Audi’s supply chain organisation: Logistics and the 360factory strategy
Under Dieter Braun, Audi’s Supply Chain function is highly integrated with objectives closely aligned to the carmaker’s 360factory strategy, including for sustainability, cost control and flexibility.
Audi supply chain series: Adding value through logistics
-
Dieter Braun on how Audi is turning supply chain motion into progress
-
Infographic: A snapshot of Audi’s production network and supply chain
-
Audi’s supply chain organisation: Logistics and the 360factory strategy
-
Audi’s supply chain in 2033 and beyond: Designed to combine logistics, automation and people
-
Breaking new ground: How Helrom’s Block Train is transforming Audi’s supply chain network
-
Red Sofa interview | Audi and Helrom discuss scaling sustainable rail logistics at ALSC Europe
At the heart of Audi’s Supply Chain organisation and strategy is an emphasis on visibility of end-to-end processes and how they link together, tracing customer orders back through suppliers, logistics and production. It includes all transport and inventory costs, managing plant production programmes, material planning and handling and delivering vehicles to customers.
At Audi, supply chain and logistics steer this process, called ‘order-to-delivery’, and helps to articulate the total impact – including direct costs, working capital and profits. It is a responsibility that interacts across Audi’s logistics, as well as its wider collaboration with Volkswagen Group Logistics (Volkswagen Konzernlogistik). It is one of the most important pillars for logistics of Audi’s wider production strategy, the 360factory and underpins objectives that Head of Supply Chain Dieter Braun and his team have set to create a more resilient, competitive and sustainable supply chain.
Understanding Audi’s Supply Chain and Logistics functions
Audi’s supply chain and logistics department includes around 4,700 employees working across six central functions, as well as five logistics functions lead at the plants (more than 3,000 work in plant-related logistics roles).
Central teams at Audi include Supply Chain Steering, which manages programme planning and scheduling of vehicle production volume and sequences for plants, in a combined role with vehicle distribution. The steering team also includes supply and capacity bottleneck control – a role that has been especially important during material and capacity shortages.
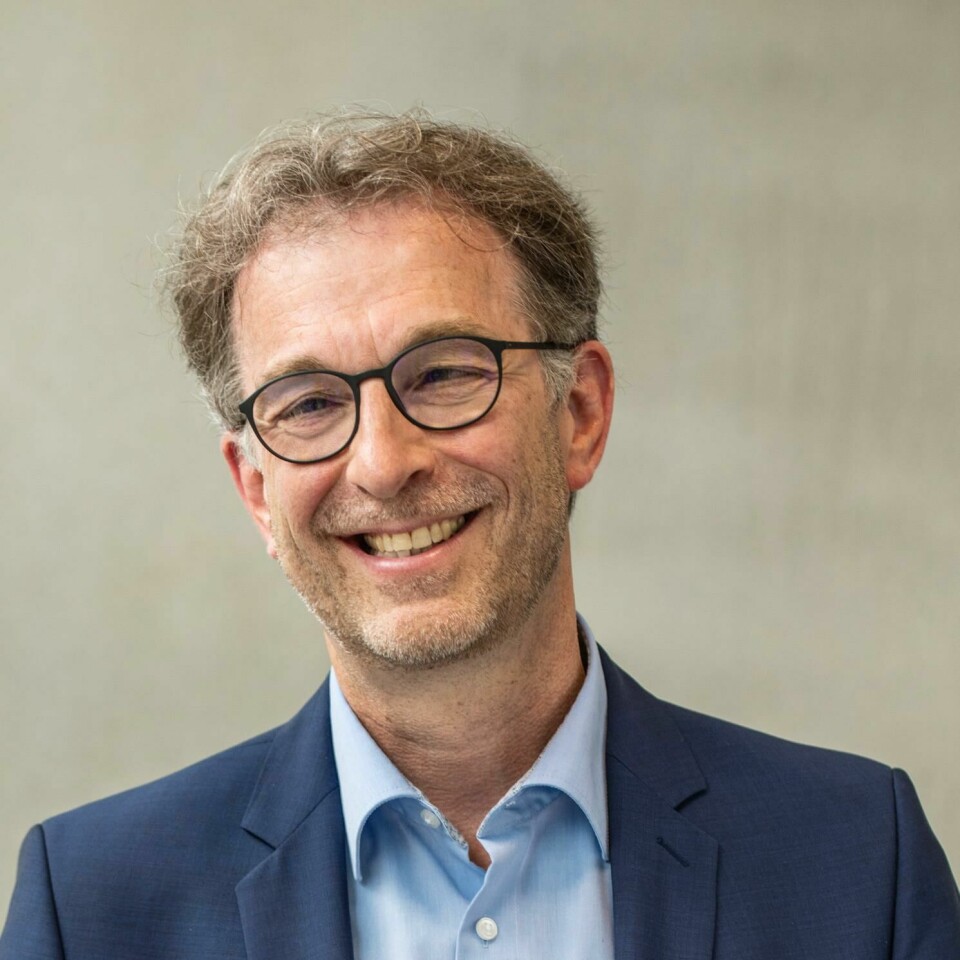
Dieter Braun, who has led Audi’s supply chain since 2019, has helped to develop the organisation across central and plant functions
The Supply Chain Planning function engineers the logistics network for all new Audi models through to start of production. This role is complemented by a lead in Supply Chain Pre-Series, which handles logistics for the early ramp up and launch phases.
Supply Chain Inbound covers inbound material transport planning and freight purchasing, while Audi’s International Supply Chain manages consolidation, packaging and shipment of knockdown kit (xKD) logistics to global plants, group and partner locations. The international group also includes a small in-house operation that manages xKD parts consolidation and packing.
Finally, a central Supply Chain Strategy and Cost Management team has overarching oversight of processes to create efficiencies and maintain strategic objectives as well as high level of standardisation through interdisciplinary teams across of all plants.
Logistics functions at plants are also assigned to the Supply Chain organisation and represented in the plant management of each plants. These teams are thus the operational link between suppliers and production, and responsible for shipping finished vehicles.
Whilst Audi’s Supply Chain organisation stands out in the Volkswagen Group for its integration, the team also coordinates with Volkswagen Group Logistics, which helps develop synergy and volume consolidation group-wide across plants for freight and containers. Audi’s finished vehicle volume is also bundled into shared logistics with the group across transport modes, including for ocean shipping on a fleet of ro-ro ships chartered or contracted by Volkswagen Group Logistics.
Group Logistics also works closely with Audi and other brands to coordinate on aligned strategic objectives, digitalisation and governance.

It includes key focus areas in logistics, including adapting for EV, order-to-delivery, sustainability, automation and more
The 360factory and logistics
In this multi-faceted organisation, Audi’s logistics and supply chain is part of the carmaker’s production organisation, led by board member Gerd Walker, to whom Dieter Braun reports. Braun points out that there is no separate supply chain strategy, and targets have been set in alignment with 360factory objectives, but with specific logistics and supply chain focus points.
The 360factory, first unveiled in 2022, is a vision to make Audi’s manufacturing and logistics more sustainable, flexible, digital, cost effective and with higher employee satisfaction.
A major plank of the production strategy is to transform Audi’s existing plants into state-of-the-art hubs for electric vehicle manufacturing. The strategy also sets out to electrify production by plant and region over different timelines, with all capable of electrification by the end of the decade. The supply chain and logistics teams support this transition closely, including in efforts to maintain flexibility at brownfield sites, especially amidst changing market requirements.
Today, Audi already produces two EV models and battery packs in Ingolstadt. Meanwhile, Audi’s newest plant, a dedicated EV factory with partner FAW in Changchun, China – where EV growth and penetration is fastest – started production in late 2024 and has incorporated high levels of automated material and AGVs. With further preparations for EVs, electric motors and battery packs underway in Neckarsulm, Győr and San José Chiapa, logistics will play major roles in the transition.
Along with supporting logistics in such transition, the 360factory’s core principles and focus areas each include important plans for the supply chain, from increasing efficiency along the order-to-delivery process through to decarbonising logistics, scaling automation and enhancing digitalisation.
Order-to-Delivery
With responsibility for the OtD process, Audi’s supply chain organisation helps to steer decisions across the business, such as supporting the choice of vehicle options and sales packages that deliver the most profit versus which variations might be creating cost and complexity in the supply chain. That creates a powerful basis to influence decisions in vehicle engineering, purchasing and supplier locations.
One important aspect of managing order-to-delivery is to have a view of working capital in the supply chain, both for material and finished vehicles. According to Dieter Braun, influencing these financial impacts is especially important when making decisions by considering all factors before developing the production and programme plan.
“We need to understand that the supply chain is about optimising financial as well as logistics flows, and that sometimes reducing capital in the supply chain is more powerful than cost reduction elsewhere,” says Dieter Braun.
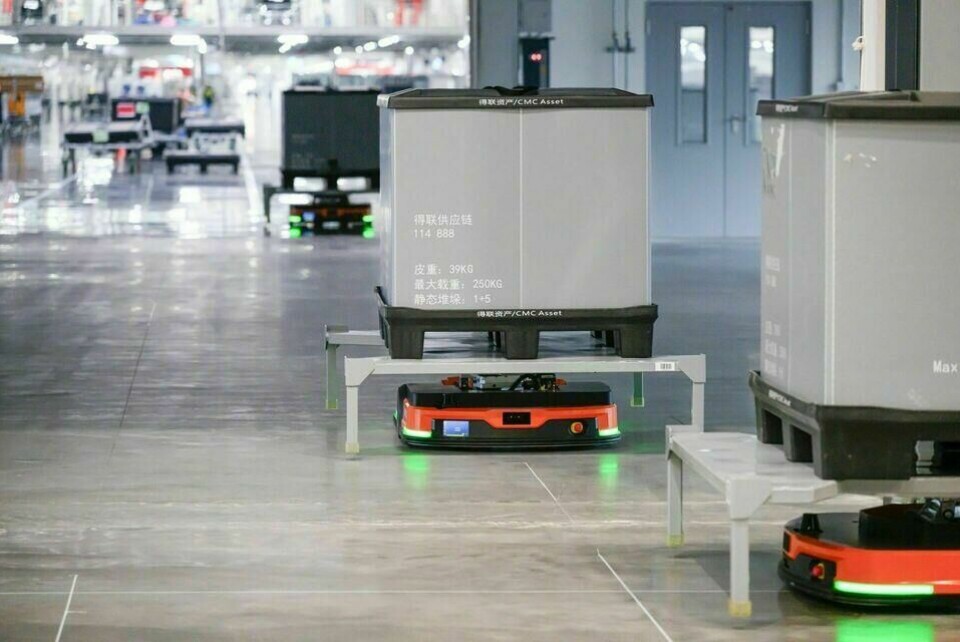
As part of its strategy to reduce parts complexity and optimise material flows, Audi has been able to achieve greater logistics automation at its new plant together with FAW in China
Cost reduction and automation
Other pillars of the 360factory strategy include a focus on lowering cost and improving productivity. Whilst supply chain and logistics teams must constantly benchmark and ensure that fixed costs and rates are competitive, lowering cost is not simply about squeezing suppliers or cutting investment. Instead, the supply chain team assesses costs more holistically, including productivity and efficiency gains, such as reducing complexity and implementing the right levels of automation.
The NEV plant in China, for example, has a high-bay racking system with automated storage and retrieval – an investment set to save significant costs. Likewise, reducing parts numbers leads to lower transport and handling costs, and the need for so much parts sequencing and supermarkets as well as improving resilience and prediction stability along the supply chain.
Decarbonisation and circular supply chains
As part of its Mission:Zero – Audi’s environmental programme for all production and logistics sites – sustainability is a key pillar of the 360factory. The main target was to make production sites net carbon neutral, which Audi achieved at the beginning of 2025. Audi is also focusing on resource and water efficiency, as well as increasing the use of recyclable parts and materials across operations.
The logistics team also has ambitions to reduce packaging waste. It collaborates in cross-brand initiatives led by Volkswagen Group Logistics that aim to eliminate plastics. Since 2020, the supply chain team has saved up to 650 tonnes of plastic annually across all locations in part through packaging designed together with suppliers with a focus on high utilisation rates, by using reusable containers and retooling existing equipment where it makes sense. Braun anticipates making further gains through collaboration with engineering early in vehicle development phases.
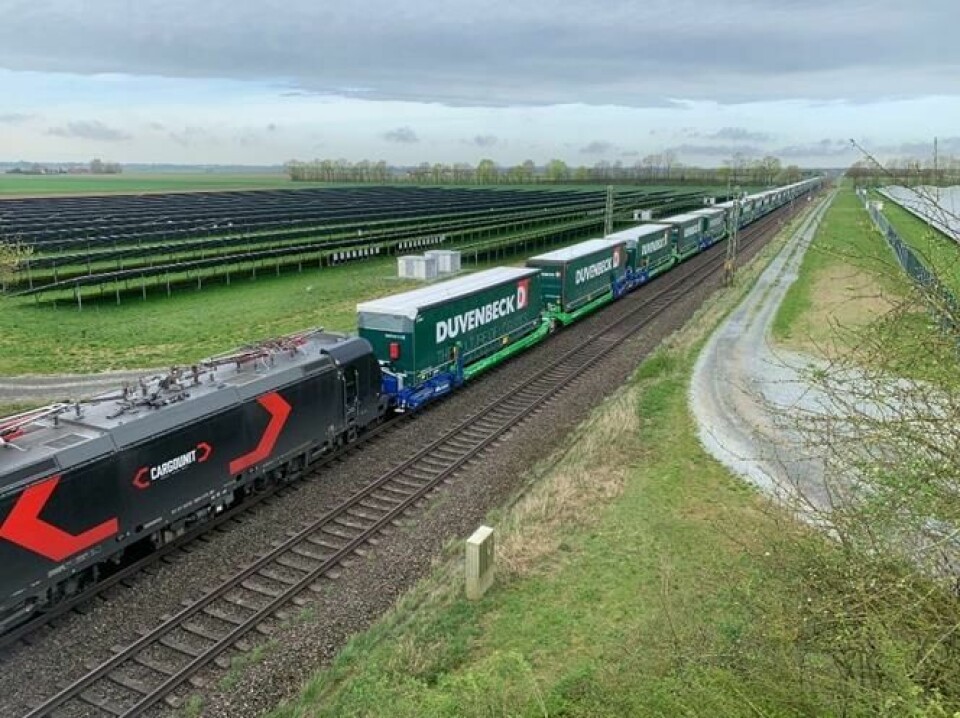
A focus on flexible intermodal transport, including with key equipment, truck and rail partners, has helped Audi to reduce transport emissions
Audi has also expanded the use of emission-free rail transport services for vehicle logistics, and alternative fuels for trucking. Using innovative new technology and rail wagons from its partner Helrom, meanwhile, the carmaker has shifted a significant share of material between Germany and Hungary from road to intermodal rail, with plans to expand services.
Team.work
A key aim of the 360factory is to make production and logistics at Audi a more attractive employer, including objectives to increase working flexibility and make work environments more comfortable. The company has increased the number of women managers in supply chain whilst offering more leadership training, and programmes to support health and well-being.
Upgrading logistics systems and technology to more modern, user-friendly systems can also help to attract workers and help them to be more productive.
For Braun, the supply chain’s responsibility for the order-to-delivery process is also a way to directly attract and retain workers and offer them career development. “For someone at the start of their career, or looking for progression, it’s a big opportunity to work with different experts and address so many topics in one organisation,” he says.
Digitalisation and automation
Audi leverages digital solutions to enhance efficiency and to create more flexible manufacturing and logistics processes. In the 360factory strategy, Audi points specifically to data integration that will allow for a greater visibility of processes, for example.
It is similar for logistics, as Audi strives to digitalise information and automate key process steps, with ambitious plans to digitalise inbound, inhouse and vehicle logistics processes over the next decade as part of its long-term goals. The carmaker recently implemented a ‘Group Tower’ that covers plants in Europe, for example. Plant dispatchers use this frontend application, which integrates data from all shipments with key logistics and inventory information.
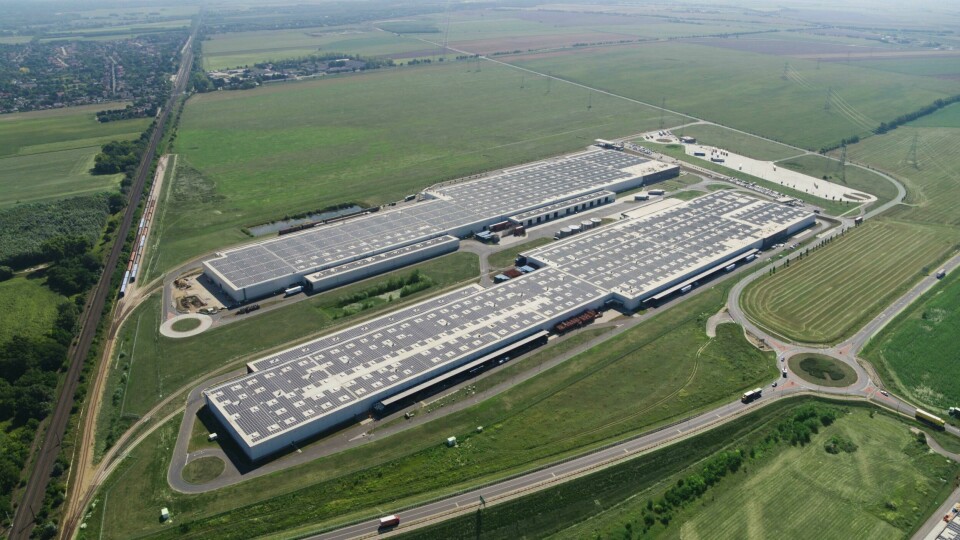
By combining various IT systems and, Audi has been able to integrate visibility on transport flows, critical inventory and dispatch operations
The Group Tower helps to assess master parts and logistics data, including critical inventory lists, with real-time information of that material from various source systems. As well as helping to monitor and anticipate disruptions, the system enables each dispatcher to handle more parts.
Artificial intelligence is also playing a growing role in Audi’s production and logistics, for example in error detection, compliance and quality control, and other innovations that are coming “bottom up” from specific operations, according to Braun. Audi and Volkswagen Group’s participation in the Catena-X data standards group will also help the carmaker to implement other opportunities AI opportunities in production.
But for generative AI (genAI) and large language models (LLMs), for which data strategy and quality is so important, in the supply chain Audi wants to take a “top down” approach and concentrate efforts specifically on optimising order-to-delivery analysis and simulations.
With the right data strategy, genAI could help Audi to process large amount of data across the supply chain simultaneously, rather than sequentially. This approach would help to assess and simulate decisions across the order-to-delivery process, for example the impacts of different vehicle configurations and engineering changes.
“We want to take a top-down approach so that we can use the technology to support our end-to-end ambitions. We don’t want to use AI to separately optimise decisions in the sales, production and purchasing, but instead to bring it all together,” says Braun. “That will help us to make better decisions, faster.”