Protocols for protecting the restart of production in Mexico
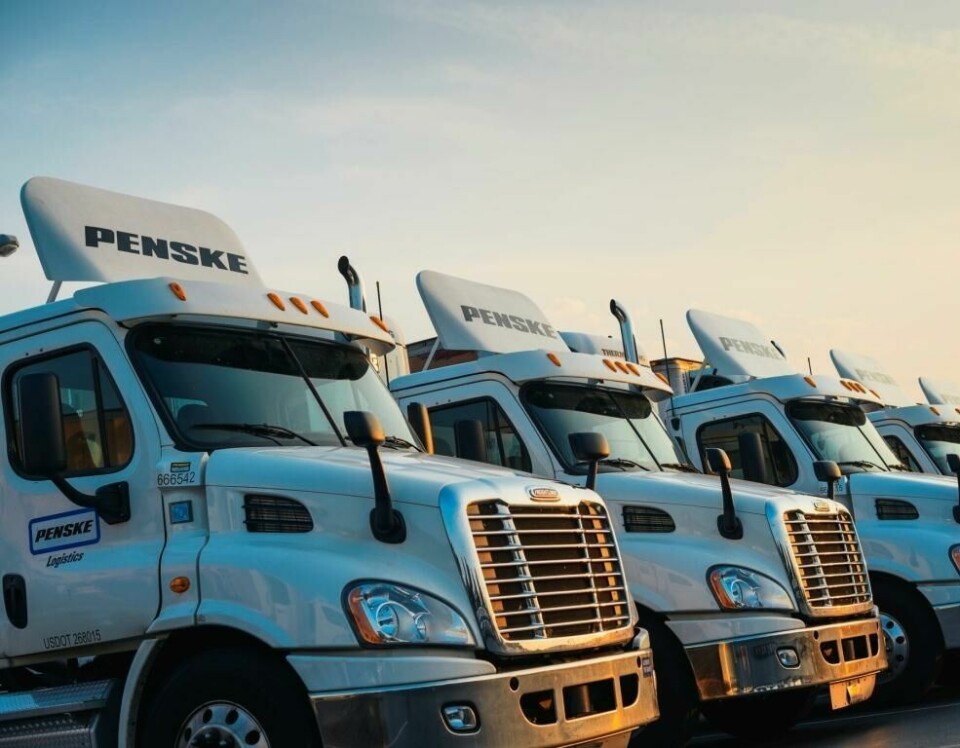
There are logistics lessons to be learned from the impact of the coronavirus pandemic on the Mexican automotive sector and Penske Logistics has quickly developed protocols for protecting the supply base and its employees. There remain some problems with certain tier suppliers unable to restart production, which is affecting manufacturing in Mexico as well as the US, but overall there has been no abnormal complexity for Penske and border flows have been maintained thanks to good visibility into supply and good collaboration between carmakers, suppliers and service partners.
“The transportation industry was deemed essential early on so our carrier partners have reported minimal issues,” said Bob Black, managing director for Penske Logistics Mexico since February this year. “What we are really seeing from state to state is the variation in [factory] reopening times or variation in companies getting the authority to reopen. I think it is pretty well known that Puebla really held firm to the June start, while other states had already allowed the process to begin and manufacturing plants to start.”
Penske Logistics has been navigating the variation in restart times subject to federal and state requirements to ensure that both it and its supplier partners are compliant with both sets of regulations, a key requirement in Mexico, moreso during a production restart that affects the health and safety of the workforce.
“I would say, certainly coming into any restart after a significant period of downtime passes, it brings its own challenges,” said Black. “With this one it is really understanding the restart requirements from a safety and regulation perspective.”
Gradual restart
Those challenges are set to continue as the infection rate in Mexico continues to rise and local parts makers are faced with liquidity issues, though most parts suppliers are now reported to have restarted production, as have a growing number of carmakers, including BMW, Ford, FCA, GM, Nissan and Toyota, albeit at a very gradual rate.
For example, last week GM started production at its engine and transmission plants in Ramos Arizpe and Silao. Vehicle assembly has also been given the go-ahead in Ramos Arizpe and Silao, subject to inbound parts supply. The restart date for operations in Toluca and San Luis Potosí is still being determined.
At the same time however, a number of carmakers on both sides of the Mexico-US border have been affected by parts supply shortages and a volatile supply chain.
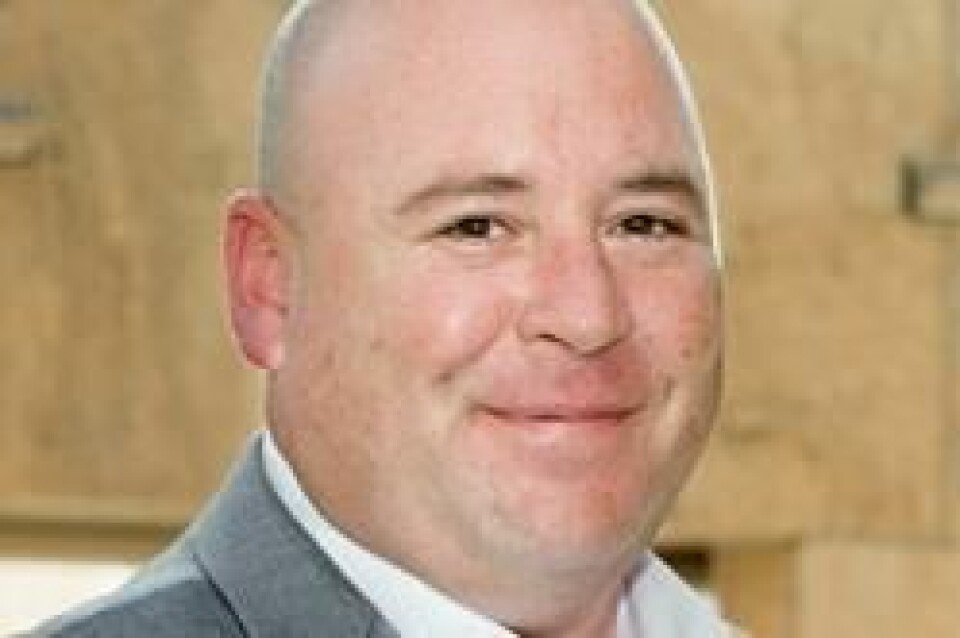
However, thanks to open collaboration between carmakers, suppliers and service providers, Penske Logistics has been able to adapt quickly as production adjustments are made.
“Within our partner-customer base and the partner-provider base that we utilise, we have seen clarity in the expected plans,” said Black. “Though we have also seen volatility and the need to react quickly and change those plans because of additional restrictions or shifts in the plant start dates.”
Critical inventory
Another lesson to be learned on the customer side from the disruption to supply in Mexico since the pandemic took hold affects inventory. Jeff Bullard, senior vice-president operations at Penske Logistics said that customers would be looking to increase banks of critical parts inventory that historically would have been in shorter supply and this will expand the services offered by logistics providers such as Penske.
“If I were making a prediction, there will be a different material flow for select commodities that are constrained,” said Bullard. “We will prebuild and probably do some buffering of inventory that we didn’t do before.”
Penske has around 100 tier supplier and OEM partners in Mexico, and upwards of 120 carrier partners, and its ability to deal quickly with adjustments to the supply chain during the pandemic relies on regular conversations with all of them, according to Bullard.
While some automotive production was maintained through the shutdown, around half of Penske’s customers and partners in Mexico were able to continue running to some extent. The return to full production for all of them relies on strong communication.
Bullard said that each customer has its own process to secure supplier readiness after a period of downtime and that those processes are robust.
“[They involve] conversations with each supplier to make sure they are prepared and, if there are issues, that the issues are being talked about and addressed,” said Bullard. “I would say we have pretty good clarity on which suppliers are having problems and which ones are more ready to provide parts to the customers’ assembly plants.”
A lesson in social distancing
According to both Black and Bullard one of the unique lessons learned from the Covid-19 crisis was how to maintain social distancing between people while still providing a product.
Black said that what really tested Penske’s expertise was ensuring that it was able to partner with customers and providers to provide a safe environment for its associates.
“A lot of activity has had to take place within social distancing and testing, and how we operate safely within these,” he said. “That was the biggest test on the front end.”
Like its customers in the country, Penske Logistics Mexico is in compliance with the requisite Health Security Self-Assessment and is approved for operations by the Mexican Social Security Institute (IMSS).
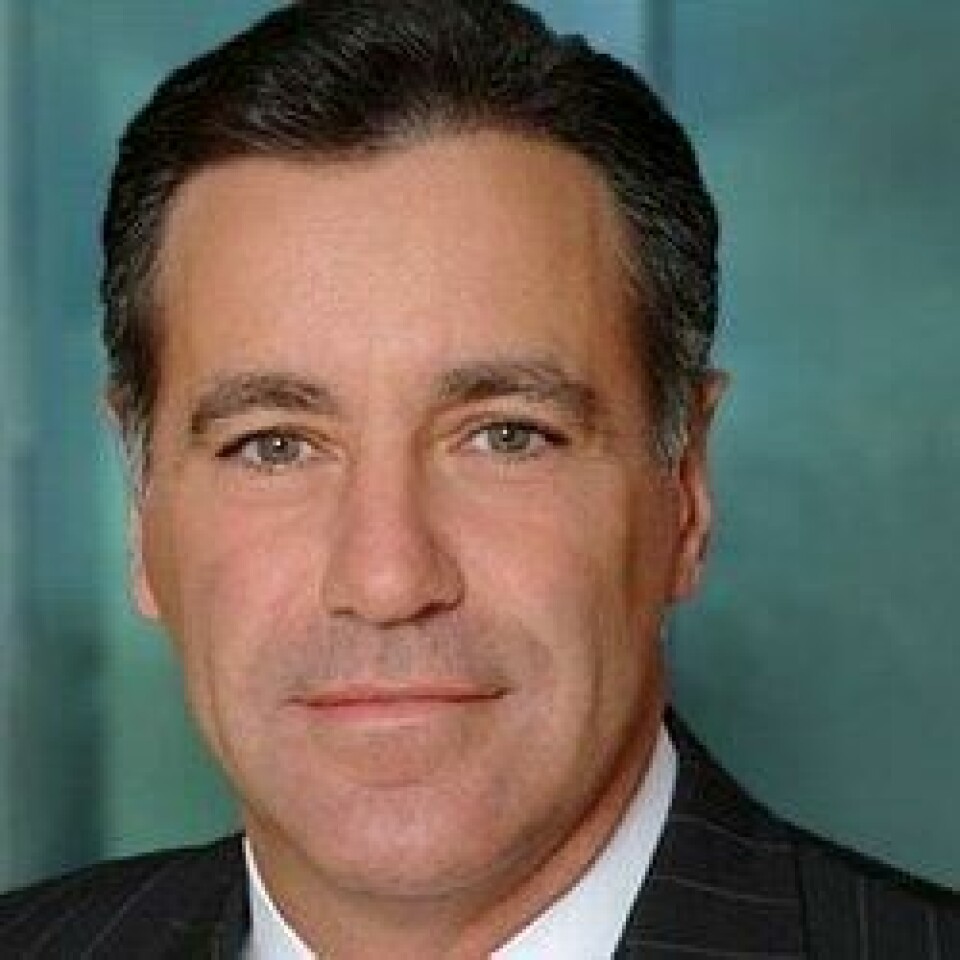
Bullard added: “We were learning about the virus and transmission protocols a bit more on the fly than previous crisis events. That represented to me the most unusual part of this one. We quickly developed protocols and implemented temperature screening, as well as certain standards that allowed us to control the environment; it was a learning curve though.”
Black added that the fast adoption and implementation of those protocols was thanks to having quality people in place who understood the requirements of the job as their work environments quickly changed.
“The way our team members were able to embrace the work-from-home rotating schedules and how all this impacted their personal as well as their professional lives has been phenomenal,” said Black. “The dedicated professionals we have in our organisation have really stepped forward.”
New deal for trade
Asked about how the signing of the US-Mexico-Canada trade agreement is likely to test Penske going forward Bullard said he didn’t foresee any major issues.
“Truth be told, back when it was unclear whether the agreements would be signed there were potentially further delays at borders but from what I have seen the borders are flowing and there is no abnormal complexity,” he said. “It is business as usual and I don’t expect that to change.”
That said, business as usual in Mexico is not without its supply chain issues at the best of times and Bullard said that the availability of material out of Mexico accounts for 75% of the issues that Penske’s customers are currently dealing with.
“Relatively speaking it is the number one issue we have today on availability of supply to keep the manufacturing locations working but it is a play we have run before and we know how to deal with part constraints and expedited shipments,” he said.
At the end of the day Bullard said business was going well despite the disruption caused by the coronavirus and the reorganisation of trade in North America because logistics was an industry used to managing crisis events and maintaining just-in-time material flow strategies.
“That makes us uniquely capable of reacting to unknown events – we are all pretty used to doing it and this is just another one on top of it,” said Bullard.