Global ro-ro report: Moving with the trade winds
The ro-ro industry has mostly balanced capacity to market demand, but there are regional variations, while changing trades and larger vessels will cause waves at sea. Additional reporting by Christopher Ludwig
The global ro-ro shipping industry is one of the most complex – not to mention capital intensive – parts of the global finished vehicle logistics sector. Carriers must provide carmakers a high quality service at the right frequency and capacity levels. With ships very expensive to build as well as to run and maintain, getting this balance right is critical. One only has to look at the red ink that stains the container shipping industry to see the cost of getting it wrong.
The ro-ro sector, however, has not suffered much the same fate as container shipping. Much of the industry was hurt badly following the 2008-2009 downturn, which saw volumes fall off at a time when order books were full; however, in the past few years carriers have been reasonably successful in balancing global capacity in line with demand for vehicle imports and exports. Data from WWL’s Global Market Intelligence unit also reveals that carriers have been fairly restrained in maintaining their fleet sizes since 2011 given the volatility in the market during this period (especially out of Japan).
But while carriers are fairly healthy, and overall capacity levels are aligned to demand, it is a different story depending on region. Perhaps most noticeably, European outbound capacity has been tight, which is partly the result of fewer imports from Japan at the same time that exports from the continent remain strong. Meanwhile, a number of emerging production centres are increasing their output, including Mexico and Thailand, creating both opportunities to add new services, but also difficulty in terms of reallocating capacity or balancing trade flows in either direction. Many ocean carriers are fulfilling demand by adding or subtracting tonnage among different routes and introducing new vessels. Even so, the results do not always meet the demands of carmakers.
In this story...
- Tracking utilisation
- Changes from Japan
- Post-Panamax vessels
- Mexico and new trade lanes
- Shipping service for Honda
Data:
One of the reasons has been that the global ro-ro market has become more fragmented, with a higher number of smaller volume exporters than in the past. According to Ole Gustav Eriksen, shipping analyst at international ship and offshore brokering company RS Platou, export flows are increasing out of Thailand, along with large trade flows in and out of China, Indonesia and India, for example. Along with Mexico, US-built vehicles have also been seeing a growth in export volume. These changes in export sources are not only eroding the decades-old trunk lines out of Japan and South Korea, but they also support intra-regional flows, such as short-sea shipping in Southeast and East Asia as well as in North America between the US, Mexico and Latin America.
The development of these short-sea flows moves somewhat in contradiction to other trends in the sector. For example, the widening of the Panama Canal is leading more carriers to order ‘Post-Panamax’ vessels that will have capacity for around 8,000 car equivalent units (CEUs) compared to 6,500 CEU today. However, while such large vessels are more economical per unit, they are most effective on large trade flows that can use their maximum capacity. A splintering of demand, on the other hand, requires the use of more hub ports and smaller feeder vessels. For example, intra-Asia flows, according to Eriksen, typically call for shorter vessels than those used from Japan and South Korea. Carriers will need to think carefully about their network routing and capacity allocation as their fleets change and these new flows develop.
A further issue for the sector is clearly that of costs, and in particular the rising price of bunker fuel. One of the most significant changes that the sector will face is in 2015, when ‘emission control areas’ in Europe and North America will require that sulphur emissions do not exceed 0.1%. Many carriers have called for a delay in the rules, as they do not yet have the technology to meet these requirements, while the cost of low-sulphur fuel will be significantly higher than the fuel used today. Rudolf Luttmann, director of car and ro-ro at Mitsui Bulk Shipping OSK Europe (MOL), says the industry has yet to find a collective solution. “We are studying new scrubber systems, and types of fuel, such as LNG (liquefied natural gas), but this is not feasible for existing tonnage,” he says. “In this respect we need more time to avoid a huge cost increase in seagoing traffic.”
Keeping an eye on capacity utilisation
These rising costs have and will put even more pressure on carriers to operate a more balanced cargo network. Eriksen points out that car carrier trades were previously dominated by the major front hauls from Japan and South Korea to Europe and North America, with return voyages being considered largely as “ballast”. Such imbalance is now unsustainable for costs, and is a waste of capacity that could be used for growing cargo volume in other regions.
Balancing trade flows is also an important part of increasing carriers’ capacity utilisation rates, which is the main way that shipping lines remain profitable. While the utilisation rate has improved since the crisis six years ago, it is still lower than desired. RS Platou defines full utilisation in the global carrier fleet as about 90%. In 2012 and 2013, the broker calculates that the utilisation rate was 87% and 86%, respectively, meaning that overcapacity has increased from 3% to 4%.
Eriksen does not expect overcapacity to increase in the next 2-3 years, however. “We expect the market balance in 2014-2015 to improve marginally on the basis of demand growth in the 4-5% range annually, and a slightly lower supply growth in the same period,” predicts Eriksen. [sam_ad id=6 codes='true']
Steinar Lovdal, head of capacity management at global deep-sea carrier Höegh Autoliners, says that he has generally seen a positive trend in utilisation figures over the last three years, although utilisation is down slightly this year compared to 2012, primarily because of the still-weak European market. For Höegh, at least, utilisation had increased between 2010 and 2012.
There are notable gaps in ro-ro capacity, with Europe one of the biggest concerns because of its weak imports but strong exports. Lovdal points out that the situation is different in the US, however, with a surplus of open capacity and several operators ballasting vessels from the US to Europe.
MOL’s Luttmann says that the ongoing diversification of trade patterns is leading to a tight tonnage situation in certain areas for the shipping line. “For our outbound business from Europe, our tonnage is tight in the trans-Atlantic region and to the Far East. This is due to reduced flows from Japan to Europe and increased exports of German high-end cars to the US and China,” he says.
In response to the market’s volatility, deep-sea ocean carriers have been keeping a close monitor on their fleet capacity, with most (but not all) reducing capacity levels in 2013 (see data above). However, with the global market still growing 3-4% per year, there is still a need for more vessels. According to Lovdal, the order book for deliveries over the next 2-3 years stands at about 10% of fleet capacity.
Despite those expansion plans, however, carriers such as Höegh Autoliners, which has been among the carriers increasing its fleet size most aggressively, expect that the market will still remain relatively balanced as shipping lines recycle smaller and less efficient vessels built in the 1980s. “There is still room at the yards for additional new buildings should we see a stronger growth in volumes, but both operators and tonnage providers are left with a weaker capital base after the crisis in 2009, which has taken our industry longer to overcome than our customers,” says Lovdal.
“Although demand is a little slower than we might wish, it coincides with planned recycling of some of our older vessels, making the situation fairly balanced overall,” says Erik Nyheim, chief commercial officer of Wallenius Wilhelmsen Logistics (WWL).
WWL, which operates a fleet of about 60 vessels owned by Sweden’s Wallenius Lines and Norway’s Wilh. Wilhelmsen, also supplements its own vessel capacity with charter tonnage to adjust for demand troughs and peaks. Besides vessel recycling and charters, Nyheim points out operational measures that WWL may take to influence capacity that include managing vessel speed, reducing time at port, shifting fleet allocation between trades in different cycles and swapping vessels within the group.
Big shift in Japan
One of the factors affecting utilisation has also been weaker volume from Japan and, to a lesser extent, South Korea. Indeed, the shift out of Japan may well be more of a structural change than a short-term reaction. “Whereas we expect Korea to rebound to volumes similar to those in 2012, exports from Japan are likely to remain at lower volumes than seen historically,” predicts Eriksen.
Following years when Japan’s carmakers suffered from natural disasters, an historically high yen, and other supply chain issues (including longer order-to-delivery times) manufacturers have been making a more aggressive push to localise production in overseas markets, most notably in Mexico and the United States, as well as Southeast Asia.
Nissan, for example, has expanded capacity in the US and was slated to open up its third Mexican plant at the end of 2013, located close to another factory in Aguascalientes. Both Honda and Mazda will open factories in the first quarter of 2014. Toyota is also expanding capacity at its US and Canadian plants. Meanwhile, Japanese carmakers have expanded production in Thailand and Southeast Asia. Mitsubishi exported around 230,000 vehicles from Thailand in 2012, and more than 300,000 from Japan. Six years ago, its Japanese exports were twice as high (see p16 for more). The carmaker has plans to increase capacity in ASEAN over the next three years (read more here).
"Although demand is a little slower than we might wish, it coincides with planned recycling of some of our older vessels, making the situation fairly balanced overall – Erik Nyheim, WWL
The Japanese government has made policy moves to support exports, including a push for higher inflation that has substantially weakened the yen. While that is benefitting exporters’ profits, it has not yet led to much recovery in Japanese export volume, states Lovdal.
While South Korea is likely to remain a competitive export base, manufacturers here too have suffered as its currency strengthened. During 2013 there were also a number of labour disputes in 2013 that disrupted production at Hyundai, Kia and GM’s South Korean unit. While there is little doubt that the country remains the base for Hyundai and Kia, rising local production for the carmakers in China, Russia and other markets have also changed the export strategy somewhat. Hyundai, for example, is also now a major exporter from India.
Meanwhile, GM’s recent decision to end sales of most Chevrolet models in Europe by 2016, most of which are built in South Korea, will end the export of nearly 200,000 per year to the continent. While GM’s rationale for the move was largely an internal issue to focus more on its Opel/Vauxhall brand in Europe, it does nevertheless signal a move away from Korean exports.
In terms of other global export shifts, RS Platou predicts strong growth in volumes from India, Thailand, and Europe. “In the short term, a recovery in European car sales would influence car carrier demand positively. However, in the long term, growth would need to be supported by demand in emerging economies such as the BRIC countries and Africa,” says Eriksen.
Bring on the big boys
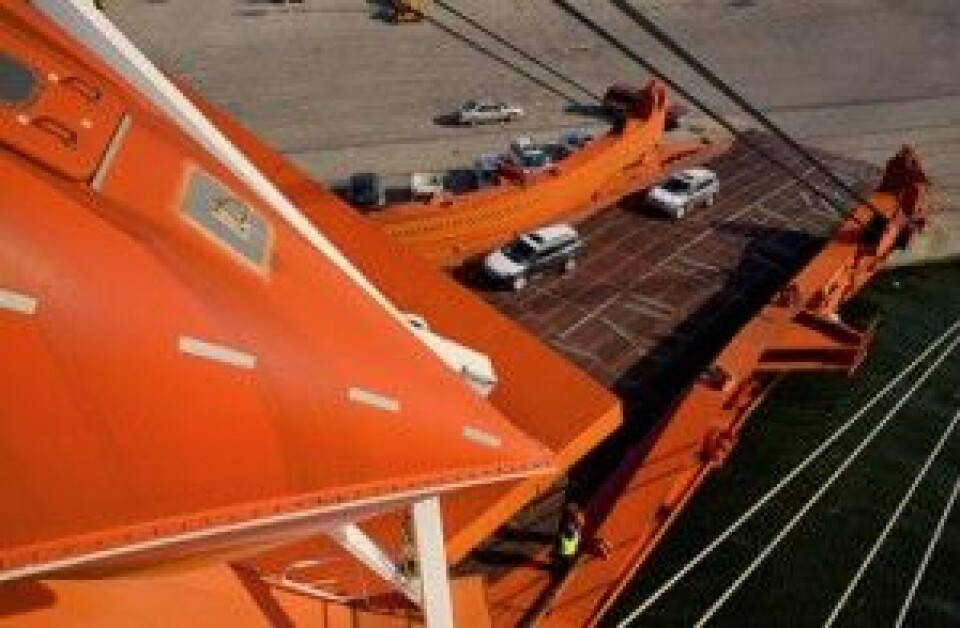
The Panama Canal expansion project will double the canal’s capacity by 2015 by adding a new lane of traffic and by accommodating larger ships. It should also reduce transit times. Eriksen says that ocean carriers have ordered post-Panamax vessels that offer higher cargo capacity within a vessel length of 200 metres, which is the limit in a number of Japanese ports. The average size for these new vessels is 8,200 CEUs, he says.
A spokesperson for Eukor Car Carriers, which is the base carrier for Hyundai and Kia around the world, says that the new wide-beam post-Panamax vessels that are due for delivery during 2014 will enable the shipping line to lower its cost base and emissions as the ships carry a greater cargo intake per vessel.
Although Lovdal says that the widening of the canal has allowed the industry to invest in ships with larger lifting capacity that do not increase vessel length beyond what many of the ports it calls can handle, limits in some locations could lower the vessels’ efficiency. “The wider beams on the post-Panamax vessels create challenges in some ports with locks, but we expect that this will be solved as the fleet of wide-beam vessels grow,” he says.
Lovdal says that for deep sea, the standard vessel size for Höegh has been about 6,500 CEUs, which is now increasing to about 7,500 with the introduction of the post-Panamax vessels. He notes, however, that carriers are still ordering 6,500 capacity vessels.
Eukor is among the carriers that have bought larger ships. According to the spokesperson, the company took delivery of five new vessels in 2013, and will add four more within the next year, including three post-Panamax vessels.
WWL has six post-Panamax vessels scheduled for delivery beginning in 2014 and another two on option. These vessels will have a capacity of about 8,000 CEUs, according to Nyheim. He emphasises that size is only one piece of having an effective export logistics chain, however. “Our real gains in optimising efficiency come when we take an integrated factory to dealer view of the outbound supply chain and ensure that the distribution system is optimised for time, cost, quality and emissions,” he says.
Luttmann says that MOL is not anticipating much increase in global capacity during the next three years, and its new buildings on order are limited. Two vessels will come online in early 2014, he says. According to data from a number of sources, the shipping line currently has the least amount of capacity on order among the major carriers (see table to the right).
He adds, however, that the shipping line could take advantage of relatively short vessel delivery times. “If we contract new buildings now, we would receive the vessel in about a year, instead of two years, for example, because there is not as much going on,” he says.
Luttmann says that customers seem to prefer higher frequency and smaller shipments. Reliable schedules, punctuality, and flexibility are necessary. MOL’s standard size vessel is 6,400 RT (a ro-ro shipping measure equivalent in size to a 1966 Toyota). When looking at new design, the focus is more on flexible utilisation, energy and fuel efficiency, particularly with the looming sulphur regulations.
“Our Emerald Ace, introduced in late 2012, is the world’s first hybrid car carrier. The ship is equipped with lithium-ion batteries that are charged by solar generator system while at sea. When at berth the Emerald Ace uses this power and can switch off the engine,” states Luttmann.
There is clearly a growing market for short-sea shipping from Mexico to the US where we are about to increase our frequency from three to five sailings per month – Steinar Lovdal, Höegh Autoliners
For short-sea shipping, a variety of vessel sizes are used, but there is also a trend towards larger vessels. In Europe, the largest vessels used are around 4,500 CEUs, and move mainly in and out of the Mediterranean. One reason for this increase in size is that deep-sea operators are moving more of these sized vessels out of deep-sea loops, where they are no longer as profitable.
New sailings for Mexico
Among the production regions that the latest vessels will likely serve is Mexico, which is expected to become one of the fastest growing regions for vehicle production globally. Along with new plants in the country by Audi, Honda, Nissan and Mazda, there are reports that Toyota and other carmakers will also eventually add production capacity there. With the increasing volume out of Mexico, MOL plans to expand its current services, according to Luttmann. Earlier this year, America Honda revealed that it would be using MOL services from both Veracruz and Lázaro Cárdenas to move vehicles to the US east and west coasts.
To meet the growing demand for ocean transport in the region, WWL has already expanded its services in Mexico by increasing sailings from Veracruz from two per month to three per month. Nyheim says that forecast accuracy is always a big challenge for the shipping line in planning new services in the region.
But Mexico presents other difficulties for shipping lines as well. Höegh’s Lovdal points out that although a large share of the fast increasing production is for export, most of it moves to the US and Latin America, which means limited volumes for deep-sea ocean transport, and more for short-sea distances – or indeed, rail transport. “There is clearly a growing market for short-sea shipping from Mexico to the US where we are about to increase our frequency from three to five sailings per month,” he says.
Others points to the difficulty of making money on such services, particularly in the face of strong competition from rail, which is the dominant transport mode for moving vehicles from Mexico to the US. “The challenge is to generate sufficient income to bring enough tonnage to the region,” points out MOL’s Luttmann. “We are also competing with other transport modes such as rail between Mexico and the United States.”
Given rail’s speed and relatively lower costs, it has historically been hard for shipping lines to offer more frequent service between the US and Mexico. Indeed, to save costs, most shipping lines include Mexico-US calls as part of larger shipping routes between North America and Europe or Asia, rather than using shuttle services between the countries.
Mexico is only one of the growing production centres that require greater ocean capacity, with Southeast Asia also seeing significant growth. Balancing flows is an important aspect of any cost effective service, and it is something with which the shipping industry continues to struggle. “The supply and demand situation in the new trades is not always balanced and still leaves some empty space on certain legs. It is a challenge to cover the costs for the entire voyage or for the repositioning of vessels,” says Luttmann.
Luttmann says that MOL expects that vehicle exports from Japan will remain steady or perhaps decline slightly in 2014 compared to 2013.
“This enables us to focus more on cross trades and exports from other Asian countries,” he adds.
Short-sea transport in Asia is the fastest growing part of Höegh Autoliners’ market, according to Lovdal. “We are investing in the area through the establishment of our joint venture company Sinor Lines, which has already started a service between Japan, Thailand and Myanmar,” he says.
As new markets grow and vehicle demand shifts, ocean carriers will change routes and services by necessity. The diversification of flows from the major trade lanes between Japan and South Korea and the US and Europe has recently accelerated such redesigns. While overall volume is up, it is spread over more markets and trade lanes, which makes allocating capacity even more difficult.
On the other hand, the rise of new production centres, such as Southeast Asia and Mexico, as well as growing demand across the world, could allow shipping lines to capture more return freight between some regions. Likewise, inter-regional trade, such as short-sea shipping in Asia and North America, is also driving more demand for shipping, and again requiring more creative service offerings.
While deep-sea carriers must be careful when determining their capacity investments and in deciding where to shift existing assets – especially since the vessels cannot, as the old saying goes, turn on a dime – the global ro-ro shipping sector looks set to grow in volume and in the dynamism of its services in line with global production trends.

In Europe, Honda handles finished vehicle imports from Japan and China, as well as exports from its plant in Swindon in the UK to Europe and a few other global destinations, including Australia.
Imports are higher in volume compared to exports. Honda management in China and Japan are responsible for European imports up to the arrival port, at which point Honda Europe takes over. For the UK, Honda uses the ports of Bristol, in the west of England, and Ghent, Belgium for Europe. Deep-sea vessels call three or four times per month. For imports bound for the continent, vessels call the port of Zeebrugge and are then barged or trucked to Ghent. Stacy adds that deep-sea calling frequencies are good thanks in part to Honda’s centralised port system, which was completed in March 2013.
Stacy says that for short-sea shipments the sailing frequency and sailing times could be improved. The problem is not one of capacity, however. “We need increased frequency – not necessarily more volume or dedicated capacity,” he says. “The problem with the current system is also that shipments are too close together.”
He points to some improvements, including an increase in service to one of its short-sea ports, Santander, Spain, from one weekly sailing to two.
Honda ships most of its exports from Swindon through the port of Southampton on England’s southern coast. Here, Stacy points to port capacity issues as a number of carmakers use the port for imports and exports. Stacy believes that this issue could be alleviated if vessel frequency were to improve.
“On the deep sea side, our export capacity requirements are met most of the time; we ship every ten days to Australia, which is okay,” he says, as the volumes are not very large.
Stacy says that cargo capacity is not as much of an issue for deep-sea shipping as is the accuracy of timing and reliability. Honda has monitored accuracy rates for its deep-sea movements to be between 75% and 80%.
The accuracy rate for short-sea shipping is better, according to Stacy, and on the whole he sees improvements for European short-sea shipping, including service levels as well as on-time rates.
For its own operations, Honda is trying to improve its forecasting accuracy. “This can impact delivery. We need not only better visibility, but also better planning,” he says.
Stacy says that Honda is not anticipating a sharp recovery in Europe, but rather a return to stable or flat growth, which he believes would be preferable for the logistics network. “We would prefer steady growth rather than volatile or subsidised growth,” he says.