BMW’s Hendrik Lang on achieving sustainable automotive supply chains
Hendrik Lang, BMW’s senior vice-president of supply chain strategy and sustainability, attended London Climate Action Week in June. He talks BMW’s successes with carbon contracts, collaboration and convincing suppliers of sustainability’s benefits. Report by Ilkhan Ozsevim
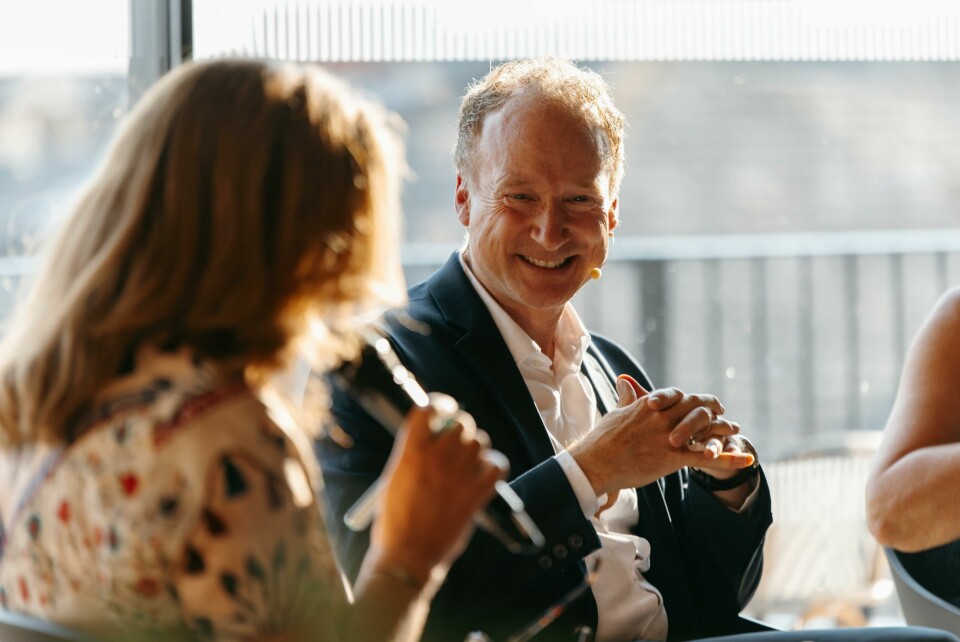
London Climate Action Week took place on the 26 June, with an interesting panel discussion on “Driving the decarbonisation of complex supply chains.” Representing BMW was Hendrik Lang, senior vice-president of supply chain strategy and sustainability.
Sustainability is not a new concept for BMW. It was the first automotive company to employ an environmental officer, way back in 1973. For decades, the carmaker has focused on improving efficiency, reducing emissions and decreasing fuel consumption. This effort culminated in the early 2000s with its ‘Efficient Dynamics’ programme, leading to the BMWi initiative, which first brought electric vehicles (EVs) to market. Then in 2013, the OEM introduced the i3, the first global premium EV, which was a success.
The experience has been invaluable to BMW, allowing it to gain substantial knowledge and experience in EVs. And now with climate considerations and technological shifts catalysing the race to net zero, the carmaker is on track to have 25 different battery EVs, including both four-wheel and two-wheel models, by the end of 2024. Its goal is for 50% of all the cars it sells worldwide, to be battery electric by 2030. In the UK, with its current targets, this percentage is expected to be even higher.
“Last year, BMW finalised 707 contracts for carbon-reduced products, resulting in a 1.7 million ton CO2 reduction in its supply chain in 2023”
Hendrik Lang, BMW Group
BMW was also one of the first automotive companies to sign the Paris Climate Agreement and commit to the 1.5-degree target, joining the Race to Zero and the Science Based Targets initiative.
BMW has the clear objective to reduce its overall carbon emissions by 40% by 2030 compared to 2019 levels, and to achieve net zero carbon by 2050. These are aspiring targets, with decarbonisation now a running thread through the entirety of the OEMs operations.
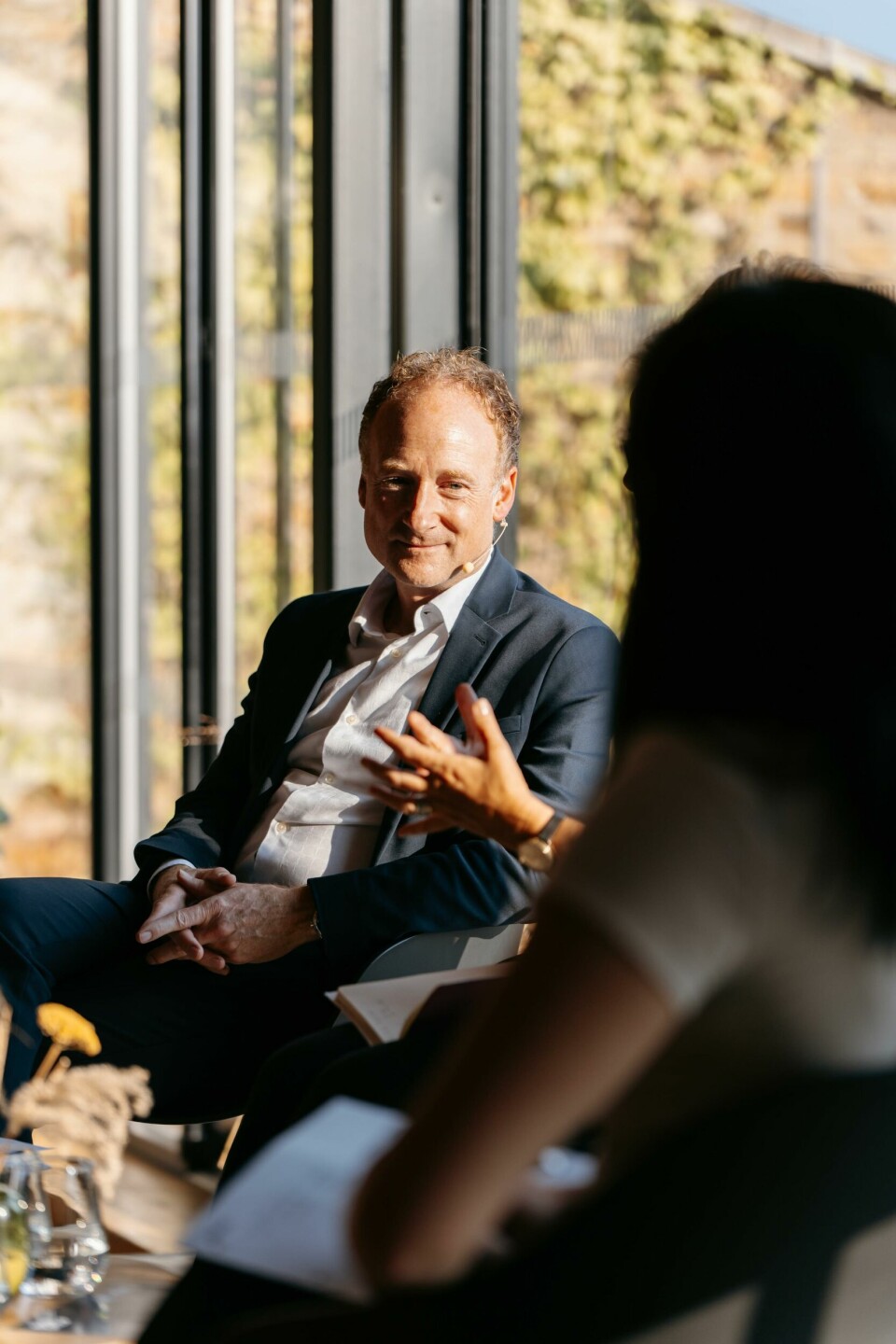
Carbon hotspots
Three-quarters BMW’s supply chain carbon footprint currently comes from the use-phase of its products, where electrification plays a crucial role. “However,” says Lang, “with electrification, the supply chain’s share of our carbon footprint will increase. If we don’t address this, it could actually negate the benefits of electrification.”
The automotive supply chain is among the most complex globally, with multiple tiers. For BMW, decarbonising its activities across this supply chain involves negotiating specific measures with suppliers to reduce CO2 emissions in its production processes. “Our primary focus areas are steel, aluminium, and batteries,” says Lang, “which constitute about two-thirds of our supply chain’s CO2 footprint. We emphasise using green energy and secondary materials to achieve our goals.”
“By working with suppliers and other OEMs, the carmaker developed a new alloy that increased the secondary material content to 70%”
Hendrik Lang, Senior Vice President of Supply Chain Strategy & Sustainability
Contracting carbon reductions
Lang said that sast year BMW finalised 707 contracts for carbon-reduced products, resulting in a 1.7m ton CO2 reduction in its supply chain for 2023. “We audit our suppliers to ensure compliance, using external auditing companies to validate these reductions,” he said. “This thorough approach allows us to report these figures in our annual report with confidence.”
There are, he said, essentially two types of suppliers: those already on board with sustainability goals and those who need more convincing.
“For the former,” he said, “negotiations are straightforward as they understand the path and technical requirements. For the latter, we must first explain the necessity of these measures, and not just for BMW; but for their relevance for the broader automotive industry.”
However, collaboration varies based on the supplier’s readiness. For instance, in the case of aluminium wheels, BMW developed a new alloy specification to allow for higher use of secondary materials, increasing from 20-30% to 70%. Lang said is required BMW to work with other OEMs and suppliers to make the alloy a new industry standard, impacting the entire aluminium wheel industry.
“We developed a new specification for an alloy that can handle more impurities, allowing the secondary material content to increase to 70% [from 20%-30%]”
Hendrik Lang, BMW Group
Collaboration for decarbonisation
Collaboration is essential at all stages of the value chain – from design to sourcing and production. A good example would be BMW’s approach to aluminium wheels, mentioned earlier. “By working with suppliers and other OEMs, the carmaker developed a new alloy that increased the secondary material content to 70%, says Lang.
This approach extends to other materials and processes across BMW’s ecosystem. Larger companies often resist changes, BMW forms cross-industry coalitions like the Responsible Business Alliance to create standards and momentum beyond what a single company can achieve. “Convincing larger suppliers that ESG and decarbonisation strategies mitigate risks from NGOs and other external pressures is another effective strategy,” said Lang.
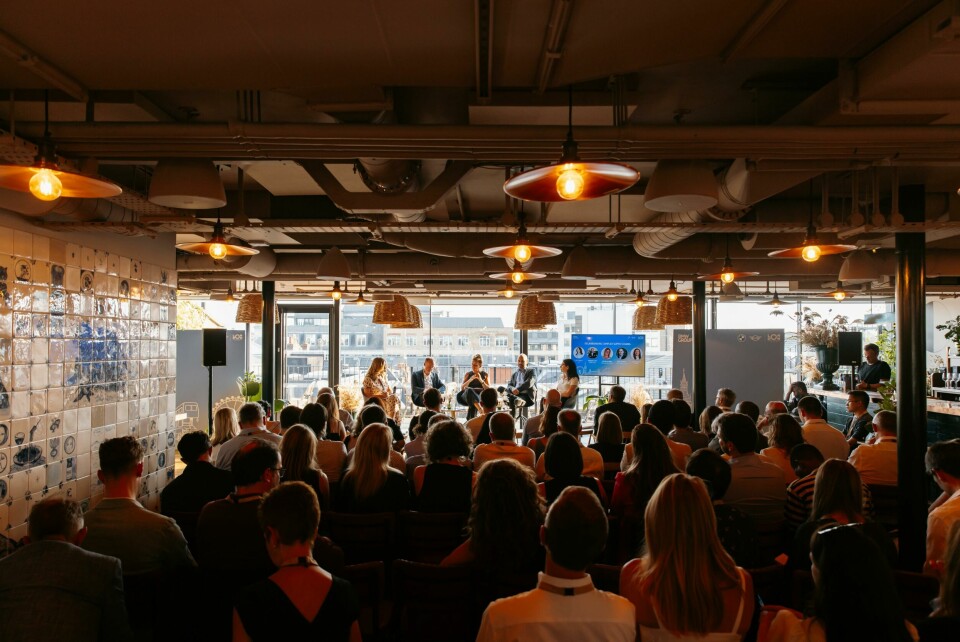
“In short, achieving our targets requires a varied approach, involving collaboration with suppliers, industry peers and standard-setting bodies to drive meaningful change throughout the automotive supply chain.
“A good example of one of these technical collaborations is our work on aluminium wheels,” he said. “Typically, aluminium wheels consist of 20%-30% secondary material. Our suppliers struggled to increase this due to impurities in available feedstock. We developed a new specification for an alloy that can handle more impurities, allowing the secondary material content to increase to 70%.”
Lang said that such sustainability successes are more than possible, but they require collaboration with other OEMs and raw aluminium suppliers to create an industrial standard. “It’s about influencing the entire industry, not just one product,” he said. “Effective collaboration also involves cross-industry initiatives and convincing larger companies that ESG and decarbonisation are risk mitigation strategies. By aligning on common goals, we can drive significant changes across the supply chain.