Peter Koltai highlights the power of predictive analytics and holistic logistics in shaping a resilient EV production network
As VW Group expands its North American footprint, Peter Koltai, head of production control and logistics at Volkswagen de Mexico, tells Automotive Logistics how predictive analytics and AI are reshaping the company’s logistics to meet the challenges of electric vehicle (EV) production and sustainability.
Volkswagen Group is expanding its manufacturing footprint across North America, including with EV production sites and battery plants. Along with that, the logistics landscape for its Mexican operations is undergoing significant transformation. With the rise of EVs, growing sustainability demands and the pressures of nearshoring, Peter Koltai, senior director for production control and logistics at Volkswagen de Mexico (VWdM), is navigating these changes and leading the use of predictive analytics, artificial intelligence (AI) and enhanced regional collaboration. These strategies are helping VWdM tackle supply chain challenges head-on, creating a more resilient and efficient logistics network that aligns with VW Group’s broader electrification goals.
Expanding the North American network
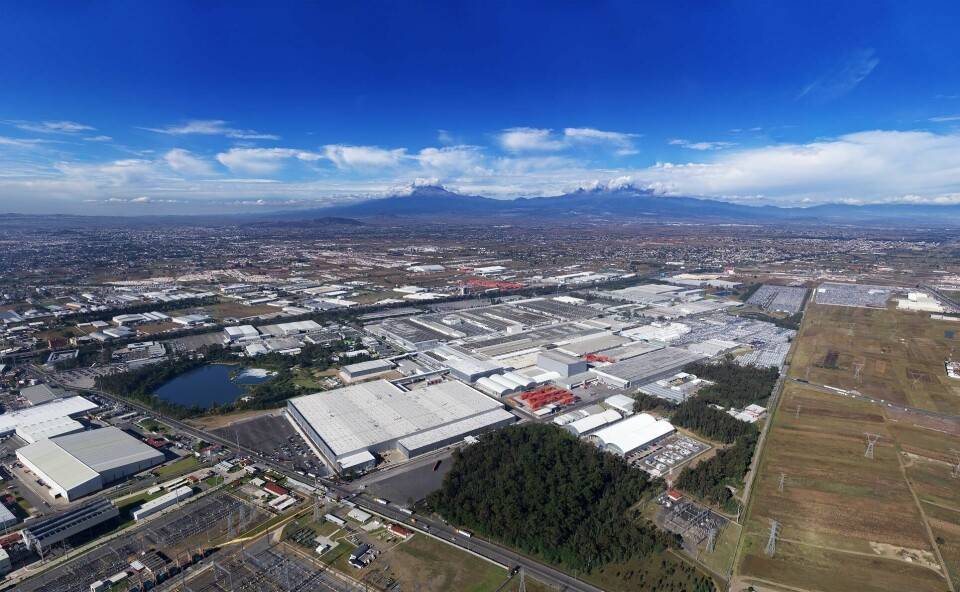
Volkswagen’s Puebla facility is at the heart of its North American expansion, evolving to support new EV production.
Volkswagen’s presence in North America has grown considerably over the last decade. Initially consisting of just a few sites, such as Puebla and Chattanooga, Volkswagen Group’s operations now span several locations, including new facilities for EVs and battery production. “If we look at the map today, what was once a few isolated plants has evolved into a vast network,” Koltai explains. This expansion includes commercial vehicle production sites and the development of new plants, such as Scout in Colombia and PowerCo’s battery cell facility in Canada.
This growing network has significantly impacted how VWdM approaches logistics, especially as the company prepares for future EV production. To meet these new challenges, VWdM has restructured its logistics organisation, merging its inbound and outbound logistics teams to create a unified approach. “By integrating these functions, we ensure that material and vehicle logistics are planned holistically, which is critical as we move into EV production,” Koltai says.
Digitalisation for supply chain resilience
VWdM is not only expanding its physical footprint but also transforming its logistical processes through digitalisation and predictive analytics. Koltai highlights that the nearshoring trend, which has increased industrial capacity in Mexico, brings challenges of bottlenecks and capacity shortages. In response, VWdM has adopted digital solutions for better transparency and quicker decision-making. “In this competitive environment, companies with the greatest transparency can respond more effectively,” Koltai notes.
VWdM has implemented predictive analytics to foresee potential supply chain disruptions. With more than 500 suppliers and 10,000-part numbers, managing the flow of materials is a complex task. “We’ve structured all the data we receive from suppliers into a database, allowing us to track deviations and predict disruptions before they occur,” Koltai explains. By identifying issues early, VWdM can mitigate risks that might otherwise lead to production delays.
One of the key areas where VWdM is advancing is in the use of AI to further automate predictive analytics. “We are working on a tool that will eventually predict daily disruptions and suggest the actions we need to take to maintain smooth operations,” says Koltai. This AI-powered system will allow VWdM to act proactively rather than reactively, ensuring that the company stays ahead of potential disruptions.
Supplier risk management
Managing the risks posed by suppliers is crucial. Koltai highlights that VWdM’s approach is heavily data-driven. “We collect data from suppliers daily, such as deviations in delivery times or quality issues,” he explains.
For example, if a transport service company faces significant delays in collecting materials, or if suppliers begin organising their own transport outside of VW’s logistics network, this signals potential problems. These insights enable VWdM to take pre-emptive measures. “We share and analyse these results daily with our purchasing and quality assurance teams to make informed decisions,” Koltai says. By turning this process into a digital workflow, VWdM can respond swiftly to day-to-day business challenges, further enhancing supply chain stability.
Collaboration across North America
VW Group’s efforts to strengthen its North American network extend beyond Mexico. Last year, VW introduced a joint control tower to oversee vehicle logistics across the continent. This initiative has already yielded improvements in cross-border flows and operational efficiency, particularly as Mexico faced significant capacity bottlenecks in 2023. “We recognised the need for closer cooperation between Mexico, the US and Canada,” says Koltai.
The control tower is one of three pillars in VW’s new logistics strategy, alongside integrated planning activities and 24/7 yard management at production sites and import distribution centres. This structure enables early warning systems for potential disruptions, allowing for more strategic, cost-effective planning. “By connecting operations across North America, we are becoming more resilient and efficient,” Koltai adds.
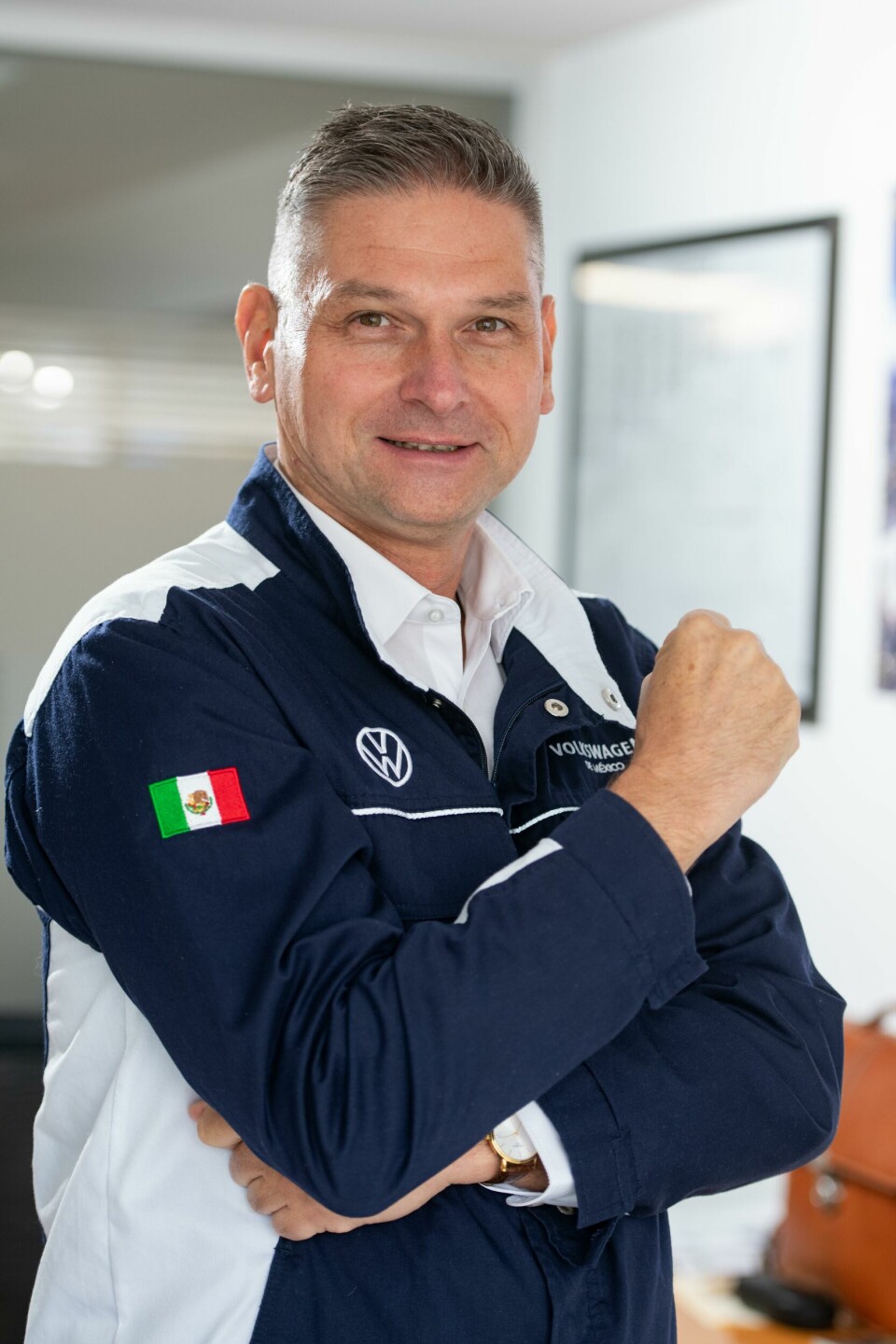
Emphasising the importance of collaboration and integration, Koltai states, “By merging inbound and outbound logistics, we ensure that material and vehicle logistics are planned holistically,” paving the way for resilient EV production in North America.
Port optimisation and customs improvements
Mexico’s ports, particularly Veracruz, play a vital role in VW’s logistics operations. While material container flows have remained relatively smooth, vehicle logistics faced significant delays last year because of infrastructural bottlenecks and changes in customs processes. However, thanks to efforts by port authorities, public yard spaces have been expanded, and key infrastructure challenges have been addressed. “We’ve also redirected part of our vehicle flow to the port of Tuxpan, which has been a critical move for operational flexibility and reliability,” Koltai explains.
This diversification of port operations has strengthened VWdM’s supply chain resilience. By having multiple ports available, the company can better manage unexpected capacity losses, a constant risk in the automotive logistics sector. “We are now in a stronger position to manage unforeseen disruptions,” Koltai notes.
Rail transport and labour shortages have posed significant challenges for Volkswagen Mexico, particularly in terms of finished vehicle logistics. To overcome these obstacles, the company has focused on securing long-term contracts with reliable partners and developing alternative solutions for unanticipated disruptions. “We do not want to experience the surprises of last year again,” Koltai asserts, emphasising the importance of preparedness and flexibility.
Volkswagen’s commitment to sustainability is also influencing its logistics strategies. “We are constantly looking for ways to reduce emissions, whether through alternative energy sources or improved packaging and transport planning,” Koltai says.
VWdM is investigating solar-powered facilities to support its logistics activities. “We have yards for finished vehicles where a solar roof could be a great option. The climate in Mexico is not a barrier for this solution,” Koltai explains. Sustainability remains central to VWdM’s logistics planning, particularly in ensuring that transport efficiency is maximised and unnecessary routes are eliminated. “The classical logistics target – avoiding the transport of air – always presents opportunities for improvement,” he adds.
Logistics for an electric future
Additionally, as Volkswagen Mexico prepares for the transition to EVs, its logistics organisation is also evolving. The company’s Strategy 2030 outlines the steps required to transform its inbound, in-house and outbound logistics processes for EV production. This strategy is being developed in close collaboration with VW’s North American network to ensure alignment with the company’s broader electrification goals.
“Preparing for EVs requires significant changes across all logistics functions,” Koltai says. “We are working closely with our sister plants in Europe and China to implement best practices and ensure a smooth transition.”
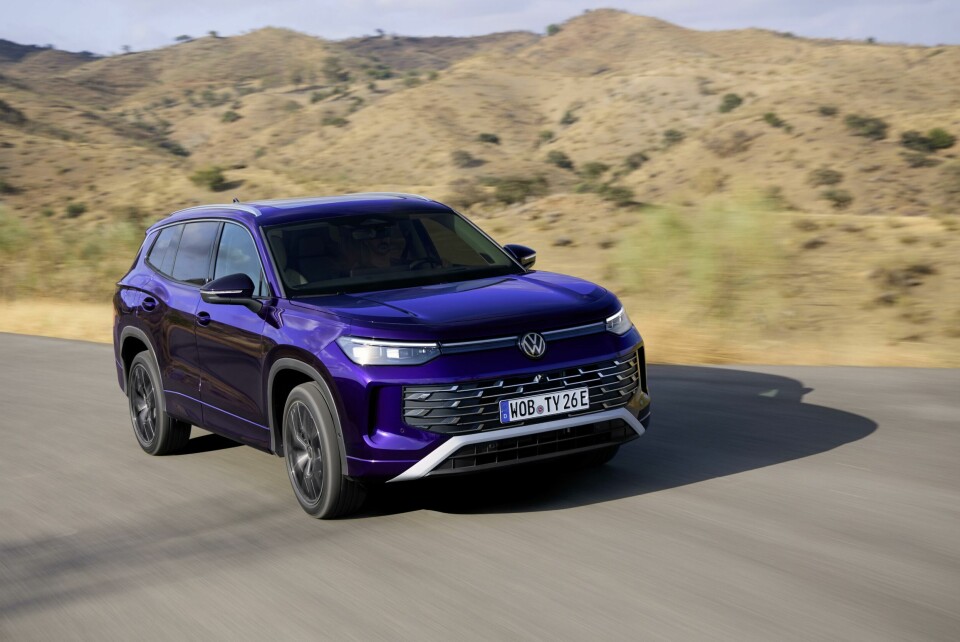
The new Tayron model, set to replace the Tiguan in Volkswagen de Mexico’s production lineup, represents a key focus in the company’s logistics strategy. As Koltai notes, ”Ensuring the smooth launch of the Tayron remains our top priority.”
Looking ahead to 2025, VW Mexico’s logistics strategy focuses on three key priorities: optimising operations, reducing costs and maintaining supply chain stability. A significant focus will be on the ramp-up of the new Tayron model, which will replace the outgoing Tiguan in VWdM’s production lineup. “Ensuring the smooth launch of the Tayron remains our top priority,” says Koltai.
Another critical objective is the continued development of AI-supported predictive tools to manage supply chain risks. “The goal is to have a system that not only predicts disruptions but also recommends solutions, allowing us to act proactively,” Koltai explains.
Finally, VWdM is committed to improving its inbound logistics processes for deliveries from North America. By streamlining these operations, the company aims to significantly reduce costs while maintaining high levels of efficiency and resilience.