Audi’s supply chain in 2033 and beyond: Designed to combine logistics, automation and people
Dieter Braun and his team know exactly where they want Audi’s supply chain to be over the next decade, even if technology and conditions will vary by plant and region.
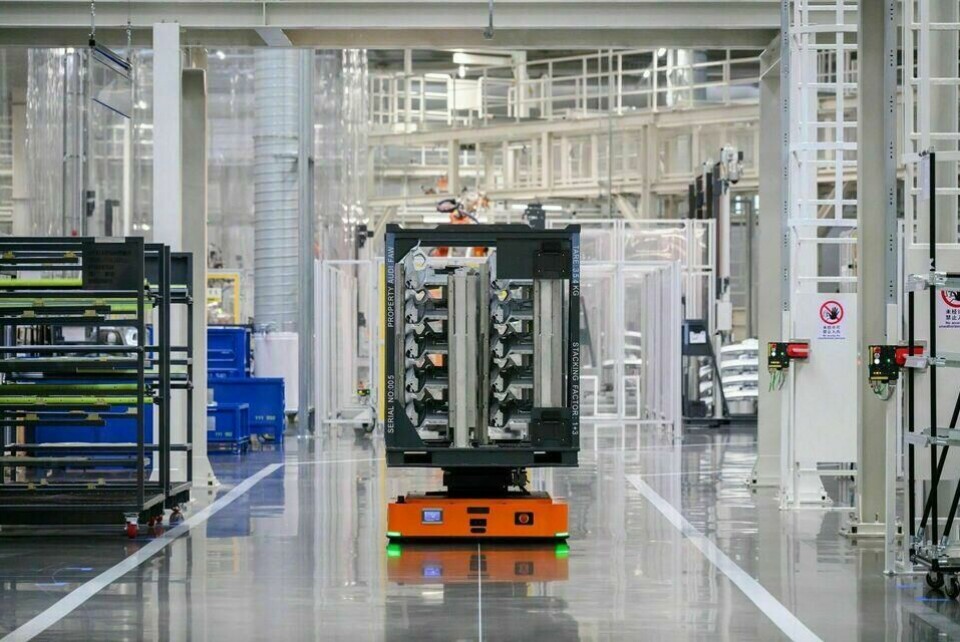
Audi envisions a greater uptake in logistics automation across its global plants and operations, however the application and timing of specific tools will vary by region and local circumstances
Audi supply chain series: Adding value through logistics
-
Dieter Braun on how Audi is turning supply chain motion into progress
-
Infographic: A snapshot of Audi’s production network and supply chain
-
Audi’s supply chain organisation: Logistics and the 360factory strategy
-
Audi’s supply chain in 2033 and beyond: Designed to combine logistics, automation and people
-
Breaking new ground: How Helrom’s Block Train is transforming Audi’s supply chain network
-
Red Sofa interview | Audi and Helrom discuss scaling sustainable rail logistics at ALSC Europe
Audi’s supply chain organisation is rooted in its end-to-end perspective, with ownership across the order-to-delivery cycle. But how should the structure and objectives of the supply chain function change and develop in the coming years, especially amidst such rapid market, regulatory and technological change?
That is exactly what the carmaker’s head of supply chain Dieter Braun and his team recently set out to answer. Starting with the framework of Audi’s 360factory strategy, they developed a vision of what the supply chain should achieve by 2033 and beyond, and then worked both with internal stakeholders and external experts to challenge these ideas and choose topics with the most potential. From this work, the team developed a detailed picture of how this target supply chain should look across each of Audi’s key logistics areas, including order-to-deliver (OtD), pre-series, inbound, inhouse , outbound and knockdown kit (xKD) logistics.
The overarching objective is to make Audi’s supply chain more resilient, competitive and sustainable. These include broad-based goals such as implementing more sustainable and efficient logistics, sourcing components closer to plants, increasing digitalisation and managing product complexity. They also include more specific goals, such as using more recyclable packaging, increasing ‘pearl chain’ sequenced flows, and implementing more integrated storage-and-material-flow automation.
With this picture, Audi’s supply chain team knows where it is heading, even though each objective needs specific considerations and often different timelines for implementation. For example, Audi cannot apply automation equally to all plants and locations thanks to variations in plant layouts, market conditions and costs.
Likewise, Audi has sought a balance between ambitious and realistic expectations, including for costs and technology. When it comes to managing vehicle complexity and reducing unnecessary part numbers, for example, the supply chain team has set high targets, with expectations that upcoming model programmes will significantly reduce parts sequencing requirements.
Braun and the supply chain team have also set out to explore how generative artificial intelligence (genAI) can help in making such decisions, with expectations that it will be able to process complex data sets across the order-to-delivery cycle in parallel, offering transformative opportunities.
However, the carmaker is more moderate in its expectations for other technologies. For sustainable transport, Audi assumes that progress in the next years will come mostly by shifting freight to rail and intermodal transport, as well as using more alternative fuels for trucks. Whilst the carmaker has pilots with electric trucks starting in 2025 and will roll out more together with Volkswagen Group Logistics in the coming years, it does not expect a high penetration of e-trucks until the early 2030s, when technology, costs and infrastructure improve.
Likewise, Braun’s team initially set higher ambitious to integrate autonomous logistics, including autonomous trucks. But external experts and consultants raised doubts over how fast such technology would be available, especially on public roads and motorways. Instead, Audi will put more focus on AGVs and using autonomous transport in controlled areas in the plant and yards.
“Our strategy is to implement consistent progress, and we will focus more on what we can achieve,” says Braun.
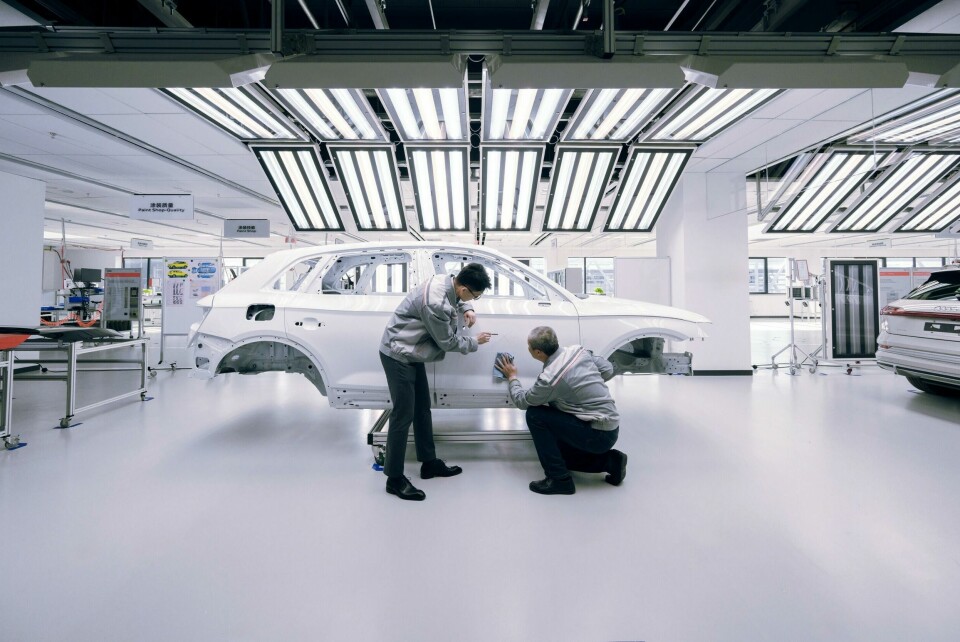
The Audi FAW NEV company’s new plant in Changchun has used a high level of digital modelling to plan logistics, has an integrated IT architecture, strong logistics automation and supplier localisation
Automating at China speed
Audi will use its global network, along with learnings across the Volkswagen Group, to help determine the best use of technology and processes, and how it might be applied to different regions.
One important example is the Audi FAW NEV Co. plant in China, which started production late 2024, and most resembles the carmaker’s target picture. It is a greenfield operation dedicated to building a new generation of electric vehicles based on the Audi-Porsche developed PPE platform, which has given the plant certain product, layout and technology advantages compared to brownfield locations.
“As we started from scratch, we had the chance to create opportunities close to an ideal state. In a great spirit of teamwork, local planners have worked with our supply chain experts from other plants to define and implement ideal processes,” says Braun.
The production and logistics planner at Audi FAW NEV Company – a cooperation company in which Audi owns a 55% share, FAW 40% and Volkswagen Group China 5% – used digital models to design production and logistics flows. The plant also has a SAP S/4 Hana IT architecture to seamlessly share production, finance and logistics data. There is less sequencing and fewer parts supermarkets on the shopfloor, with high levels of material automation and driverless transport. A 24-metre-high warehouse serves production with a fully automated storage and retrieval system, for example.
Meanwhile, the NEV plant leverages a strong supply base in the Changchun region in north-east China, and a local supplier park, representing around 85% of the material transport volume sourced within 30km of the new plant.
Audi cannot transfer these conditions so easily to other plants and regions. For example, logistics automation costs in China are low and highly scalable compared to elsewhere, points out Braun. There are many Chinese AGV suppliers that produce equipment at high volume with simple, standard designs. In Germany, by contrast, AGV equipment is usually more customised to specific solutions, and must adhere to different regulations – a scenario unlikely to change significantly or quickly.
Even though labour costs in China are lower, the cost of automating such logistics flows is often cheaper than in Europe or North America.
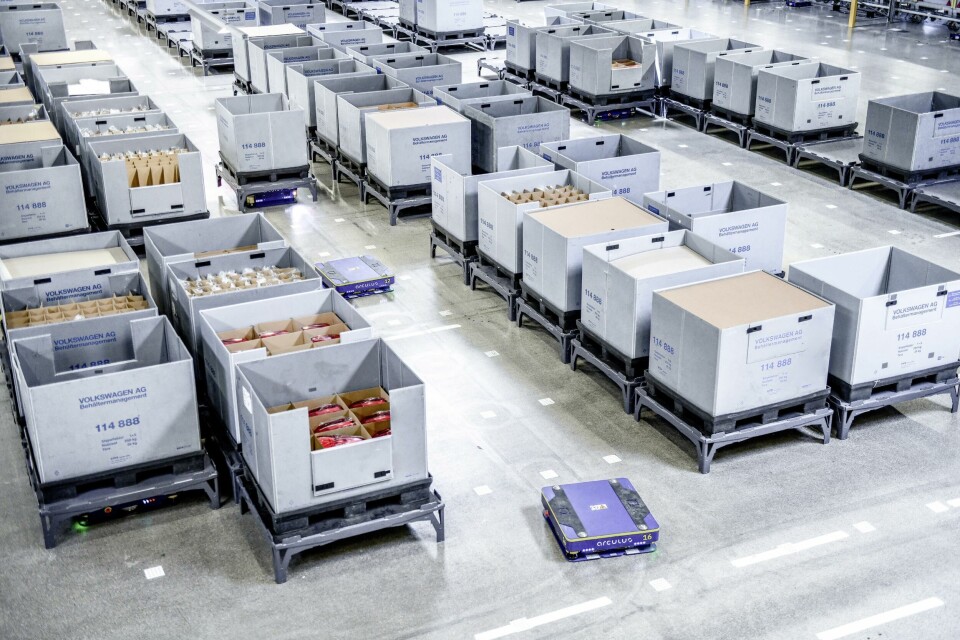
Audi continues to explore logistics technology and automation in plant logistics and parts supermarkets, but in many cases the highest automation comes where part supermarket numbers and complexity have been reduced
A chance to ‘clean up’ future logistics
However, whilst replicating conditions in China is not possible, Dieter Braun sees lessons that can be shared more widely from the Chinese plant in terms of how to transfer high levels of automated material flow. Here, a focus on the total process view and influencing decisions early will help other Audi plants to achieve similar benefits.
“What we can bring back from China is that from the very beginning we defined the ideal material flow and ideal condition on the line side,” says Braun. “If you compared this to our traditional plants you will find more complexity in the automation solutions, which is the enemy of scalable automation,” says Braun.
“It means that the task for our existing plants is to clean up the situation as much as we can, so that we can also achieve this ideal process.”
“The biggest step forward that we can take is to reduce complexity so that we don’t have so many parts supermarkets. If we don’t have the supermarkets, we don’t need robots for them.”
Dieter Braun, Audi
Braun has a similar perspective for advanced automation such as multipurpose robotics and humanoids. In China, Audi FAW NEV will work with the Beijing Innovation Centre of Humanoid Robotics, together with Chinese robot producer Ubtech Robotics, to explore this technology – joining other OEMs who are also trialling humanoids in their operations.
Braun is convinced that humanoids will play a greater role in logistics automation, and Audi’s centres of excellence are also exploring these possibilities outside China, too – but the technology is not ready yet. The size and shape of certain automotive parts will make them difficult to handle, and variation across parts still presents challenges. Over the coming years, at least, the best way for Audi to achieve its goals of greater material and logistics automation will be to remove the need for parts sequencing wherever possible.
“The biggest step forward that we can take is to reduce complexity so that we don’t have so many parts supermarkets,” he says. “If we don’t have the supermarkets, we don’t need robots for them.”
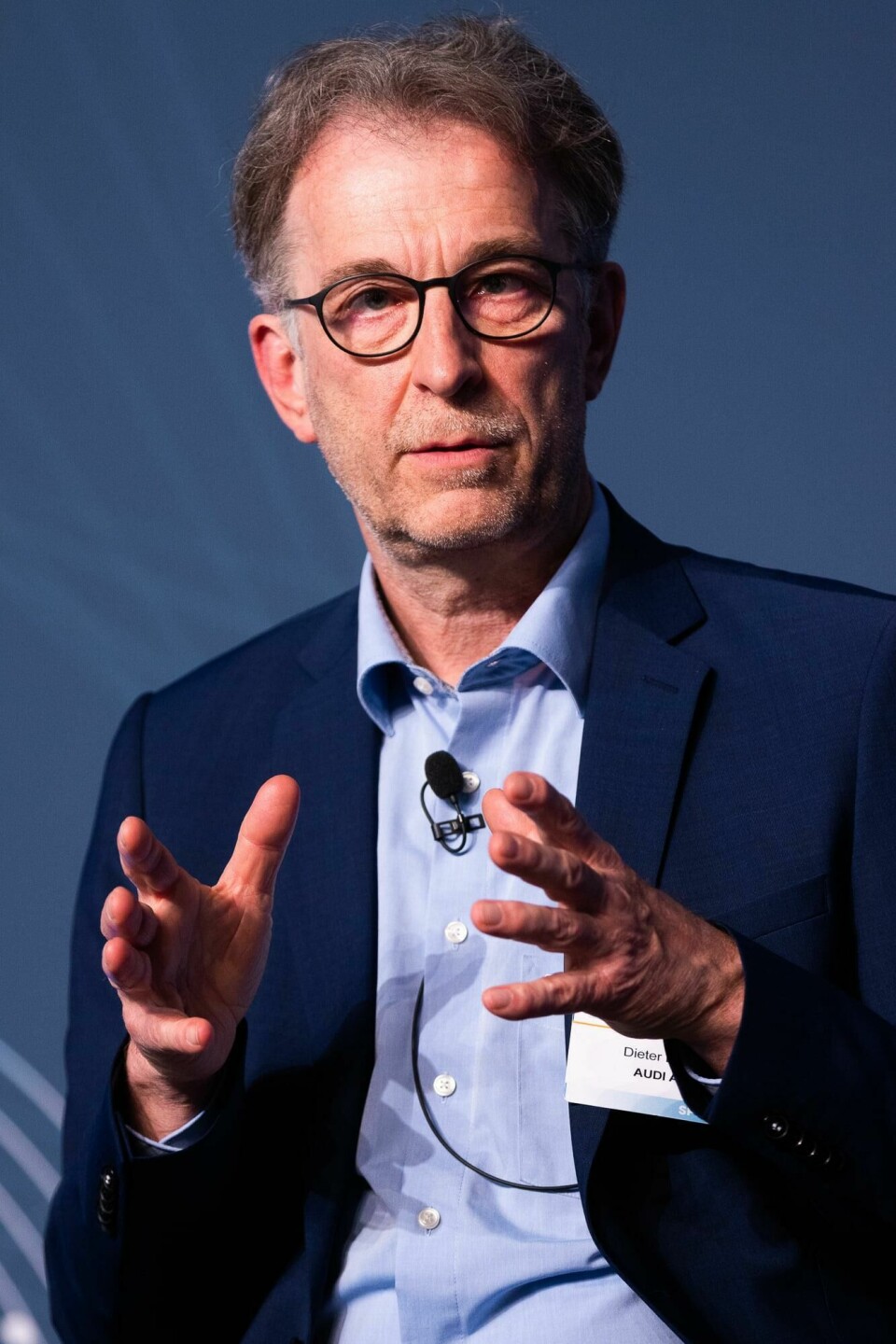
Whilst digitalisation, AI and automation are important features of Audi’s supply chain target vision, Dieter Braun considers them as a means to achieve objectives in resiliency, sustainability and competitiveness
A supply chain north star
Achieving Audi’s supply chain goals for 2033 and beyond won’t always come in a straight line or equal measure, especially considering regional and market differences. However, core principles and objectives won’t change for Audi’s supply chain, says Braun, including common process and innovation standards that developed in cross-plants teams, as well as increasing resilience, sustainability and competitiveness. Audi will thus continue to develop its organisation and its people in line with maintaining an integrated perspective across functions, especially for the order-to-delivery process, says Braun.
And while advances and emerging technology might introduce yet more tools, Audi will focus on those that help it to achieve its goals. “We won’t implement digital systems and AI just for the sake of technology, but always with the aim to improve visibility and control over the supply chain,” says Braun.
With competition and cost pressure only likely to increase, it will be become even more vital for logistics and supply chain experts to create value across the company, and to ensure that every order, call off, material handling, dispatch and motion represents progress.