Automotive Logistics & Supply Chain Europe 2025 - “Adapt and deliver, together: Co-creating an agile, win-win automotive supply chain”
Welcome to the recap blog for Automotive Logistics & Supply Chain Europe 2025, returning to Bonn, Germany, from March 18-20. Now in its 22nd year, this flagship event unites over 450 automotive logistics professionals - spanning OEMs, tier one suppliers, logistics providers and tech innovators.
March 31
Peter Hörndlein, managing director of vehicle logistics at Volkswagen Group Logistics, took to the Red Sofa at ALSC Europe 2025 in Bonn to discuss how VW is building a resilient, flexible and sustainable vehicle logistics network across Europe and globally.
He said VW aims to shift more outbound logistics to rail powered by green electricity, despite capacity constraints. The OEM is also aiming to increase electrification of road transport, with investment in battery-electric trucks accelerating as compatible trailer solutions improve.
Watch the full Red Sofa interview below!
March 28
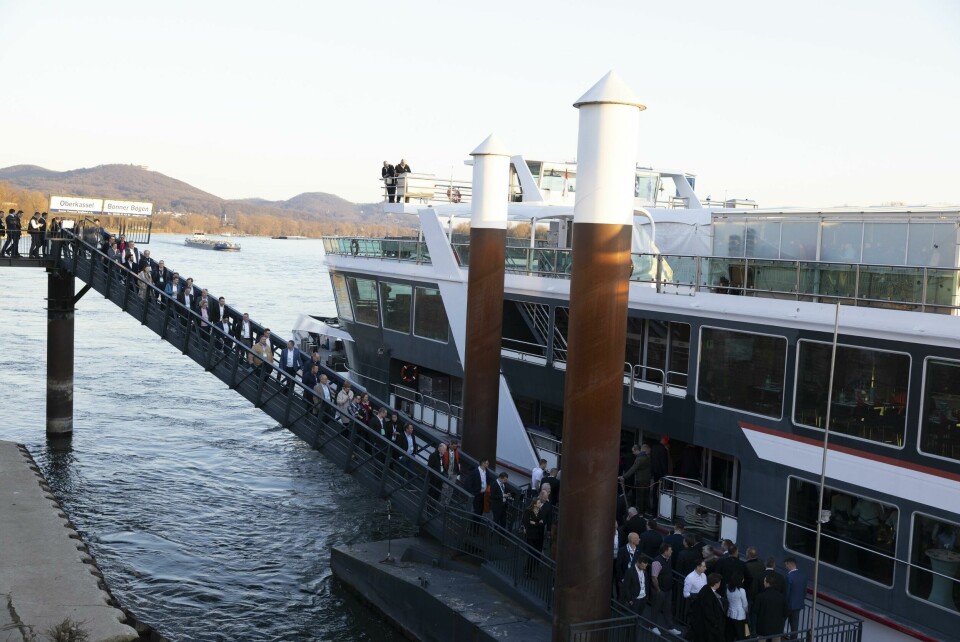
Don’t have the time to scroll down our blog for the most important insights from the event? Don’t worry - we’ve compiled them all here!
Read our conference wrap-up for insights shared on empowering talent and diversity for a digital future, taking digitalisation and AI from pilots to scalable tools, using collaboration to boost agility in a volatile market, improving sustainability and using packaging as a competitive tool, and focusing on supply chain resilience.
March 25
In its transition from an in-house 4PL model to a more collaborative structure with local plant-level logistics responsibility, GKN Automotive is focusing on maintaining a central core team for strategic alignment.
Chris Payne, global logistics director at GKN Automotive said there is a critical need for data sharing and two-way visibility with logistics providers to proactively manage disruptions. He said the ambition to move towards real-time shipment visibility is driven by customer expectations and the “Amazon effect”.
Watch his full Red Sofa interview now.
March 25
Next to take to the Red Sofa was Jean-Marc Carlicchi, vice-president of supply chain engineering at Renault Group. He sat down to discuss how the OEM is using operational control towers to enhance visibility and decision-making across inbound and outbound logistics.
Watch the full interview here!
March 25
In our first Red Sofa interview from ALSC Europe 2025, Nadine Philipp, vice-president, sustainability supplier network at BMW Group, outlined the company’s comprehensive approach to decarbonising its global supply chain.
Philipp, who opened day one of the conference with a keynote presentation on supply chain decarbonisation at BMW, said that sustainability is a business imperative. She said that BMW sees sustainability not only as a responsibility but as a critical success factor, balancing environmental, social, and economic goals even during challenging times.
Watch the full Red Sofa interview below, and stay tuned for more interviews to come!
March 24
While the event may be over, there are plenty more insights and interviews to come!
In the meantime, watch the wrap-up video from day two of the event here.
March 20
Final panel: Stronger together how collaboration is redefining supply chains
We wrapped up the exciting event with our final panel with a discussion on partnerships, transparency, and long-term collaboration in logistics.
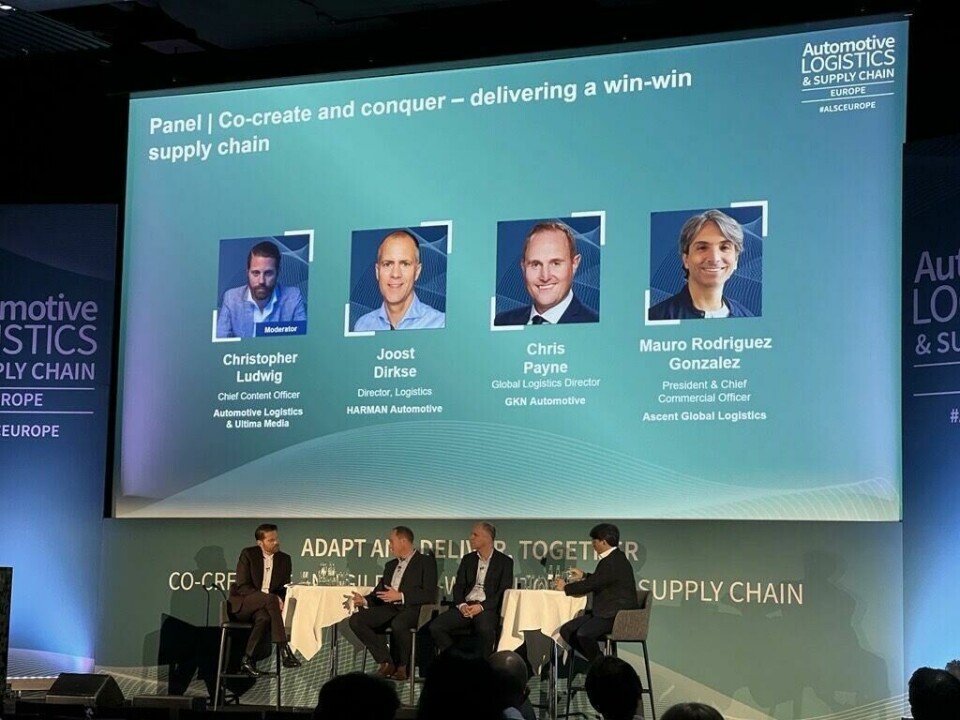
Chris Payne, global logistics director at GKN Automotive, highlighted how balancing centralised network design with local execution has helped improve efficiency. However, he stressed that true collaboration with logistics providers goes beyond cost negotiations. “If we don’t set clear expectations upfront, we’ll always end up firefighting,” he said, explaining how GKN’s approach ensures proactive rather than reactive logistics management.
Joost Dirkse, director of logistics at HARMAN Automotive, echoed this, emphasising the role of 4PL partnerships in providing real-time visibility, data analytics, and process optimisation. “Our 4PL isn’t just a supplier; we see them as an extension of our team,” he said, pointing to data-driven decision-making as key to improving transport efficiency.
Mauro Rodrigo Gonzalez, president & chief commercial officer at Ascent Global Logistics, added that true win-win relationships require mutual investment. He stressed that logistics partners need to be seen as strategic allies rather than transactional vendors. “If we’re only considered a cost centre, then no one wins,” he said. He also highlighted how AI and predictive analytics are helping logistics providers anticipate demand spikes and react faster.
The conversation turned to forecasting and supply chain resilience, with all panellists agreeing that imperfect data shouldn’t be an excuse for lack of collaboration. Dirkse admitted that logistics teams often hesitate to share forecasts if they’re not 100% accurate, but noted that even partial information is better than none. “A quick phone call can prevent a crisis—sometimes we just need to communicate better,” he said.
Finally, the panellists agreed that embracing new technology, strengthening trust, and being proactive will define future success. As Payne put it, “We need to be brave—if we don’t take risks, we’ll never drive change.”
March 20
The roadmap for a cleaner, more advanced road freight network
The session on decarbonising road freight featured Dr Andreas Kammel, vice president alternative drivetrains at TRATON, who laid out a compelling case for why battery-electric trucks (BEVs) will dominate long-haul freight. While many in the industry assume short-haul distribution is easier to electrify, Kammel argued that long-haul trucking offers the best business case for BEVs, due to high mileage, energy cost savings, and the potential of megawatt charging infrastructure.
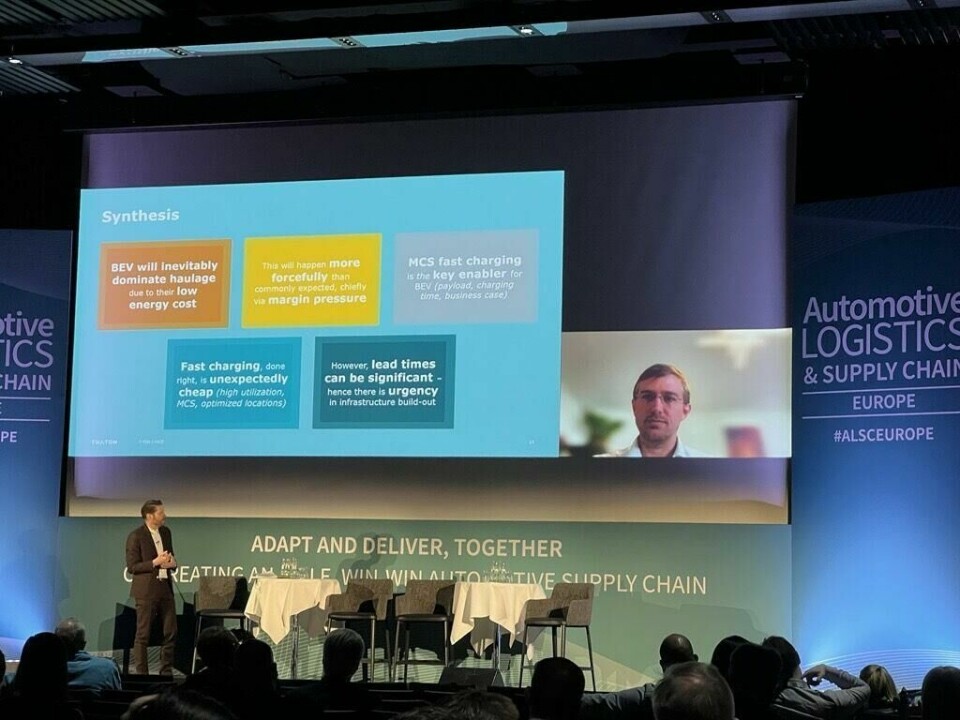
“The key to making BEVs work isn’t just about better batteries—it’s about cheap, high-speed charging,” he said, explaining that megawatt charging will allow trucks to refuel during mandatory rest breaks without losing productivity. He also highlighted that autonomous driving will further strengthen the BEV business case, as eliminating driver costs will make energy efficiency even more critical.
Kammel dismissed hydrogen as a niche solution, pointing out that even if green hydrogen were free in European ports, transport and distribution costs would still make it too expensive for mainstream trucking. Instead, TRATON is investing heavily in BEV infrastructure, including a joint venture to roll out 10,000 high-power charging points across Europe.
While challenges remain, Kammel was clear: the transition to electric road freight is not a question of if, but when.
March 20
Workshop on future-proofing battery packaging
Philip Bitterman, editor-in-chief of neue verpackung, a sister publication to Automotive Logistics, led a dynamic workshop exploring the evolving role of battery packaging in sustainability, cost efficiency and safety. “Packaging is not just about protection – it is about enabling a more resilient supply chain,” he emphasised. The discussion focused on the delicate balance between safety and sustainability, particularly in handling new and damaged lithium-ion batteries.
Participants debated the impact of standardisation, with one speaker noting that customised packaging for every vehicle model increases waste and costs. A key takeaway was the need for modular, reusable packaging, especially as EV demand fluctuates unpredictably. One example was Renault’s switch from expanded polystyrene to reusable polypropylene packaging, significantly reducing waste.
Cost optimisation was another focal point, with global battery supply chains facing volatile demand and regulatory inconsistencies. A participant from CATL highlighted the role of automation in reducing costs, but acknowledged that OEMs have vastly different requirements, complicating standardisation. “The challenge isn’t just finding efficiencies – it’s making collaboration attractive,” one attendee remarked.
On temperature management, discussions raised more questions than answers. Fire risk, regulatory constraints and evolving materials create complexity, with some advocating for steel containers, while others explored lighter, multi-material alternatives.
The consensus? Early-stage packaging integration, cross-industry collaboration and data-driven design are essential to future-proofing battery logistics. “Packaging must evolve – because the industry isn’t slowing down,” Bitterman concluded.
March 20
Packaging as a supply chain enabler
Julian Brandt, research scientist at Fraunhofer Institute, underscores the often-overlooked power of packaging in supply chain strategy. “No goods move without packaging,” he asserts, yet it remains an afterthought in product development. Brandt argues that packaging should be integrated from the outset, balancing cost, sustainability and efficiency. He highlights emerging technologies, such as AI-driven load tracking and sensor-enabled packaging, which optimise material flow and reduce waste. Comparing packaging innovation to consumer technology, he states, “If smart devices can optimise our daily lives, why can’t smart packaging revolutionise logistics?” His call to action: view packaging not as a cost but as an enabler of efficiency and innovation.
The panel discussion builds on this, emphasising the need for a paradigm shift in packaging perception. Andy Winebloom, senior manager at Toyota Motor Europe, explains how centralising Toyota’s packaging management across its European plants has cut costs and improved efficiency. “Before, each plant acted independently, often designing multiple packaging solutions for the same part,” he says. “By standardising and consolidating expertise, we have reduced waste, improved consistency for suppliers and significantly lowered development costs.”
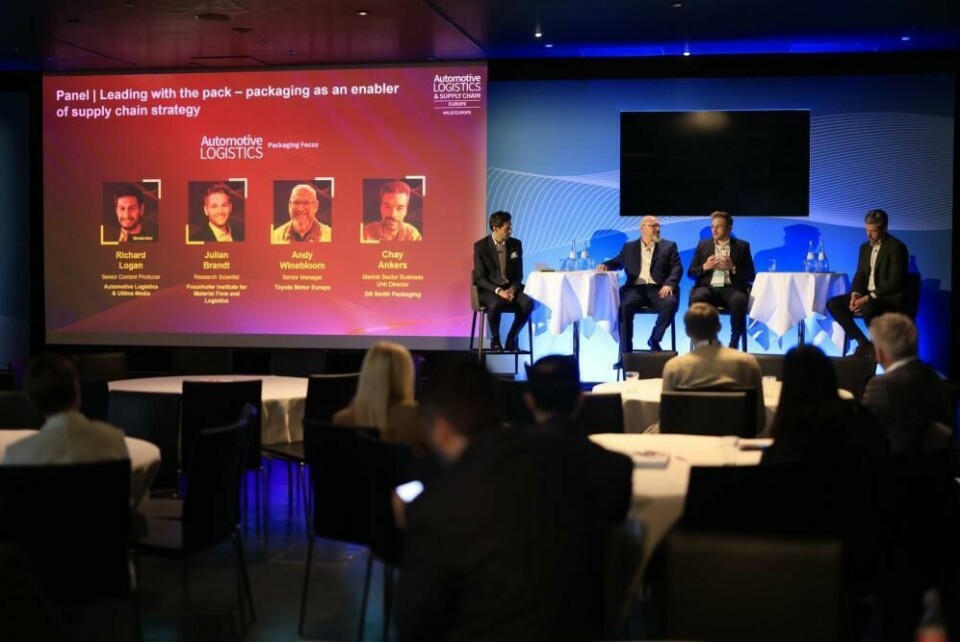
Chay Ankers, market sector business unit director at DS Smith, agrees but points out a lingering industry challenge: packaging is still treated as an afterthought. “Most companies see it as a commodity – something to be sourced as cheaply as possible,” he says. “But that mindset is costing them agility, efficiency and money in the long run.” He advocates for earlier collaboration between packaging specialists, OEMs and Tier 1 suppliers, stressing, “If we’re involved at the start, we can design solutions that optimise the entire supply chain – not just protect the product.”
Toyota’s real-world examples highlight the potential of a proactive approach. Winebloom shares how rethinking part design for packaging efficiency has driven significant savings. “We told our designers, ‘If you cut this wheel arch moulding into two pieces, we can double our packaging density,’” he recalls. “By looking at total supply chain costs, not just production costs, we secured a smarter, more cost-effective solution.”
As the industry faces regulatory pressures and the rise of EVs, the panel agrees that data-driven decision-making, sustainable materials and integrated design thinking will shape the future of packaging. “The shift to electrification changes everything,” Winebloom notes. “We’ll have heavier parts, weight-limited trucks and new logistical challenges. Lightweight materials and recyclability will be key.”
March 20
”If we don’t create space for women to step up, we’ll never unlock their full potential”
The ’Empowering Women in Automotive Logistics’ panel delivered a candid and inspiring discussion on progress, challenges, and the need for cultural shifts in the industry.
Dr Gisela Linge, vice president global logistics at Autoliv, reflected on how attitudes towards women in leadership have evolved over the last two decades. “When I first stepped into a leadership role, I was told I only got it because of a quota—despite there being no quota at all,” she shared. While progress has been made, she emphasised that true diversity goes beyond numbers. “We need different perspectives to tackle the complexities of today’s industry—it’s not just about gender, it’s about diversity of thought.”
Jennifer Coulter-Lissman, CEO & president of NTG Supply Chain Solutions, highlighted historical barriers that have kept women in administrative roles rather than leadership. While opportunities have expanded, she stressed the importance of male allyship. “A true ally sees you as an equal and actively supports your growth,” she said, noting that mentorship should evolve into genuine sponsorship and advocacy.
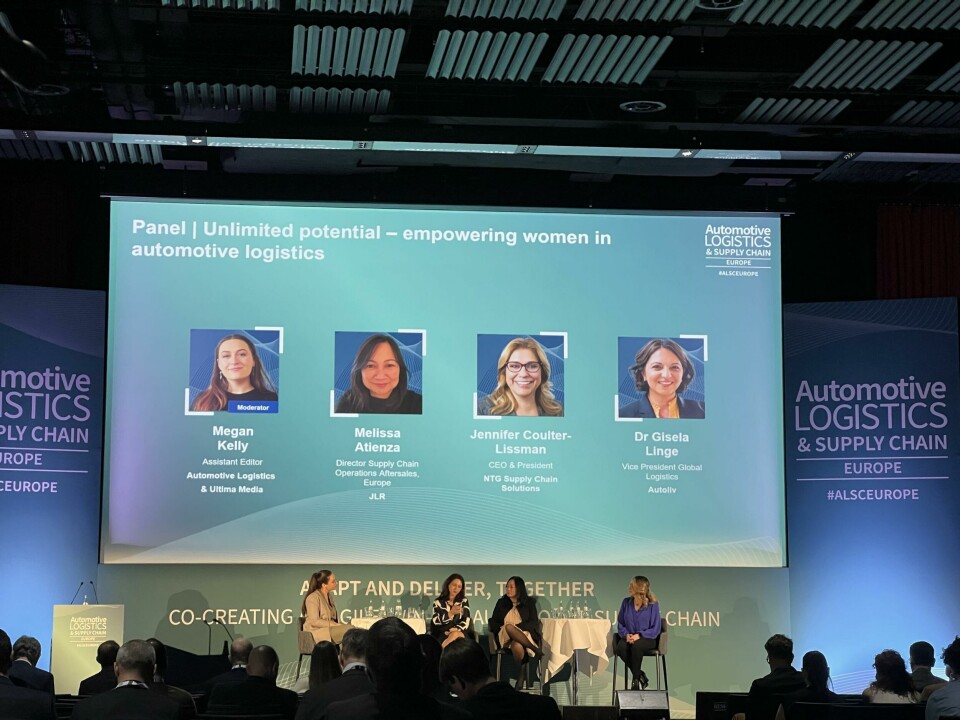
Melissa Atienza, director supply chain director | Europe (Aftersales) at JLR, spoke about the cultural differences in workplace inclusion, pointing out that some regions still struggle to break traditional gender roles. While JLR has strong policies supporting women in leadership, she noted that real change only happens when inclusivity becomes ingrained in company culture. “If the mindset isn’t there, even the best DEI initiatives won’t stick,” she said.
The conversation also touched on imposter syndrome and self-doubt. Linge urged women to take risks, sharing how she almost turned down her current role due to a lack of logistics experience. “I had 20 seconds to say yes—and I did. The truth is, men apply for jobs when they meet 60% of the criteria. Women feel they need 100%. That mindset has to change.”
”The truth is, men apply for jobs when they meet 60% of the criteria. Women feel they need 100%. That mindset has to change,” Dr Gisela Linge
The panel ended on a call to action—greater representation must come with real support, visibility, and opportunities for women to lead with confidence. “The technology and talent are there,” Atienza said, “but if we don’t create space for women to step up, we’ll never unlock their full potential.”
March 20
How automotive logistics is navigating the green transition
The next session explored the realities, challenges, and opportunities of decarbonising automotive supply chains. Levent Yuksel, freight operations director at JLR, opened with a keynote on JLR’s sustainability efforts, highlighting tangible progress in alternative fuels, vehicle transport efficiency, and collaborative industry initiatives.
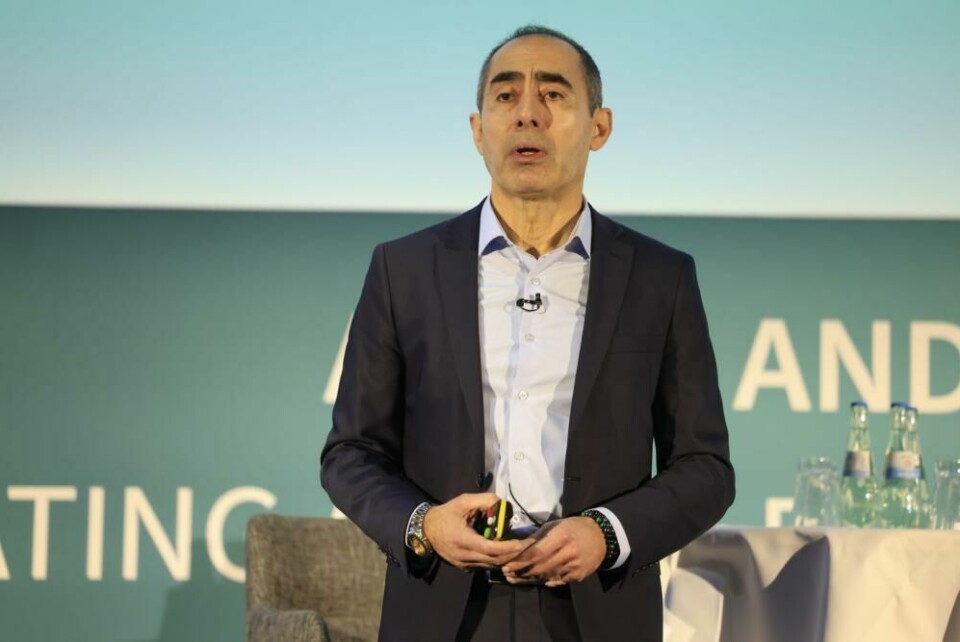
Yuksel emphasised that while electrification is the long-term goal, infrastructure limitations mean that a mix of solutions—including HVO, BioLNG, and CNG—are necessary in the transition. “We can’t wait for the perfect solution. We need to act today with what is available,” he said, explaining how JLR has already transitioned its UK dedicated fleet to a blend of alternative fuels, reducing emissions without a major financial burden.
The panel discussion, featuring Andreea Serbu, senior manager, external affairs, ECG, Didier Bruneau, global supply chain director, OPmobility, and Yuksel, tackled the collaborative challenges of sustainable logistics. Bruneau acknowledged that investment in green logistics is still misaligned with short-term cost-driven procurement strategies, stating, “We source for one-year contracts, but green investments need long-term commitment.” Serbu reinforced this, arguing that sustainability must be integrated into core business models rather than treated as an add-on.
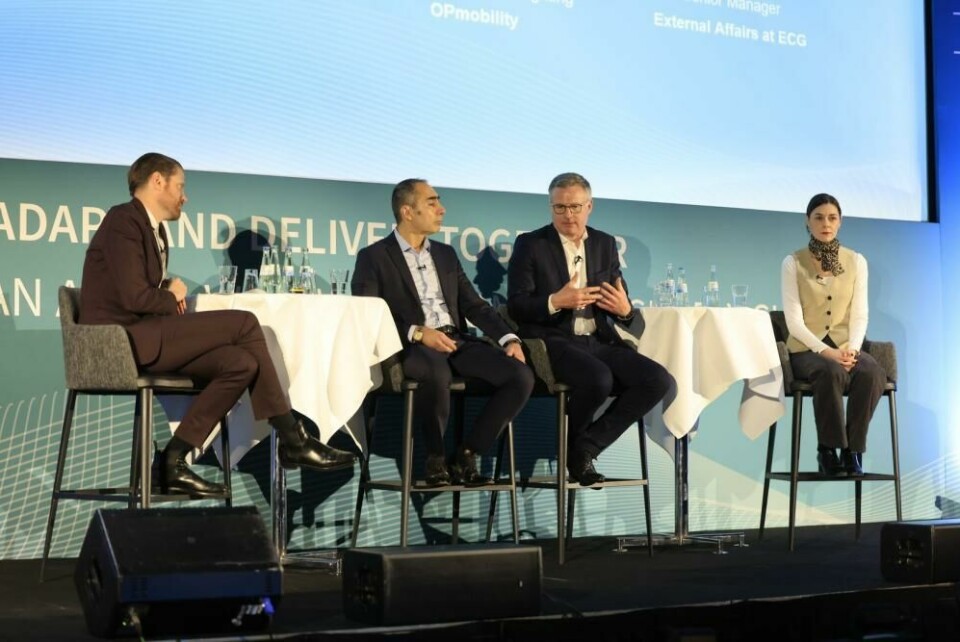
The conversation also focused on data-driven decision-making. Serbu explained ECG’s push for harmonised emissions reporting, stressing that “without accurate data, we can’t measure progress or make informed decisions.” Bruneau admitted that many companies still rely on inconsistent, self-reported data from logistics providers, making meaningful emissions reduction efforts difficult.
Yuksel further added that true progress requires open collaboration between OEMs, suppliers, and policymakers.
“We talk a lot about partnerships, but now we need action. Transparency and shared responsibility are key,” Yuksel said.
March 20
Hackathon with industry leaders to solve real-world challenges
The Hackathon brought together leaders and delegates to tackle real-world challenges in supply chain digitalisation, AI integration, and decision automation. Across different teams, participants explored how data, technology, and people can work together to drive transformation.
Dr Gisela Linge from Autoliv led discussions on data governance and AI-driven decision-making, emphasising the need for quality data, clear ownership, and practical use cases. “AI is only as good as the data behind it. If we don’t fix the foundation, we can’t build anything useful,” she noted. The group also debated AI’s role in decision-making transparency, exploring ways to track and audit machine-driven recommendations.
The inbound logistics team focused on how AI can enhance track-and-trace capabilities for returnable packaging and real-time transport visibility. They stressed the need for AI to support, not replace, human decision-making, noting that “like autopilot in planes, AI should assist, but humans must remain in control.”
Another group tackled freight and transport management, outlining a vision for an AI-powered exception management system to improve ETAs and reduce inefficiencies. Fabian Pobantz from Schaeffler pushed for AI-driven analytics to automate tedious tasks, explaining that “material planners shouldn’t waste time chasing updates—they should be focused on strategic priorities.”
The session concluded that successful digital transformation requires trust, collaboration, and strong leadership buy-in. As one participant put it, “The technology is ready—now it’s up to us to use it.”
March 20
AI is useless if no one uses it correctly
We kicked off the first keynote and panel discussion with Dr Gisela Linge, vice president global logistics at Autoliv, who shared a bold vision for the future of AI-driven logistics, where automation, predictive analytics, and digital assistants will enhance efficiency and resilience.
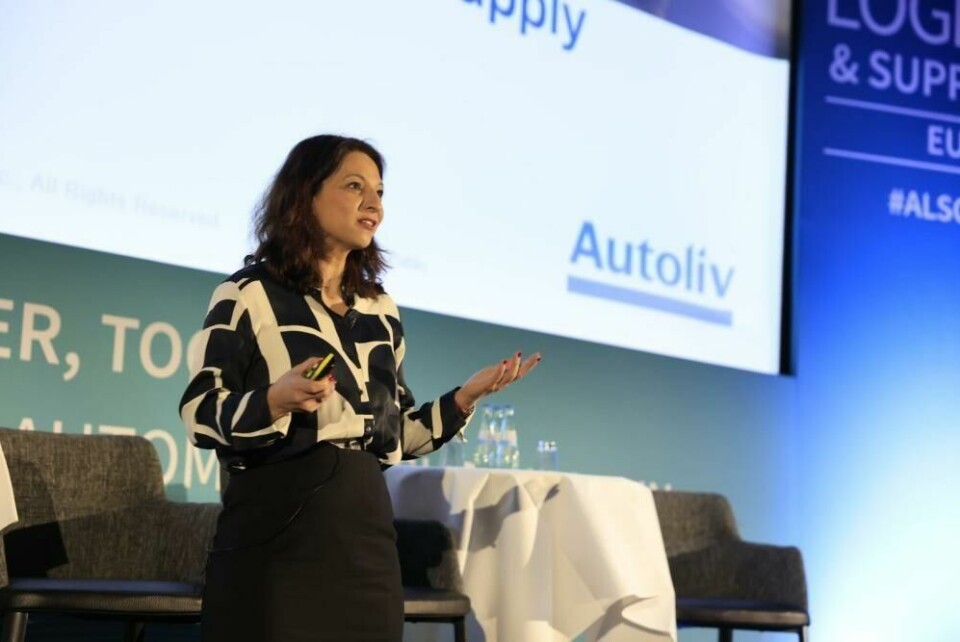
She described how AI agents and chatbots will soon handle tariff changes, supplier risks, and inventory planning in real time. “AI won’t replace us, but it will challenge us to think differently,” she said, highlighting how machine learning is already improving Autoliv’s global operations in predictive maintenance, quality control, and supply chain visibility.
“AI needs training just like any other team member. You must guide it, feed it the right data, and continuously improve it,” Dr Gisela Linge said.
The panel discussion built on Linge’s keynote, diving deeper into how AI, automation, and digitalisation are transforming automotive supply chains. Fabian Pobantz, VP of operation digitalisation & IT - supply chain and purchasing at Schaeffler, highlighted how AI is already playing a crucial role in forecasting, supply chain planning, and decision-making. He shared that Schaeffler is actively testing humanoid robots in warehousing and enabling employees to work with AI-powered chatbots to improve efficiency. “We need to upskill our workforce—not just hire new AI talent but train our existing people to use these tools effectively,” he said.
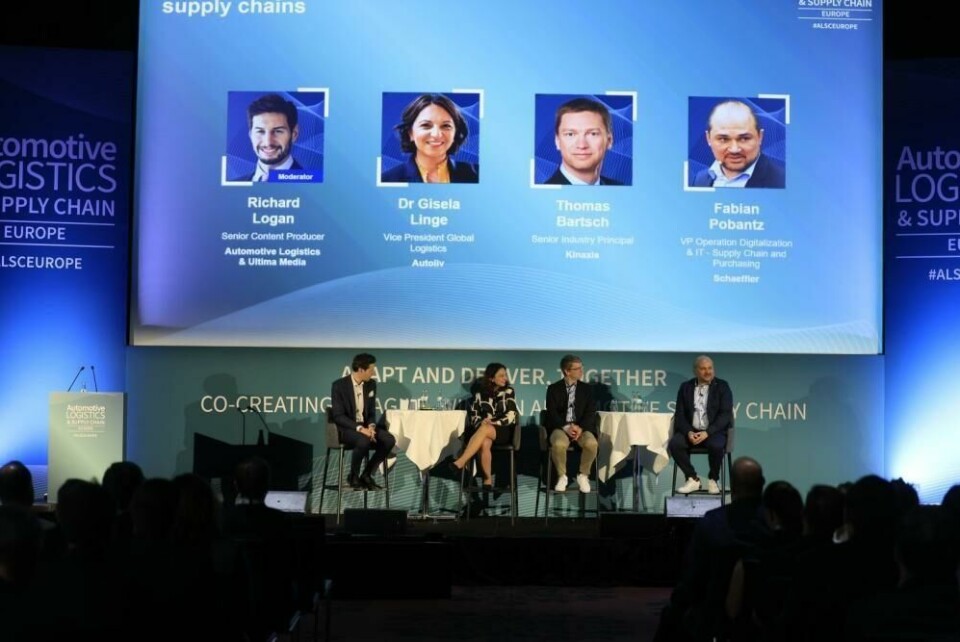
Thomas Bartsch, senior industry principal at Kinaxis, noted that automotive is behind other industries in digital transformation, largely due to its complex supplier structures and reliance on custom-built solutions. “We have been fantastic at piloting new technologies, but we struggle to scale them globally,” he said. He said that breaking down silos and integrating digital tools across the supply chain is critical to achieving agility and resilience.
Linge reinforced that digital tools are critical for risk mitigation and fast decision-making. “When tariffs change overnight, I need financial impact data in hours—not days,” she said, pointing to the power of control towers and predictive analytics.
March 20
We wrapped up the first day of the conference with a networking dinner on the river Rhine, sponsored by DP Schenker. After a day full of insights on supply chain management, automation, packaging and much more, our delegates got a chance to discuss these takeaways along the beautiful river with some food and drinks!
On the second and final day, we will dive deeper into digitalisation, green logistics, supply chain, AI and much more. You will hear from experts including Levent Yuksel and Melissa Atienza from JLR, Dr Gisela Linge from Autoliv, Dr Andreas Kammel from TRATON, Chris Payne from GKN Automotive, Mauro Rodrigo Gonzalez from Ascent Global Logistics and many more. Stay tuned for more insights from today’s discussions.
Watch the wrap-up video from yesterday below!
March 19
Matthias Schmidt, European autos analyst, Schmidt Automotive Research is now closing out day one of ALSC Europe 2025 with an overview of the European market outlook.
China is now potentially intensifying its focus on Europe, Schmidt says. “We expect that to happen with ICE vehicles following these recent tariffs,” he says, adding the example of Chery delivering to the UK.
As for the biggest risks to established European players, Schmidt says: “At the moment we’re seeing Chinese OEM’s combined volumes equal that of Ford Motors Europe. We’re likely to see traditional brands with low equity exit the market.”
March 19
S&P Global highlights Europe’s slowdown as China’s auto market surges
Henner Lehne, vice president of global vehicle forecasting at S&P Global Mobility, delivered a hard-hitting keynote on the shifting dynamics of the global automotive market, outlining why Europe is falling behind, how Chinese automakers are disrupting the industry, and why full EV adoption is further away than many expect.
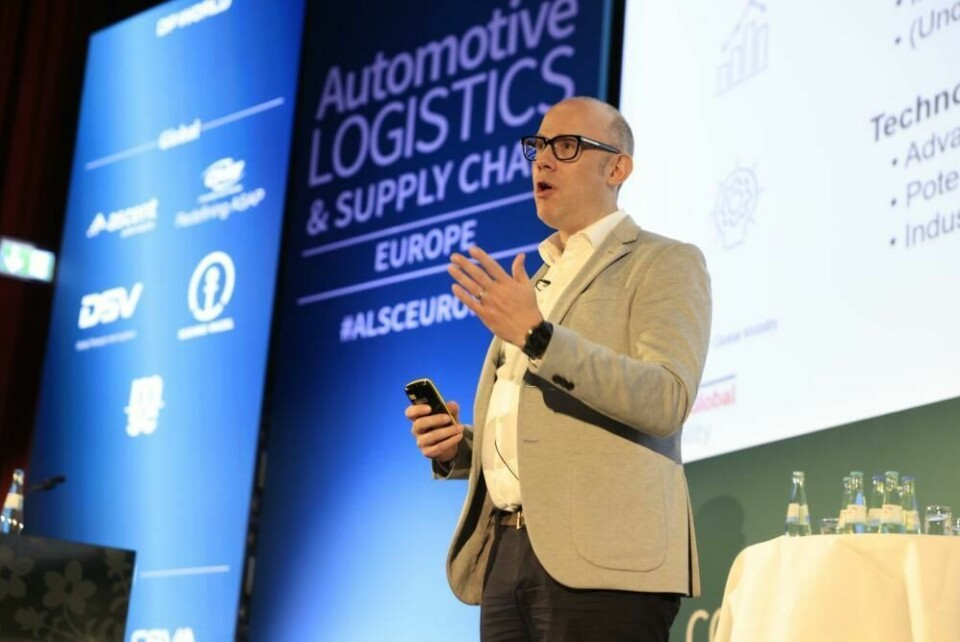
Lehne pushed back against the 2035 zero-emission vehicle target, arguing that full electrification is unlikely before 2040. “The vehicles are coming, the battery infrastructures are coming, but charging costs and affordability remain major obstacles,” he said. While Europe has made visible progress, Chinese automakers are aggressively expanding into the region, offering vehicles that are not only cheaper but also more technologically advanced. “It’s not just about price,” he warned. “It’s about what these vehicles can actually do.”
He pointed to import tariffs and protectionist measures as a short-term response, but was clear that these will not stop China’s rise.
“Chinese OEMs have a long-term strategy,” Lehne said. “They will push, they will grind, and they are not thinking in two-year cycles—they are thinking in ten.”
Discussing global vehicle demand, Lehne noted that while the industry is recovering from COVID-19 and supply chain disruptions, Europe is the only major region expected to see a decline in vehicle sales this year. While markets like China, India, and North America continue to grow, consumer confidence in Europe remains low due to economic uncertainty, rising costs, and unclear regulatory policies.
On electrification, he noted that battery costs are declining by 8% annually, and solid-state batteries could be commercially viable by the end of the decade. However, EV adoption is slowing in key markets like the US and Europe, and many OEMs have already delayed or cancelled planned EV investments. “The reality is, electrification will come—it’s just a matter of time,” he said. “But if you ignore it now in favour of short-term wins, you’ll find yourself in real trouble in five years.”
Lehne closed by stressing resilience and long-term planning as critical for automotive companies. “Now is the time to put on the warm jacket and make sure you are safe,” he said. “If you don’t, you will have problems very soon.”
March 19
Packaging regulations and the implications for the automotive industry
Now, Eric Lambert, managing director, GALIA, and chairman, ODETTE is walking us through changing packaging regulations, and their impact of the automotive industry.
He said that there are many regulations coming into place this year, although not all of them are new – some were in previous regulations but were not implemented correctly in some regions of Europe.
From now until 2030 there are more ambitious targets, with requirements for total 70% weight of the waste recycles. 55% plastics, 30% wood.
Lambert says: “There is no reason not to start, the sooner the better. Start to investigate how to eliminate empty space, protections that are not needed, and materials that are not recyclable.”
He adds that ensuring materials are recyclable does not simply mean “recyclable in theory”. It requires companies to ensure the material is recyclable at scale - if not, it will be banned.
March 19
Inside Aston Martin’s supply chain overhaul and the fight to keep up
For the next session, we are joined on stage by Martin Corner, executive director of supply chain management & logistics at Aston Martin who offered a candid look at the challenges of running a low-volume, ultra-luxury supply chain and made it clear that despite producing far fewer cars than mainstream OEMs, the complexity of Aston Martin’s supply chain is immense.
“People assume that because we build 7,000 cars a year, the supply chain must be straightforward. The reality is very different,” Corner said.
Unlike high-volume manufacturers that benefit from scale and established supplier relationships, Aston Martin operates in a highly specialised, fragmented environment. The impact of supply disruptions is far greater—losing a few multi-million-pound hypercars in production can have the same financial consequences as thousands of mass-market vehicles.
Rob Gammon, director of operations planning & vehicle logistics at Aston Martin, then shared just how chaotic things were when he and Corner joined in 2022. Suppliers were in arrears, planning was disjointed, and teams were in constant firefighting mode just to keep production running. “Every day, the question was the same—do we have enough parts to build cars?” he recalled. Without structured planning or real-time visibility, even minor supply issues could bring production to a halt.
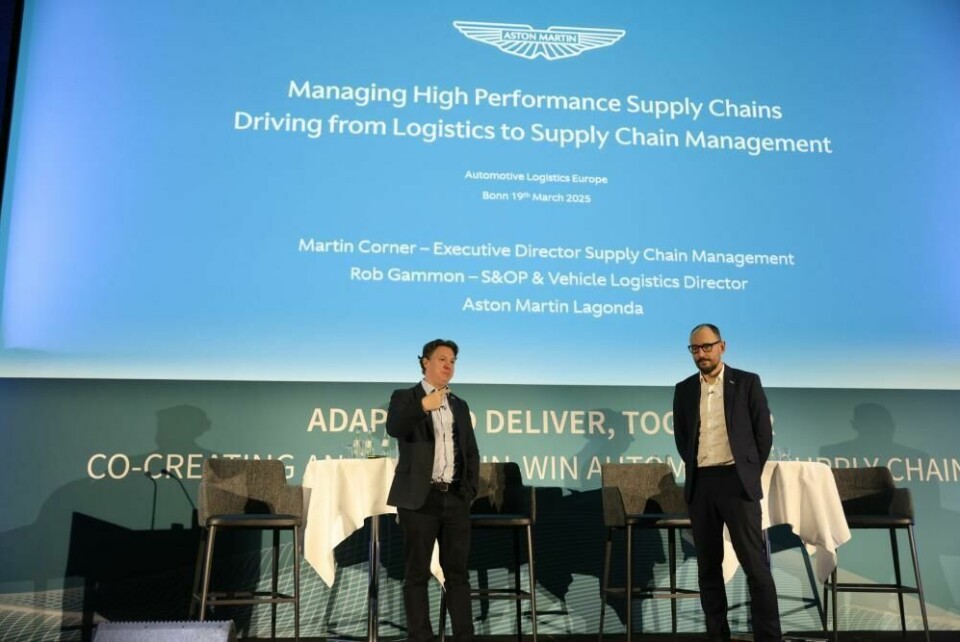
One of the biggest challenges was managing customisation and complexity. Each Aston Martin is highly personalised, which meant hundreds of variations for components like wiring harnesses. Gammon explained how a slight adjustment to the production schedule could suddenly leave them missing key parts, bringing everything to a standstill. “The system might say we have plenty of stock, but if it’s for the wrong spec, it’s useless,” he said.
To fix this, the team went back to basics—improving stock management, refining safety buffers, and working more closely with suppliers. The biggest breakthrough was implementing a structured sales and operations planning (S&OP) process, giving the company better long-term visibility and control. “We’ve gone from scrambling to solve today’s problems to planning 18 months ahead,” Gammon said.
The improvements have been significant. Right-first-time production has increased by 290%, part shortages have dropped by 80%, and logistics costs are down 15% year on year. Most importantly, supply chain is now a strategic function, involved in high-level decision-making rather than just reacting to crises.
But there’s still more to do. Corner admitted that compared to larger OEMs, Aston Martin is still catching up. “We’re trying to compete in the Tour de France on a penny farthing,” he joked. However, with stronger foundations in place and a focus on long-term supply chain resilience, Aston Martin is moving towards a more stable, efficient, and agile operation—one that matches the prestige of its brand.
Stay tuned for more coverage!
March 19
“Do LSPs invest in advanced battery-ready warehouses now, or wait for OEMs to commit?”
We are back from lunch and straight onto our next keynote with Aleksej Krükov, general manager overseas service EMEA at CATL who offered a compelling perspective on the growing complexity of the EV supply chain and the challenges facing manufacturers, logistics providers, and policymakers alike. He painted a picture of an increasingly fragmented landscape, where regulatory barriers, transport limitations, and raw material sourcing are putting unprecedented strain on global supply networks.
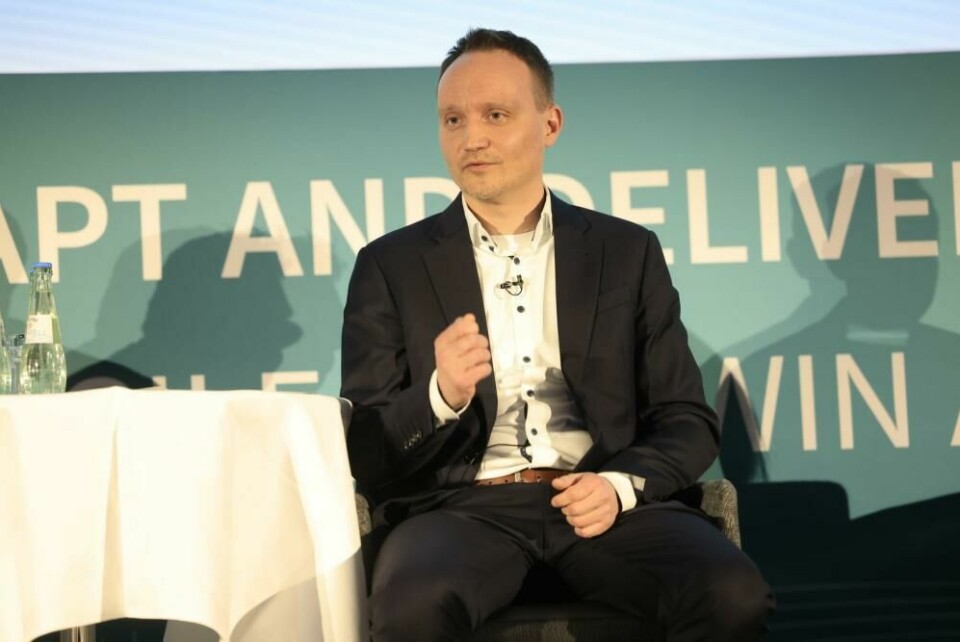
Krükov highlighted that battery logistics is not just about moving goods from A to B, but about ensuring safety, sustainability, and long-term viability. With European battery regulations tightening and EV adoption accelerating, he stressed that the industry must rethink its approach to handling, recycling, and transporting batteries. “The share of internal combustion engine vehicles will decline significantly, and by 2040, EVs will represent up to 60% of the global market. That shift brings incredible complexity, particularly in Europe,” he explained. He also pointed to the challenge of reverse logistics, noting that “Transporting a defective or end-of-life battery is significantly more complex than moving a new one.”
The panel discussion built on these themes, with Lucie Dobeer, head of automotive at Unipart, and Antony Yiakoumi, global account director – automotive at DSV, discussing how supply chains must adapt to uncertainty, regulatory shifts, and infrastructure demands.
Dobeer stressed that logistics is the biggest barrier to EV adoption, urging LSPs to move from being transactional service providers to strategic partners. “We keep talking about collaboration at every conference. Now is the time to actually do it,” she said, adding that early involvement in planning, rather than responding to tenders, is crucial.
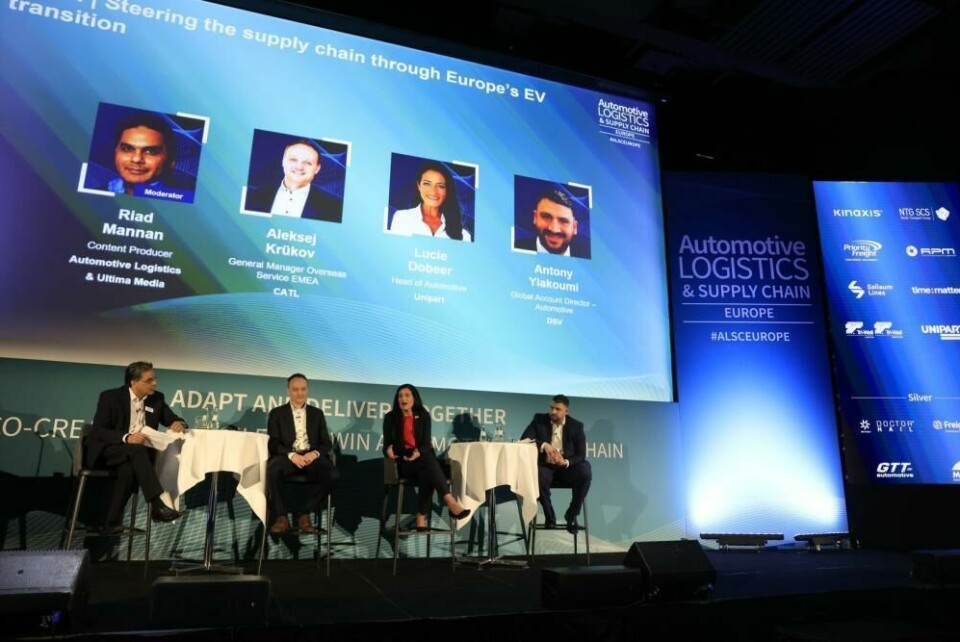
Yiakoumi highlighted the unpredictability of government incentives and its impact on demand forecasting. “It’s a chicken-and-egg scenario. Do LSPs invest in advanced battery-ready warehouses now, or wait for OEMs to commit?” He pointed to regionalisation and decentralisation as key solutions, reducing reliance on long-haul transport and improving supply chain flexibility.
Krükov reinforced the importance of standardisation and digitalisation, arguing that harmonised regulations and real-time data sharing will be essential to overcoming supply chain bottlenecks. “If trust is the issue, technology can provide the transparency we need,” he said.
March 19
Lunch break!
It’s now time for the long-awaited lunch break, sponsored by Priority Freight, where delegates will get a chance to connect, enjoy the sunny Bonn and prepare for the second half of the conference.
When we come back, we will hear from Aleksej Krükov from CATL, Martin Corner and Rob Gammon from Aston Martin, Olivier Cotillard from Renault Group and many more.
March 19
Finished vehicle logistics hackathon: sustainability, capacity management, and long-term partnership
In an interactive hackathon, Martina Graser, director, material planning and logistics at Ford, Frits Mehrtens, interim managing director at RPM, and Levent Yuksel, freight operations director, JLR lead delegates in discussing co-creating innovation for finished vehicle logistics.
Graser lead a group discussing transparency and visibility, addressing questions on collaboration, leveraging technological solutions, and building these into different systems. The group found that there is a strong need for collaboration, because shipping lines are using different technological software and systems and there is sometimes a lack of interoperability.
The delegates in Graser’s workshop agreed there is a need for an agreement on what information everyone in the network should share. It was suggested that the industry could begin to democratise key pieces of data, such as promises made to the customer, so that everyone in the network can work together to achieve the goals.
RPM’s Mehrtens lead a discussion on capacity management, both in the medium and long-term and the risks in that, and the balance between asset and non-asset. His group discussed the impacts of volatility and consumer uncertainty, with pressures from tariffs and taxes and environmental rules and regulations. The consensus among the group was that mergers and acquisitions will likely be a key trend.
JLR’s Yuksel focused his group on increasing sustainability in FVL, and how we share assets, leverage green corridors, and share investment and responsibility for reducing emissions. His group discussed the issues around charging and loading capacity of BEVs, as well as investment versus contract duration. The group said that open ended contracts could be a better and open investment, and a more beneficial long-term solution.
March 19
“Automation is great, but only when built on a solid foundation of best practices”
Karel Verpoorten, head of parts supply chain from Toyota Motor Europe gave an insightful keynote on the growing complexity of managing service parts in today’s evolving automotive landscape. He highlighted Toyota’s commitment to efficiency, sustainability, and customer satisfaction, underlining the company’s sell one, buy one philosophy to keep supply chains lean and adaptable. “Nobody wants a pallet of windshields—so why should we push our customers to order one?” he explained, reinforcing Toyota’s approach to just-in-time inventory management to reduce excess stock and improve agility.
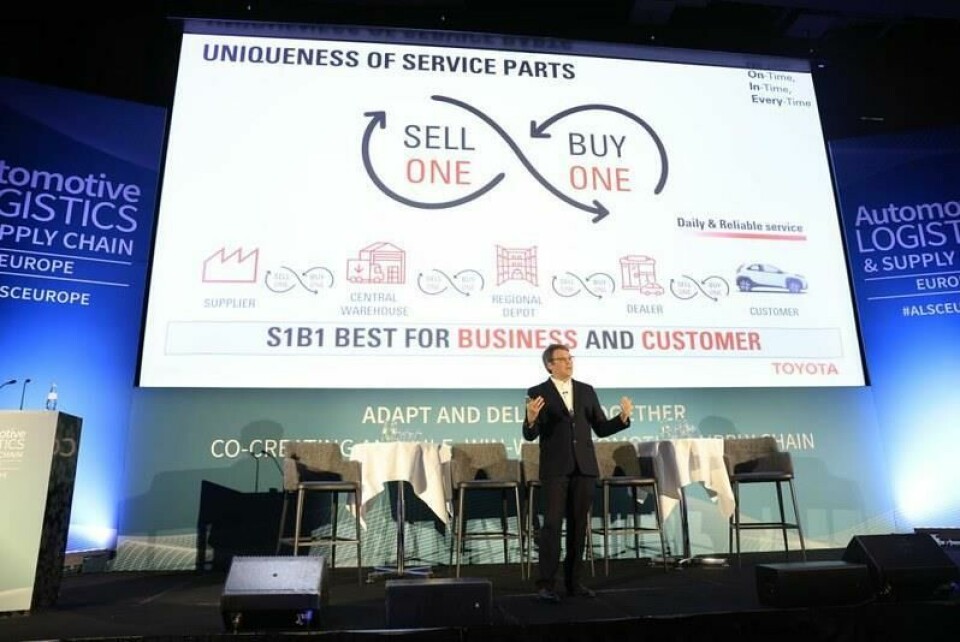
Verpoorten also stressed that electrification and new vehicle technologies present fresh challenges for service parts logistics. With multiple powertrain options—including hybrids, battery-electric vehicles, and hydrogen—Toyota is navigating a wider variety of service parts while ensuring long-term availability for older models. This growing complexity, he noted, requires greater collaboration with suppliers and logistics partners to keep supply chains efficient.
The panel discussion brought together leading voices in service parts logistics, including Katharina Uribe Casillas, SVP, dead of global automotive at Kuehne+Nagel; Markus Ramirez, managing director global sales – automotive solutions at FedEx; and Friedhelm Glormann, COO at LKQ DACH.
Casillas highlighted the need for agility as the industry transitions from ICE vehicles to hybrids and electric models, pointing out that service parts supply chains must accommodate an increasing number of SKUs. “The parts spectrum will explode over the next few years, and logistics needs to be ready,” she said, emphasising the challenge of balancing cost efficiency with high service levels. She highlighted the role of AI-driven decision-making in optimising transport modes and inventory holding costs, allowing companies to shift seamlessly between air, sea, and road freight depending on demand fluctuations.
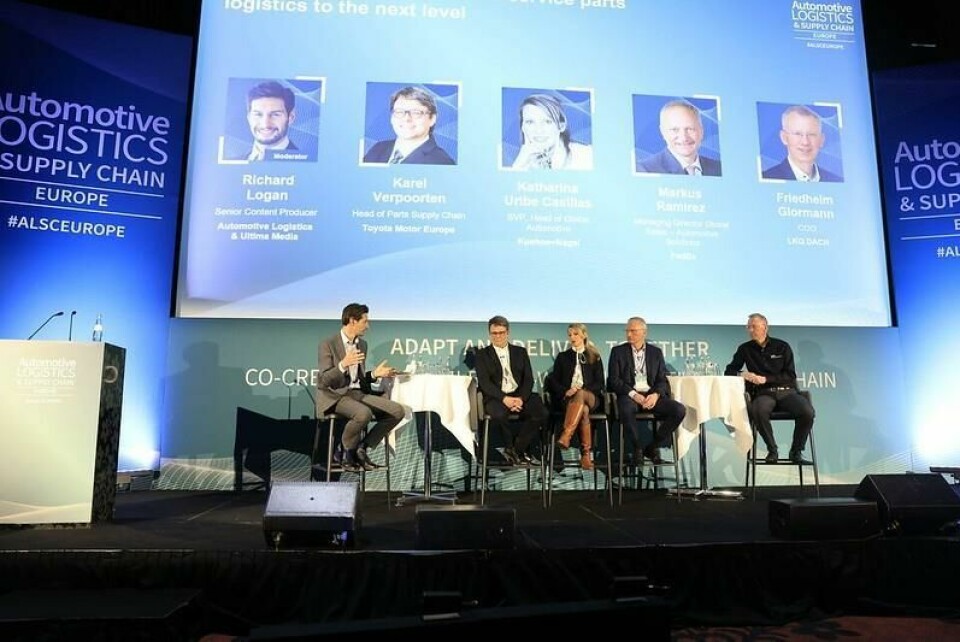
Ramirez built on this by discussing how visibility and digitalisation are reshaping the industry, explaining that predictive analytics and AI-powered tracking tools are enhancing real-time shipment monitoring and reducing unnecessary express freight costs. “If a dealer knows exactly when a part will arrive, they can plan their workshop accordingly, eliminating the need for excess stock,” he explained, pointing to FedEx’s predictive ETA tools as a game-changer in aftermarket logistics efficiency.
Explaining how LKQ delivers parts to 125,000 garages across Europe, sometimes up to six times per day, Glormann provided a perspective from the independent aftermarket. He noted that while OEMs focus on dealer networks, independent service providers play a critical role in keeping vehicles on the road. “We are the other half of the service market,” he said.
Verpoorten cautioned against automation inefficiencies, explaining that Toyota’s approach is to optimise processes first, then implement automation where it adds real value. “Automation is great, but only when built on a solid foundation of best practices,” he said.
March 19
How supply chains are closing the gap between planning and execution
This session opened with a keynote from Agnieszka Kubiak, senior vice president logistics at Brose Group, who painted a stark picture of today’s volatile supply chain landscape. Gone are the days when stable and predictable demand allowed for traditional planning methods. “The world is changing, and we must change with it,” she stated, explaining how fluctuations in demand, rapid globalisation, and increasing competition from Asian manufacturers are reshaping the European market.
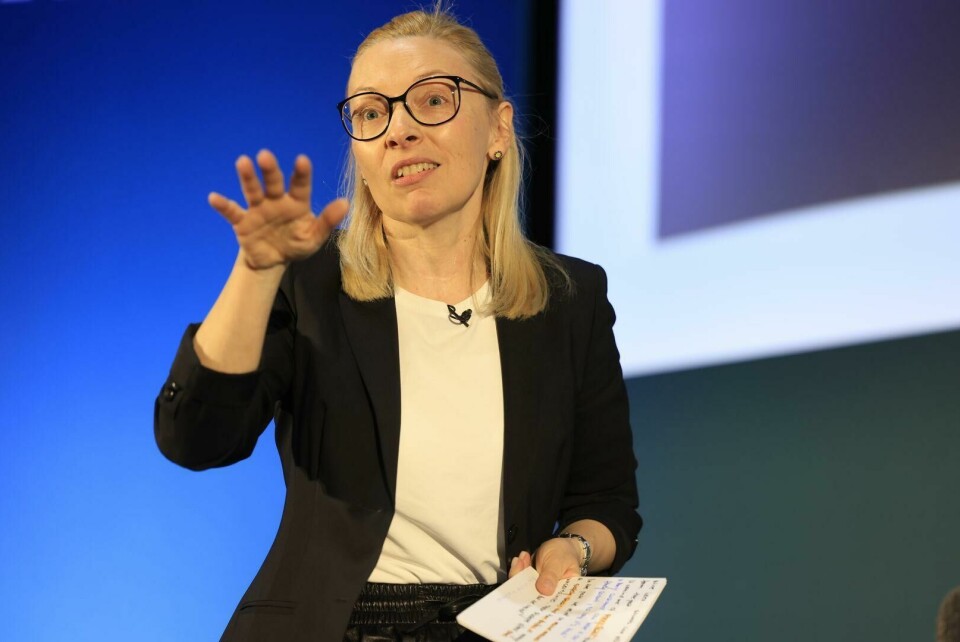
Kubiak acknowledged that past supply chains operated with buffers and reactive measures, but today’s environment demands proactive, data-driven decision-making. She highlighted the shift towards real-time visibility and scenario planning, allowing companies to anticipate risks before they escalate. However, she also stressed that technology alone is not the answer—collaboration and strong leadership are just as crucial. “ We need to stop relying on unrealistic security and instead take calculated risks,” she added, reinforcing the need for flexibility in both supply chain operations and decision-making.
The panel discussion built on these themes, with Kai Olschner, global VP supply chain engineering at DP World, stressing the importance of end-to-end collaboration and visibility across supply chains. He explained how logistics providers must work more closely with OEMs, suppliers, and service partners to predict disruptions and respond faster. “We became extremely reactive and collaborative like never before,” he said, highlighting how technology is helping companies gain better oversight of inbound and outbound flows to reduce delays and inefficiencies.
Thomas Blank, vice president EMEA at CNW, provided a different perspective, focusing on the critical role of speed in decision-making. Operating in emergency logistics, he emphasised that long planning cycles aren’t always an option. “We don’t have time to analyse data for days. The phone rings, and we need to act immediately,” he said. While predictive analytics and AI tools provide valuable insights, execution must be swift and failure-free. He also stressed that communication is just as important as data. “The most important tool in our IT suite is the phone,” he added, reinforcing the value of human judgement and rapid coordination in high-pressure situations.
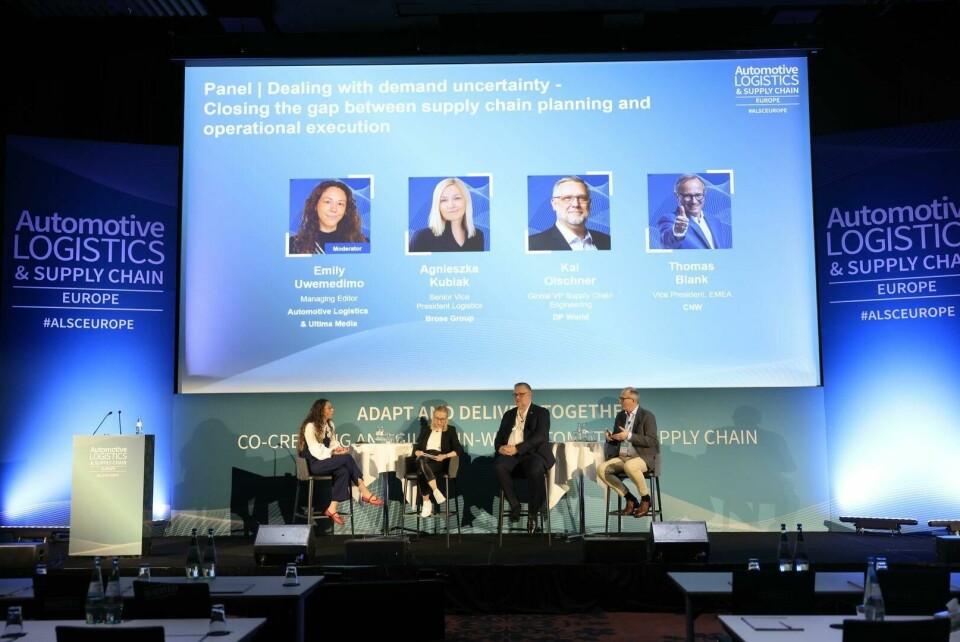
The discussion then turned to data overload and how companies can extract meaningful insights from vast amounts of information. Kubiak noted that while AI and predictive analytics are becoming essential, they are only useful when combined with strong leadership and decision-making structures. She referenced a lesson from an astronaut trainer at the European Space Agency: “The most important currency isn’t information – it’s time.” This point resonated across the panel, as speakers agreed that having access to data is one thing, but acting on it in a timely and effective manner is what truly drives success.
The panellists spoke about the need for flexibility in supply chain operations, whether through alternative transport modes, universal production lines, or decentralised decision-making. The ability to adapt quickly and make strategic decisions in real-time will be key to navigating future disruptions.
Stay tuned for more live updates!
March 19
Moving with the times: transparency, efficiency and resilience
In stream two, we have a keynote and panel session on transforming Europe’s finished vehicle supply chain, with experts from VW, Sallaum Lines, ECG, and INFORM.
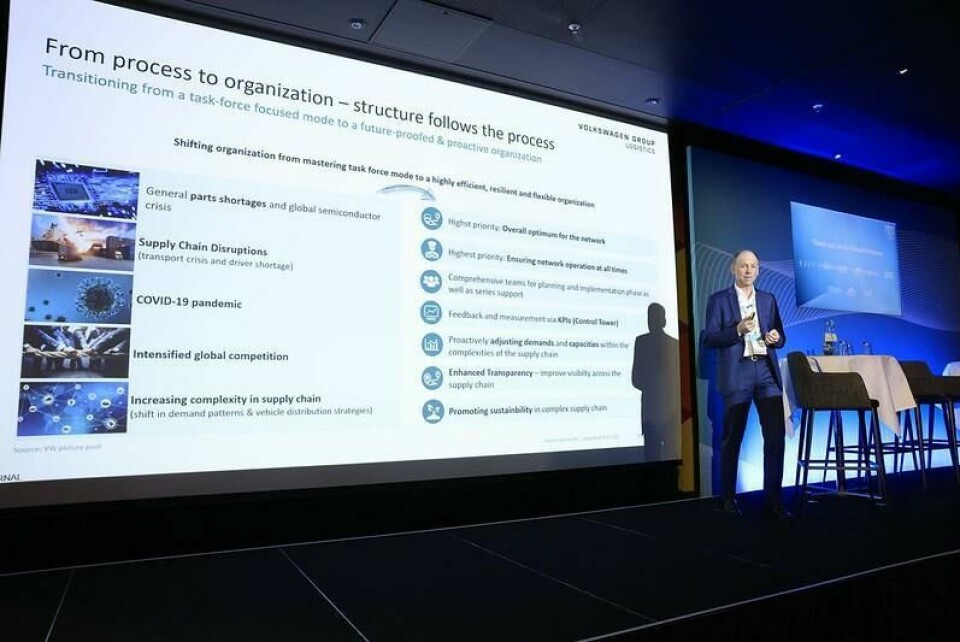
Peter Hörndlein, managing director vehicle logistics, Volkswagen Group Logistics, Volkswagen Group says that to move with the times, transparency, efficiency and resilience are crucial, with process-oriented monitoring for proactive planning.
“We are constantly rethinking our network, which is a great factor for us in order to achieve resilience,” Hörndlein says.
To do this, VW looked at demand fluctuations, capacity, and using technology to better predict the landscape and share the findings with partners in the supply chain. “Especially in volatile times with a lot of discussion about tariffs, we need to adapt,” says Hörndlein. “In the past, we didn’t really exchange information frequently enough. Now we have introduced a proactive demand and capacity management, which leads to transparent updates of our volumes to our partners and indicates which areas where capacity might become tight, allowing us to operate the whole network more efficiently for our partners and ourselves.”
To address fluctuating demand and capacity in FVL, VW developed a completely new ro-ro facility in the Mediterranean which serves as a major hub and has led to a significant reduction in emissions while ensuring resilience. The carmaker is operating its own fleet of 13 vessels in the north Atlantic trade route between Europe and the US, leading to reductions in emissions of up to 26% in CO2, up to 30% in NOx, up to 60% in particulate matters, and up to 100% in Sox.
The OEM also introduced an Outbound Order Book, which gives everyone easy access to volume forecasts, capacities, real-time validation of responses from logistics services providers, automatic status messages based on telematics data, and short-term forecasts for better planning.
March 19
Networking break hosted by Sallaum Lines
We are now breaking into our first networking break hosted by Sallaum Lines, giving the attendees a chance for further discussions and exploring the exhibition hall.
We will be back with the upcoming session, which will delve into how manufacturers and packaging specialists are challenging the packaging status quo, focusing on material choices, product lifecycles, and technology applications to deliver cost savings and emissions reductions across supply chain and manufacturing operations.
March 19
Building a more resilient automotive supply chain: Insights from Jean-Marc Carlicchi
Now we have a presentation from Jean-Marc Carlicchi, vice-president, supply chain engineering, Renault Group, who is discussing how the OEM is reimagining its supply chain ecosystem.
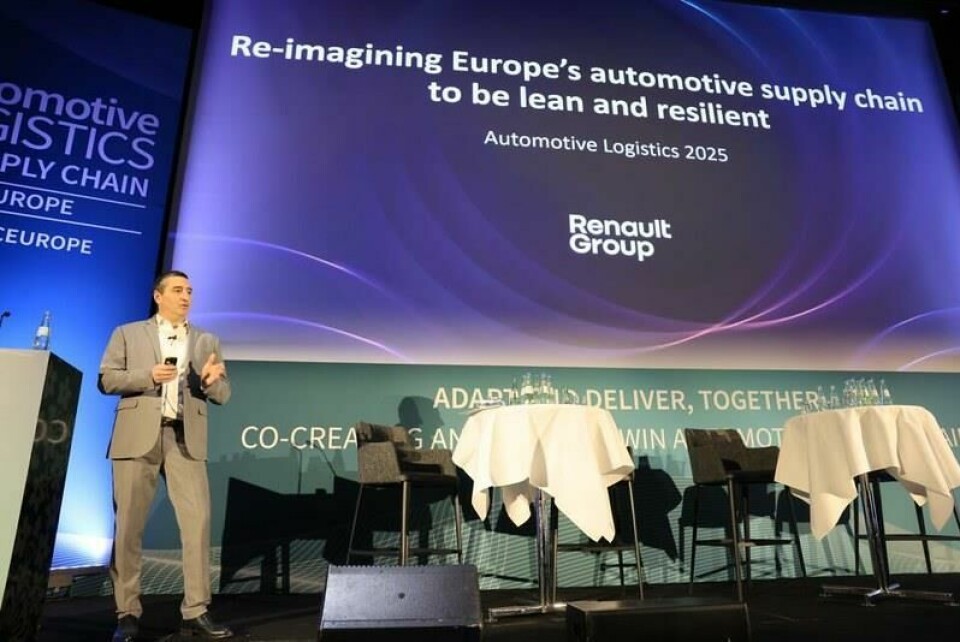
Carlicchi says that recent elections, tariffs and protectionism, as well as new players coming into the market, is creating a lot of uncertainty, but he says that the industry needs to continue to focus on its strengths. From COVID disruptions to geopolitical tensions and supply chain shocks, unpredictability is now the new normal. Carlicchi emphasised that despite these challenges, companies must maintain economic performance, achieve decarbonization goals, and ensure customer flexibility.
“Change is our new normal. We became extremely reactive and collaborative like never before.”
He says that there are four key aspects of business that need to continue to be pushed, despite any hardships in the wider market, including financial economic performance, decarbonisation by 2030, ensuring customer flexibility, and maintaining satisfaction in SCM management. He says: “There is no going back on this, it is our duty.”
In response to ongoing market headwinds, the industry has become highly reactive and collaborative. “When you don’t know what to do, you ask others,” he says. “You talk, and you become more transparent.” This shift has led Renault to introduce AI-driven supply chain operations control towers for both inbound and outbound logistics, alongside business continuity plans to enhance visibility and resilience.
Now, Renault is taking the next step towards greater collaborative visibility with its Supply Chain Engineering Control Tower. This end-to-end ecosystem approach integrates continuous network design, S&OP ‘what-if’ scenarios including logistics capacities, and decarbonisation as a constraint within the S&OP cycle. AI-driven decision-making, leveraging Generative AI, is at the core of this transformation. “We are moving from reactivity to a faster structural change that allows us to warn our entire ecosystem of risks,” he concludes.
Watch the Red Sofa interview we did with Carlicchi last year!
March 19
BMW’s vision for a sustainable supply chain
In the first keynote of day one, Nadine Philipp, vice president of sustainability supplier network at BMW Group, lays out the carmaker’s approach to decarbonisation.
“We have a clear and 360-degree approach [to decarbonisation],” she explains, detailing BMW’s goal to reduce CO2 emissions by 40% by 2030 across the entire value chain. Electrification is a crucial step, with half of BMW’s fleet expected to be fully electric by the end of the decade. Yet, as Philipp points out, EVs present a paradox: while they reduce emissions in use, they significantly increase emissions in production, particularly in high-voltage battery manufacturing.
To mitigate this, BMW focuses on three key materials – aluminium, steel and battery raw materials – which account for the bulk of supply chain emissions. “Deploying green energy is our biggest lever, responsible for nearly 50% of CO2 reduction potential,” she notes. BMW also seeks to increase the use of secondary raw materials, though availability and quality remain significant hurdles.
Logistics, though a smaller contributor to emissions, is not overlooked. Philipp acknowledges that decarbonising transport remains costly, but BMW is gradually introducing sustainability criteria into its freight tenders and exploring alternative fuels and recyclable packaging. “Logistics measures today are still expensive, but we need to work together to drive this transformation,” she says.
Beyond emissions reductions, Philipp states: “Verification is crucial.” The carmaker conducts annual third-party audits to ensure compliance, though she concedes that this approach is resource-heavy and unsustainable at scale. The solution, she argues, lies in digital ecosystems like Catena-X, which would standardise data sharing and increase transparency across the supply chain.
Despite the costs, BMW is unwavering. “We trust that it’s business-critical for the future,” Philipp asserts. The pressure is not just environmental but also regulatory and social.
March 19
The state and play of automotive logistics in Europe
We’re kicking off the first full day of the ALSC Europe 2025 conference with an introduction from Christopher Ludwig, chief content officer, Automotive Logistics, who is painting a picture of the European automotive logistics and supply chain market and the challenges it is facing.
“Managing uncertainty is now perhaps the central task of many supply chain leaders and actors in this room,” Ludwig says. He adds that predicting and planning on a stable and consistent basis is constantly being challenged, due to trade challenges, tariffs and geopolitical uncertainties.
A competitive, lean and resilient supply chain is the aim, and planning and integrating with supply chain partners is the way to achieve that, he says. “We are facing some other structural challenges that you’re all aware of. Tariffs, protectionism and new competition constantly coming into the market. Be ready with plan A, B, C and D, and integrate with your partners to do that. Co-creating an agile win-win supply chain will be an overriding theme.”
But Ludwig stresses that the outlook for the market is not all negative.
”Despite the challenges we’re facing in the European automotive industry, we firmly believe this is a thriving sector and that by working together we’ll continue to see success and drive transformation,” he says.
Ludwig also emphasised that market fragmentation persists, even as acquisitions—such as DB Schenker and DSV—reshape the logistics landscape. However, no single logistics provider dominates the sector, making partnerships and collaboration essential.
According to our latest European Automotive Logistics Market Report 2025-2035, the shape and dynamics of the market indicate there is still growth in the sector. Ludwig says: “I’m not going to pretend this accounts for every tariff and uncertainty ahead, it doesn’t, but in terms of post-Covid and the capacity challenges we had, we do see stabilisation. We do see a basis for continued growth in this sector.”
March 19
We wrapped up the pre-conference day yesterday at the ALSC Europe, taking place in Bonn this year! The day saw over 450 automotive and supply chain leaders join together to discuss our key theme of this year’s event: ’ Co-creating an agile, win-win automotive supply chain’ with a special focus on automotive packaging.
After the insightful conversation with some of our leaders including Saba Azizi from CATL and Martin Corner from Aston Martin. We moved on to our Welcome Cocktail Reception for further networking and catch up with peers, and prepare for the important discussions ahead. The next few days promise engaging conversations on transparency, digitalisation, and sustainability, alongside deep-dive sessions on service parts logistics, finished vehicle logistics, and, for the first time, automotive packaging.
Watch the wrap-up for the pre-conference day below!
March 18
Championing change: Diversity in the automotive supply chain
A panel featuring Saba Azizi, head of service network and business development, EMEA Aftersales at CATL, Harry Kwaki Davies, senior global supply manager, Automotive Industry and Martin Corner, executive director supply chain management & logistics at Aston Martin, discussed the transformative power of diverse teams.
Corner mentioned that diversity is a strategic necessity across all business areas, not just a supply chain concern: “Crucially important, I don’t think it goes just for the supply chain. I think it’s across all parts of any business.” He pointed out how varied backgrounds spark creativity, vital in today’s unpredictable market, yet acknowledged recruitment hurdles. “Supply chain… has struggled to attract diversity… operations tends to mean presenteeism, long hours, lots of pressure,” he said, describing the field’s traditional image as a barrier.
Davis offered a practical fix, urging HR to craft inclusive job descriptions: “Your job descriptions must say regardless of nationality, gender, sex, origin, whatever. Focus on people’s skills capability rather than unnecessary criteria.” Azizi shared how diversity at CATL shaped a digital after-sales system, noting, “The diverse team… can see one problem from different angles.” Corner recalled a Nissan team of 50 people from 24 nationalities—a “powerhouse” that excelled strategically. Davis, reflecting on his path from Ghana to Europe, added a personal angle: “I was willing to learn new cultures, understand perspectives,” highlighting adaptability as a strength.
Fostering inclusion demands action. Davis called for intentional leadership: “Be intentional… ask for workforce statistics” to track progress. Azizi emphasised empowerment, saying, “We need a place for everyone’s voice,” while Corner pushed to reframe supply chain roles as strategic: “Make it a business orchestration function, not just logistics.” The session underscored a clear truth: diversity isn’t optional—it’s the key to resilience and innovation in the automotive supply chain’s future, achieved by dismantling biases and redefining how the industry works.
Tomorrow, we will be diving into more insightful sessions with speakers like Nadine Philipp from BMW who will spotlight innovative approaches to logistics challenges, Jean-Marc Carlicchi from Renault Group, who will dive into how technology and data layers, including digital control towers and AI, can bolster supply chain resilience, Peter Hörndlein of Volkswagen Group who will address the intricacies of finished vehicle logistics, focusing on cost optimisation and sustainability, alongside insights from other experts in the field.
Stay tuned for more highlights on the live blog here!
March 18
Adapt and deliver, together: Co-creating an agile, win-win automotive supply chain
The ALSC Europe event opens at a critical juncture for the industry. Against a backdrop of economic uncertainty, geopolitical shifts, evolving trade landscapes and rapid technological change, the need to adapt and deliver together has never been more urgent. This week, industry leaders and experts will dive into transparency, digitalisation, AI, resilience, flexibility, carbon reduction, packaging and capacity planning – all essential to shaping a more agile, competitive and collaborative supply chain.
“At a time of rapid change, the most important asset for automotive supply chains isn’t just technology, AI or digitalisation – it’s people. The industry needs to attract, develop and retain the best talent to navigate complexity and drive success,” says Christopher Ludwig, chief content officer at Automotive Logistics & Ultima Media, who moderates today’s pre-event forum and networking session.
The forum kicks off by tackling a crucial foundation for supply chain transformation: talent, diversity and leadership. Building a workforce that can thrive in today’s fast-changing, multipolar environment requires strong leadership, inclusive hiring and a culture that values diverse perspectives. Supply chains are not just evolving through technology and process improvements – they are being shaped by people with the skills, vision and adaptability to drive change.
“We’re not talking about diversity for the sake of quotas. We’re talking about ensuring that the best talent – regardless of gender, background or nationality – can flourish and contribute to a truly agile and competitive automotive supply chain,” Ludwig adds.
As the afternoon progresses, the focus will shift to networking, where speakers, attendees and sponsors will come together to connect, exchange insights and build relationships that will help shape the future of the industry.
Stay tuned for live updates throughout the week on sustainability, digitalisation, packaging and women in supply chain!
March 13
Recap: Brose’s Agnieszka Kubiak on strengthening supply chain resilience
With supply chain disruptions becoming more frequent and unpredictable, resilience, agility and digital transformation are more critical than ever. At ALSC Europe 2025, Agnieszka Kubiak, senior vice president logistics at Brose Group, will take the stage to discuss how industry leaders are bridging this gap using real-time data, digital tools and collaboration.
In our conversation with Kubiak last year, she discussed how Brose is using AI, real-time data and predictive analytics to enhance visibility, improve demand forecasting, and reduce inefficiencies across its supply chain. A key takeaway from our conversation was her emphasis on the need for stronger collaboration and rapid response capabilities:
At ALSC Europe 2025, Kubiak will build further and talk about how OEMs and suppliers can better manage demand volatility, enhance supply chain execution, and integrate digital tools to improve decision-making. She will also lay focus on how coordinating logistics, inventory levels and sub-tier supplier management can create a more resilient and cost-effective supply chain, even in uncertain market conditions.
Stay tuned for more speaker recaps!
March 12
Recap: JLR’s Levent Yuksel on green logistics innovation
As ALSC Europe 2025 kicks off next week, sustainability is at the forefront of industry discussions. One of the key speakers addressing this transformation is Levent Yuksel, freight operations director at JLR, who will be taking the stage to discuss how the automotive industry is transforming green logistics into the most competitive option.
Levent has been instrumental in JLR’s journey towards a carbon-free future, and we previously spoke with him about the company’s strategy in our in-depth interview:
Levent previously highlighted JLR’s commitment to cutting emissions across its global supply chain, focusing on multimodal transport strategies, investments in sustainable fuels, and the need for deeper collaboration with logistics providers. He also spoke about JLR’s approach to reducing its carbon footprint, from optimising freight flows to integrating rail and short-sea shipping to lower road transport dependency.
At ALSC Europe 2025, Levent will build on these themes, discussing how manufacturers and logistics providers are shifting towards sustainable transport, using eco-friendly materials, and adopting innovative packaging to meet both regulatory requirements and business needs. He’ll also dive into how emission reporting, standardisation, and strategic partnerships are reshaping green logistics to be the most cost-effective and scalable solution.
Join us at ALSC Europe 2025 as Levent and other industry leaders discuss how sustainability can drive both cost-efficiency and competitiveness in automotive logistics. Stay tuned for live updates from the session!
With Europe’s automotive industry navigating economic challenges, new regulations and tough market competition from China, ALSC Europe 2025 is all about working together and driving innovation. Over two and a half days, industry leaders will connect, share expertise and explore practical ways to streamline logistics, cut costs and hit sustainability targets.
The conference will include senior executives from leading OEMs like Volkswagen, Renault, Audi, Ford, JLR, Toyota and BMW, alongside logistics giants such as DP World, DB Schenker and Ceva Logistics. We will dive deep into critical topics like automation, rescilience planning, the battery supply chain, network design, global freight and more.
A highlight for 2025 is the new Automotive Logistics Packaging Focus, with dedicated sessions exploring innovations in returnable containers, sustainable materials and pack density engineering - key to optimising the supply chain.
From co-creation frameworks to cutting-edge digital tools, this event will be able about shaping the future of automotive logistics in Europe.
Watch the highlights from ALSC 2024 event to give you an idea of what’s to come!