Mexico now seventh largest auto producer with 3.8m vehicles made and exporting 3.3m units globally
There is a high demand for the parts supplied by Mexicoʼs tier one suppliers, with 87% production going for export, making it a powerhouse for the wider North American automotive market. Automotive Logistics talks to some of the leaders about maintaining a resilient supply chain.
Sitting at the centre of two vast continents, Mexico is uniquely placed logistically to supply automotive components but it is the magnetic pull of its giant and powerful neighbour to the north, which has led myriad suppliers and OEMs to beat a path to the centrally located country.
And pour into Mexico they have, generating some seriously eye-catching statistics. According to the Mexican Automotive Industry Association (AMIA), last year saw the automotive sector account for 4.7% of national GDP and 21.7% of manufacturing GDP, generating a million jobs along the way.
Mexico is the seventh largest vehicle producer in the world at 3.8m units – with 3.3m of those destined for overseas markets – while it is also the 12th largest seller of light vehicles globally.
This veritable boom is partly fuelled by the US-Mexico-Canada (USMCA) agreement, but all eyes are currently on the White House as Mexico-based manufacturers look to see what policies Washington adopts to the auto sector.
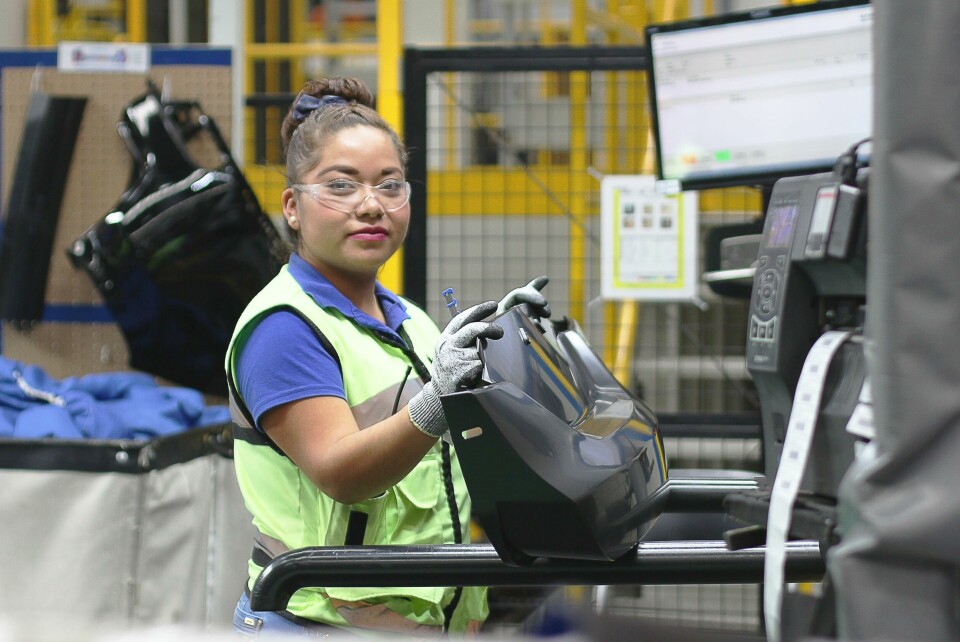
Magna employees need strong analytical and problem-solving skills, proficiency in digital supply chain tools, and an understanding of lean manufacturing principles.
Significant improvements
According to the Office of the United States Trade Representative report to Congress on the operation of USMCA, the deal has had a “positive economic impact” on the North American automotive industry.
The report notes that following “significant improvements” brokered between Congressional Democrats and the Trump Administration, including a facility-specific labour Rapid Response Mechanism (RRM) and the strengthening rules of origin in the automotive and steel sectors, the USMCA won “overwhelming bipartisan support in the House and Senate.”
Replacing the old North American Free Trade Agreement (Nafta), the report details how some of the “most meaningful and novel provisions in the USMCA are specific to automobiles.”
These provisions include new rules of origin (ROO) requirements, which are intended to be stricter and were updated to improve the distribution of supply chain benefits between the US Mexico and Canada.
“USMCAʼs stricter rules of origin, particularly the higher regional value content (RVC) requirements, have significantly impacted sourcing strategies”
Misti Rice, Magna
“They also include the RRM, which, when paired with the new automotive provisions in the USMCA, provides an innovative tool to empower workers to exercise their rights to organise and bargain collectively,” says the report. Some 66% of RRM cases to date have been in the autos sector.
Mexico’s parts association
Mexico’s National Auto Parts Industry association (INA) underscored just how important a sector it represents is by noting 87% of its members’ production is for export and 13% for domestic.
According to the association, there are no specific component supply issues at present, with parts being delivered on time to OEMs in Mexico, while INA executive president, Francisco González told Automotive Logistics that “growing demand for more efficient, safe and sustainable vehicles has driven companies to innovate, adopting new technologies and materials, such as plastic.”
In terms of component distribution, road transport accounts for the vast majority at 85%, with train (7%), sea (4%), air (2%) and others (2%), making up the rest.
So, what is INA’s role in talking to national and local governments to best represent its members’ interests?
“INA represents the auto parts industry before local, state and federal governments, leading industry actors and international organisations to ensure its members have a voice in global business and regulatory matters,” says González. “We set up meetings with key government officials to discuss the industry’s interests [and] encourage the industry’s different players to enter into agreements, discuss problems and propose solutions to them, depending on their level of priority.”
Working with the government INA promotes national and regional development by growing existing investment and promoting new investment in the automotive parts sector.
The body listed several key skills for automotive component staff to possess such as supply chain management, the ability to analyse sales data and market trends, using data analysis tools that facilitate visibility and control of the chain, as well as an ability to quickly adapt to changes in demand or market conditions.
Maintaining that Mexico is currently strengthening its tier two and tier three chain to reduce imports and increase the value of regional content, the INA chief also addressed the rules-of-origin issue.
“This year, companies are already complying with 75% of the regional content value and companies are developing local sourcing to reduce imports,” notes González.
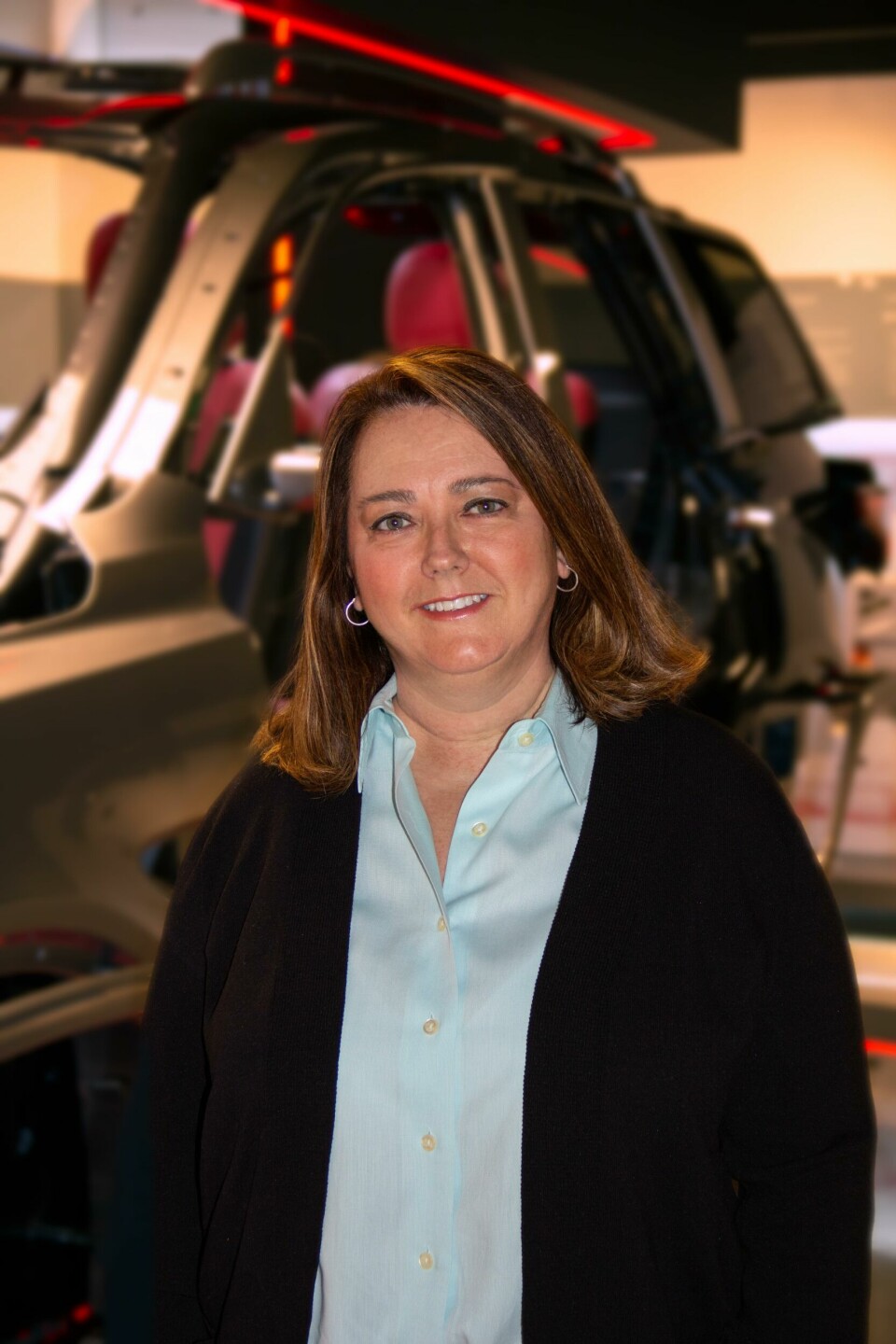
Rice says Magna has adjusted its supply chain to prioritise North American suppliers and meet these elevated regional value content thresholds.
Magna reacts to higher RVC thresholds
Magna has a significant presence in Mexico, so how is the USMCA deal working for the supplier, particularly as rules-of-origin content for vehicles are being made more complicated?
“USMCA’s stricter rules of origin, particularly the higher regional value content (RVC) requirements, have significantly impacted sourcing strategies,” says Magna executive director for government affairs, Misti Rice.
“At Magna, we’ve adjusted our supply chains to prioritise North American suppliers to meet these elevated RVC thresholds. This shift has driven investment in local production capabilities across North America to ensure compliance and mitigate risks.”
How does Magna view the attitude of the Mexican government towards auto suppliers and does company have a role in lobbying the administration?
“The Mexican government has been broadly supportive of the auto sector, acknowledging its critical role in Mexico’s economy,” noted Rice. “However, there are ongoing challenges in labour compliance, infrastructure and customs efficiency.
Maintaining Mexican competitiveness
“Magna remains active in advancing policies that streamline customs processes, enhance infrastructure and ensure labour regulations do not disrupt supply chains. Our advocacy also focuses on workforce development, recognising the importance of a skilled labour pool to maintain Mexico’s competitiveness in the global automotive landscape.”
At the time of press, the US election is unknown, but Mexico is somewhat of a political hot potato, both from a manufacturing and immigration standpoint, so what is Magna’s view as America goes to the ballot box?
“The US election will have significant implications for the automotive industry, especially on trade and labour policy,” says Rice. “Both candidates have signalled intentions to bolster US manufacturing, but their approaches could diverge.
Rice says that if the next US administration leans toward protectionism, it may affect cross-border supply chains and suppliers with operations in Mexico. “However, policies that incentivise investment across North America could enhance regional competitiveness, benefiting Mexico as an integral part of the supply chain,” she adds. “We are carefully tracking how potential policy shifts might influence trade agreements and supply chain regulations.”
It seems both US presidential candidates are advocating a more robust approach to ensuring manufacturing in America is a priority, but could this lead to protectionism taking centre stage?
“Both candidates advocate for stronger domestic manufacturing, but the scope and implementation of protectionist measures could differ,” says Rice. “If more aggressive trade policies are adopted, there may be increased barriers to cross-border operations, which could impact the broader North American supply chain.
Rice says Magna supports policies that enhance North America’s collective competitiveness rather than individual nations. Strengthening regional trade collaboration and competitiveness is key to ensuring North America remains a global automotive powerhouse, according to her.
“Regardless of the election outcome, suppliers must remain adaptable to navigate policy changes and maintain innovation,” she says.
A sizeable portion of Magna’s production supports OEMs in Mexico, particularly for assembly plants servicing the North American market. However, the supplier’s footprint extends beyond Mexico to the US and Canada, as well as European and Asian markets.
Increasing buffer stocks
So, what are tier-n suppliers and logistics providers doing to build resiliency into the supply chain?
“Tier-n suppliers and logistics providers are adopting multiple strategies to increase resilience, such as diversifying sourcing options, nearshoring and increasing buffer stocks for critical components,” says Magna’s vice-president of operations, Kathy Worthen.
“Many are also leveraging digital supply chain tools and predictive analytics to identify and mitigate potential disruptions before they escalate,” she says. “Key challenges include port congestion, changes in volume demand and/or mix, fluctuating transportation costs and delays due to cross-border regulations. Additionally, supply chain shortages and volatile lead time, particularly for electronics and raw materials, continue to impact inbound logistics.”
Magna also cites a range of other challenges including unpredictable transport timelines, changes in volume and mix releases, customs delays and regional disruptions. To address those issues, the company says it is working on “building more resilient supply chains” by diversifying suppliers, improving forecasting accuracy with digital tools and collaborating with logistics providers to streamline customs processes and ensure real-time visibility of shipments.”
Digital suite
Magna is also using digital technologies to make logistics processes in Mexico more efficient, traceable and secure.
“Magna has implemented several digital tools such as real-time tracking systems, AI-driven supply chain platforms and predictive analytics to enhance efficiency and traceability,” notes Worthen. “We are also investing in blockchain technologies to further secure the movement of high-value parts across borders.”
Worthen points out that Magna has made considerable strides in upgrading transport and warehouse management, including the adoption of automated warehouse systems and enhanced routing software for logistics. “We have also refined our inventory management with just-in-time delivery models and predictive stocking based on real-time demand analytics,” she says.
Employee buy-in is important with staff needing “strong analytical and problem- solving skills,” proficiency in digital supply chain tools, and an understanding of lean manufacturing principles. Training in advanced logistics software and real- time data interpretation is also critical for enhancing inventory and distribution efficiency.
“Greater localisation is reducing lead times and transportation costs,” adds Worthen. “Magna is increasingly focusing on sourcing locally to mitigate risks associated with global supply chain disruptions and streamline delivery processes.”
Worthen recognises a shortage of tier two/three suppliers for some commodities, especially for specialised components, which challenges localisation sourcing strategies. Magna is working to develop and support the growth of local suppliers, while also diversifying its sourcing strategy to ensure continuity and competitiveness in its supply chain. “We will continue to maintain a global supply chain but drive the procurement strategies to optimise the end-to-end supply chain.”
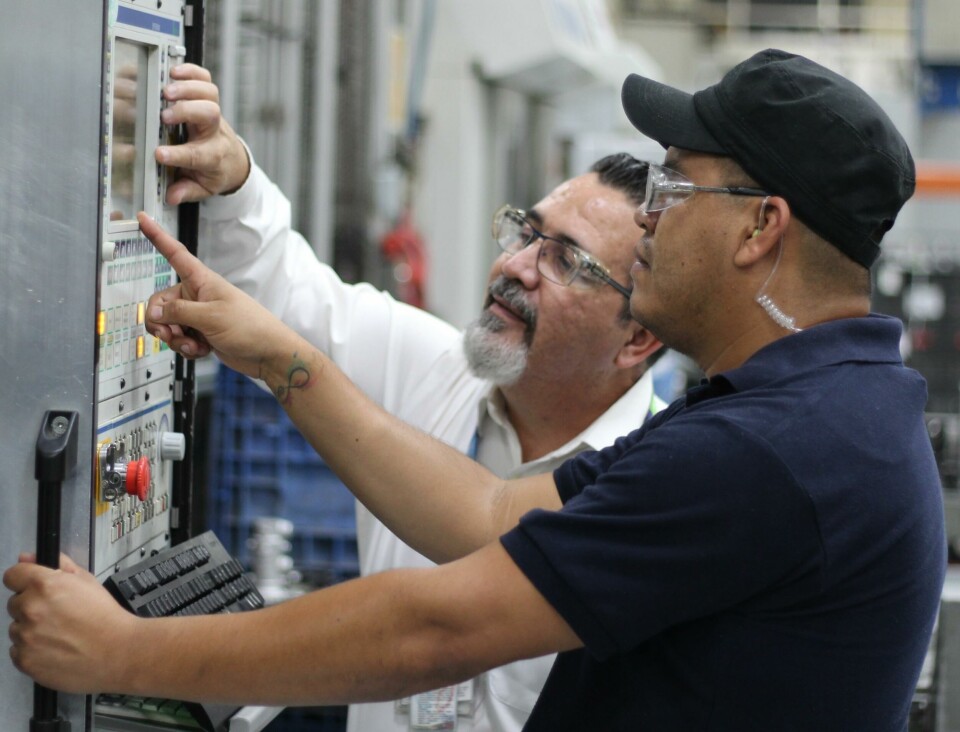
Bosch has invested $1.5 billion into the expansion of four plants in Mexico focusing on automotive components, steering and braking systems, including at its facility in Aguascalientes.
Bosch expands in Mexico
German supplier Bosch has been in Mexico since 1955 and has a colossal operation there, currently employing 20,000 staff in the country where it has 16 locations, including 13 manufacturing sites.
In 2023, the company generated sales of $4.2 billion in Mexico across four business sectors: Mobility, Industrial Technology, Consumer Goods and Energy, and Building Technology.
“We are committed to achieving profitable and sustainable growth in Mexico, which is considered a strategic location due its infrastructure, talent, trade agreements and geographical position bordering the US,” says a Bosch spokesperson.
“In the last two years, we invested more than 25 billion pesos ($1.5 billion) into the expansion of the plants in Juárez, Celaya, Querétaro and Aguascalientes, focusing on automotive components, steering and braking systems.
Bosch is looking to grow its Mobility business unit in the Americas and Mexico plays an important role in this. The supplier has the technology and talent to develop solutions in electrification, software and automation.
“One key factor for success is the local- for-local approach; Bosch manufacturing operations are located where its customers are,” says the company’s spokesperson. “The company draws mainly on regional sources of supply, shortening supply chains and making them less vulnerable. For this reason, the local supplier market in Mexico is already very important.”
Bosch is keeping its cards close to its chest with the US election, noting it does “not specifically endorse political candidates or parties” and that: “As we have with the previous and current administrations in the US, we will strive to be a technical resource to authorities in the US as they consider the impact of policy and regulation into the future.”
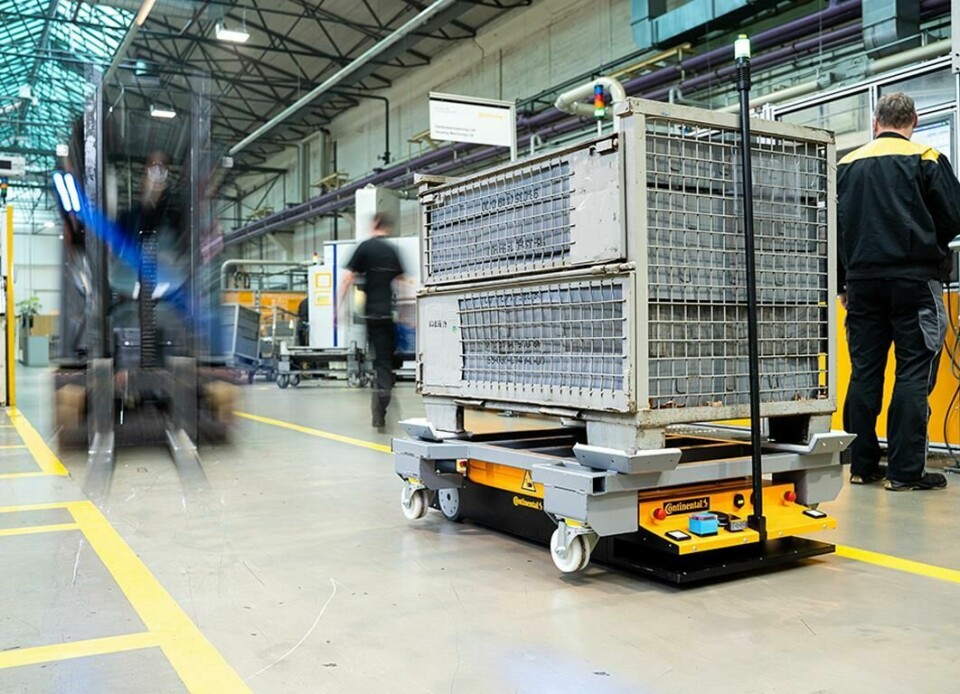
Continental maintains operations with an overall uptime of 99.7% and a MTBF of more than 3,000 hours.
Continental launches Smart Warehouse
Continental has a very large presence in Mexico with 21 locations which include production plants, offices, research and development centres as well as financial hubs, employing more than 23,000 people in total.
The supplier makes a range of products including tyres, rubber hoses, start/stop buttons, instrument clusters, chassis position sensors, electronic suspension systems and wheel speed sensors, as well as a range of other modules.
In terms of the USMCA, a Continental spokesperson notes the supplier is “globally in favour of the free market and any treaty at the global level is beneficial for the global economy.”
Earlier this year, Continental started operations at its Smart Warehouse, a $3.3m facility at Continental’s Periférico plant in Guadalajara. Known as AutoStore, the material storage and assortment system features robots, reticles, receivers, ports and controllers.
The supplier said the AutoStore, which opened in 2002, achieves “ultra-dense storage” that increases its capacity by up to four times compared to manual warehouses. It has the equivalent of 7,000 effective cubic metres of storage.
Continental maintains operations with an overall uptime of 99.7% and a mean time between failures (MTBF) of more than 3,000 hours. Independently controlled modules and troubleshooting software make system outages rare and solvable without the need to shut down operations.
“This system allows us as a plant to have an extreme use of the space on the production floor… increasing efficiency in material handling,” says the Periférico plant’s general director, Sergio Márquez Oriza. “All this helps us enormously in continuing to deliver the best quality products to our customers and meeting delivery times,” he says.
The facility is dedicated to the design, manufacture and testing of clusters of analogue and digital instruments, as well as head up devices for both light vehicles and commercial vehicles, serving mainly the North American market.
Thyssenkrupp Materials de México
Thyssenkrupp has been producing automotive parts in Mexico for a long time and underlines the importance of the country, which it says has seen Audi, BMW, Ford, General Motors, Honda, Kia, Mazda, Nissan, Toyota and Volkswagen all beat a door to it to export their vehicles to North America.
As the supplier notes: “There is therefore a great need here for high-performance services, as at its three steel service centres in Mexico to date, the materials experts provide services for their customers throughout the Mexican automotive sector.
These include logistics, warehousing and management, pre-processing, just-in-time delivery, as well as technical services, raw material purchasing and import. This means steel and aluminium do not have to be procured, stored and prepared by the auto manufacturers themselves.
At the start of this year, Thyssenkrupp Materials de México ploughed $37m into a new service centre in San Luis Potosí, creating 65 jobs, with the facility catering for automotive trends such as sustainability and electromobility, particularly for light vehicle production.
“The [AutoStore] system allows us as a plant to have an extreme use of the space on the production floor… [and it] increases efficiency in material handling. All this helps us enormously in continuing to deliver the best quality products to our customers and meeting delivery times”
Sergio Márquez Oriza, Continental
The new facility is part of Thyssenkrupp Materials Services’ growth strategy in North America, a region in which the company has invested more than $100m in the last two years. It will join three other service centres located in the country in the cities of Saltillo, Puebla and Silao.
The latter has a steel and aluminium blanking line and, since it is 170km from the new site, will operate in conjunction with it, making them the only two facilities in the country to offer the service.
“The needs and requirements of the industry are changing rapidly,” said Thyssenkrupp Materials Services CEO, Martin Stillger. “In the context of the major transformation issues of electromobility, sustainability and supply chain resilience, Mexico is a clear growth market for us. Here we can support customers with our Materials as a Service strategy, precisely in these key areas.”
The new facility features a Schuler cutting line, allowing the cutting of raw pieces of aluminium and high-strength steel used in the automotive industry.
Thyssenkrupp Materials de México now has four service centres in the country, which are located close to numerous OEMs and suppliers. Delivery routes will be shorter and the direct connection with the railway line of the San Luis Potosí facility enables operations to be carried out in a manner that is “more profitable and sustainable,” maintains the company, in addition to just-in- time deliveries.
All aluminium blanks destined for the automotive industry that are not produced in these facilities will need to be imported as prefabricated parts from the US.