Typhoon Kong-rey’s disruption on automotive logistics highlights the need for predictive tools
Typhoon Kong-rey made landfall in Taiwan at the end of October before impacting the Philippines, East China, South Korea and Japan, disrupting ports in the region.
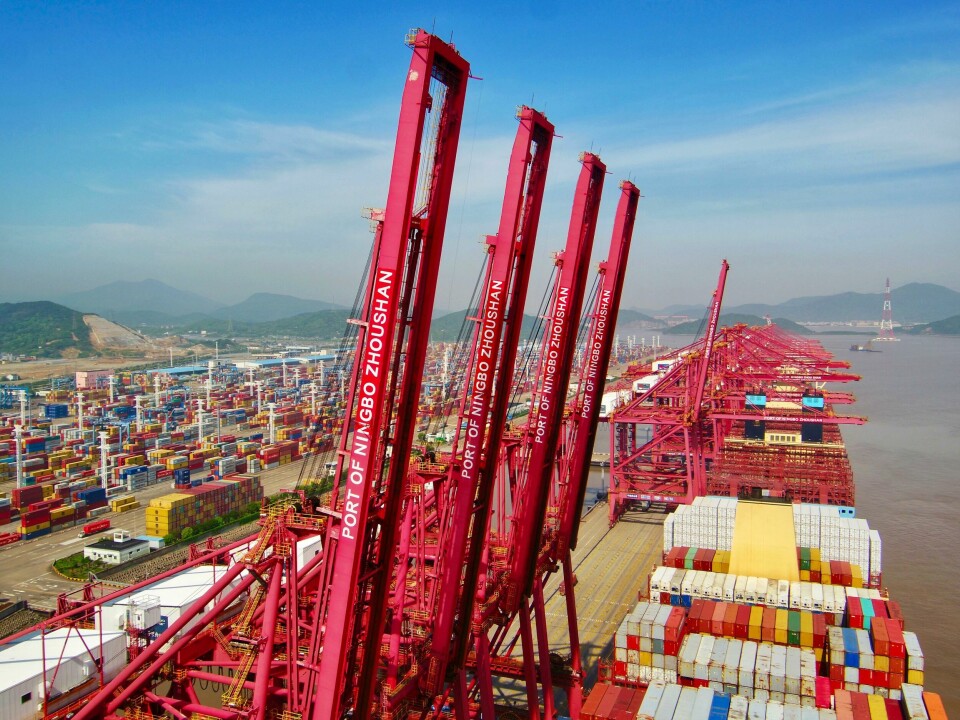
As of 17 November, the Ningbo port has 123 container ships at anchorage, stuck in a backlog due to the Typhoon Kong-rey
Container shipping ports in the East China Sea have been facing congestion due to the impact of Typhoon Kong-rey, which made landfall in Taiwan at the end of October before impacting the Philippines, East China, South Korea and Japan.
Since the typhoon, which formed on 24 October and dissipated 7 November, the Shanghai, Ningbo and Kaohsiung container ports have been dealing with backlogs and congestion.
As of this week (17 November), the fallout from the extreme weather event continued to affect the ports and supply chains. At Shanghai/Ningbo port, there are almost double the amount of ships waiting to get into the port than there are docked, with 123 ships at anchorage and 65 at port, according to containership database Linerlytica. This equates to 537,336 TEU at anchorage, and 456,698 TEU at port, with a queue to berth ratio of 1.89.
The congestion following the typhoon reiterates the need to be flexible in the automotive supply chain and have visibility across the entire value chain, while using digital tools to improve predictability.
Jon Davis, chief meteorologist at Everstream Analytics, told Automotive Logistics that companies with supply chain exposure to extreme weather events need a plan to mitigate risk. “For example, prior to a storm impacting a facility or port, many companies accelerate or delay shipments, so they are not stuck in harm’s way,” Davis said. ”Both predictive and prescriptive pathways can be taken to reduce this risk.”
Davis added: ”These types of risk, typhoons in the west Pacific for example, are increasing due to climate factors such as the record ocean temperatures that are currently in place - more “fuel” from the warm oceans equates to more severe impacts. Climate risk scores in Taiwan and China indicate that the risk of tropical cyclones will be increasing during the upcoming decades.”
Even though the extreme weather event passed relatively quickly, the impact of delays – be they from natural disasters or strike action – can be long lasting in automotive logistics.
Following Typhoon Kong-rey, the port of Kaohsiung, Taiwan’s largest port, was closed for numerous days. Widespread power outages slowed the port opening due to availability of workers and infrastructure issues. The majority of other ports across the Nation were also closed for numerous days, and further west in China, the ports of Shanghai, and Ningbo, two of the largest container ports in the world, temporarily halted operations as a weakened version of Kong-rey moved across this area. The sheer number of major ports that were impacted compounded the issue and increased the severity of disruptions in, and around, the Taiwan Strait and the East China Sea. Since this area has such a large concentration of supply chain nodes, the ramifications of these disruptions reverberated around many areas of the globe, according to Everstream Analytics.
We’ve also seen similar supply chain disruptions earlier this year with lasting impacts reverberating across the supply chain.
When the Francis Scott Key Bridge at Baltimore port, Maryland, collapsed into the Patapsco River on 26 March after being struck by a cargo ship, it took three months for the port to be fully restored. The accident caused huge problems with the automotive supply chain in North America, and FVL firms had to re-route vessels to other US ports, including Brunswick, New York, Norfolk and Philadelphia.
Back in October, when the strike on the US east coast and Gulf coast ports was upcoming, Everstream Analytics estimated that one day of strikes would mean it would take seven days to clear the backlog, while three days of strikes would take anywhere between 21 and 25 days.
Similarly, Jessica Hanson, vice-president of Logistics at Bosch North America said at ALSC Global 2024: “The average standard right now is that it takes us, in the industry, at least one week per day of strike to try to recover.”
Agnieszka Kubiak, senior vice-president logistics at tier one mechantronics supplier Brose Group recently told Automotive Logistics that digital tools are helping the supplier to better predict and adapt to geopolitical disruptions in the supply chain. “Currently, I believe the best approach is to implement proactive risk management strategies, develop scenarios and create contingency plans to mitigate potential impacts,” Kubiak said.