Dieter Braun, Audi
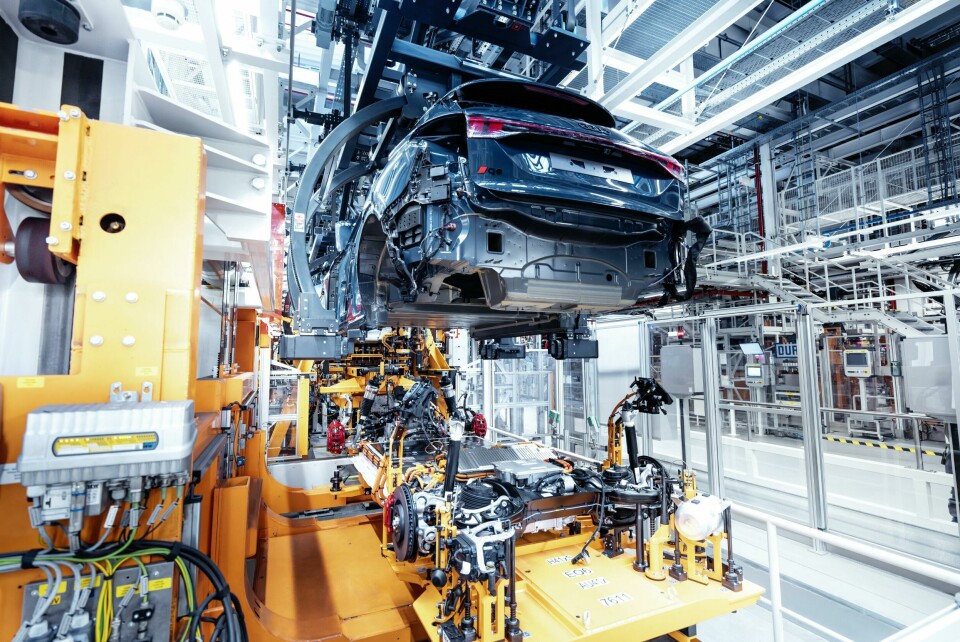
Dieter Braun on how Audi is turning supply chain motion into progress
In the first part of a special interview series, read how Audi is confronting challenges in the automotive market with an emphasis on a holistic supply chain function that makes a positive contribution to the carmaker’s production and products. Head of supply chain Dieter Braun reveals how logistics can add value across the order-to-delivery process.
Audi supply chain series: Adding value through logistics
-
Dieter Braun on how Audi is turning supply chain motion into progress
-
Infographic: A snapshot of Audi’s production network and supply chain
-
Audi’s supply chain organisation: Logistics and the 360factory strategy
-
Audi’s supply chain in 2033 and beyond: Designed to combine logistics, automation and people
-
Breaking new ground: How Helrom’s Block Train is transforming Audi’s supply chain network
-
Red Sofa interview | Audi and Helrom discuss scaling sustainable rail logistics at ALSC Europe
Managing uncertainty remains the leitmotif for automotive supply chain leaders in 2025. Indeed, that has been the case for most of the same time since Dieter Braun took over leadership of the overall supply chain function at Audi in 2019, helping the premium OEM navigate logistics through the pandemic, chip, material and transport shortages. Braun and his team have used the past half decade to hone a supply chain vision that aims to make Audi even more resilient, sustainable and competitive – even as the task becomes more complex across volatile markets, technology transition and rising trade barriers.
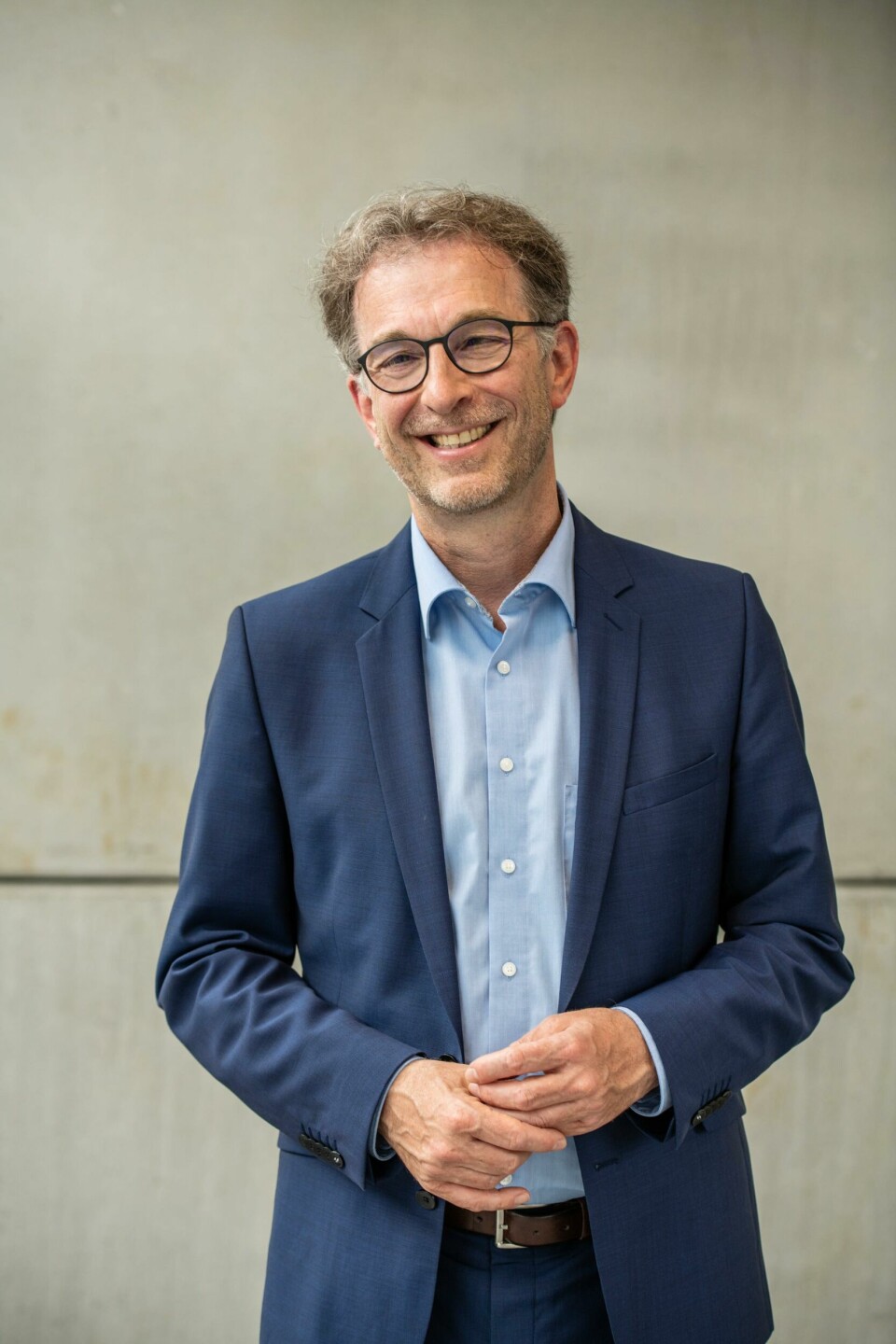
Under Dieter Braun, Audi’s supply chain team aims to provide an integrated view of the entire order-to-delivery process
For Braun, one of the most important means to achieve this resiliency will be for his teams to have greater influence on reducing logistics and supply chain complexity itself. “Logistics can serve as value creator for the company by having a deeper influence on how we work and on the conditions of our future production network,” he says.
He points especially to how, with the right understanding and visibility across processes, a strong supply chain function can help to reduce part numbers, localise key modules and minimise material handling, which in turn lowers transport costs and emissions whilst enabling more material flow automation and strengthens resilience along entire the supply chain.
Supply chain leaders at other automotive manufacturers are also striving to exert greater influence, from sales and operations planning (S&OP) to influencing engineers during the development phase of new vehicles. But silos often still exist between logistics and other departments, whether R&D and purchasing, manufacturing and sales. Many OEMs have also historically treated logistics functions with a focus on transport cost, quality and delivery times, along with material fulfilment at plants.
Braun admits that such gaps existed at Audi, too, including data silos between customer demand, production and supplier planning, material handling and finished vehicle delivery, a process which Audi calls ‘order-to-delivery’ (OtD). In principle, the supply chain organisation at Audi was always responsible for OtD, but several changes and events over recent years have brought it into sharper focus. “We figured out that order-to-delivery was a diamond in need of polish,” said Braun.
The supply chain team has now more responsibility for better integrating and improving order-to-delivery across the company. For example, it contributes to better translating customer demand into supply chain requirements and better understanding the influence of model configuration on the number of parts to handle, including impacts for logistics, inventory, material and packaging flows – and ultimately on profit margins.
“We have to optimise not only logistics flows but also working capital and financial flows, and to make sure that we make decisions based on these combined KPIs,” Braun says. “A holistic order-to-delivery process must consider the impact of decisions not only on cost, but earnings.”
Audi’s logistics evolution: End-to-end value creation
The main shape of Audi’s supply chain department took form after a reorganisation in 2020, when there was a shift into a more integrated Supply Chain function (read more on Audi’s supply chain and logistics function here). The supply chain organisation consolidated responsibility for central logistics steering, planning and cost management, through to transport and plant logistics functions. The carmaker’s supply chain team also works closely with Volkswagen Group Logistics (Volkswagen Konzernlogistik), notably on group-wide transport and logistics synergies, sustainability and digitalisation projects.
In 2022, the rollout of Audi’s overarching production strategy, 360factory, refocused several logistics priorities as the carmaker set out its ideal manufacturing conditions, including ambitions to redevelop existing plants and logistics to be more sustainable, flexible, efficient and competitive. Drivers of this transformation include greater digitalisation and automation and reducing unnecessary complexity.
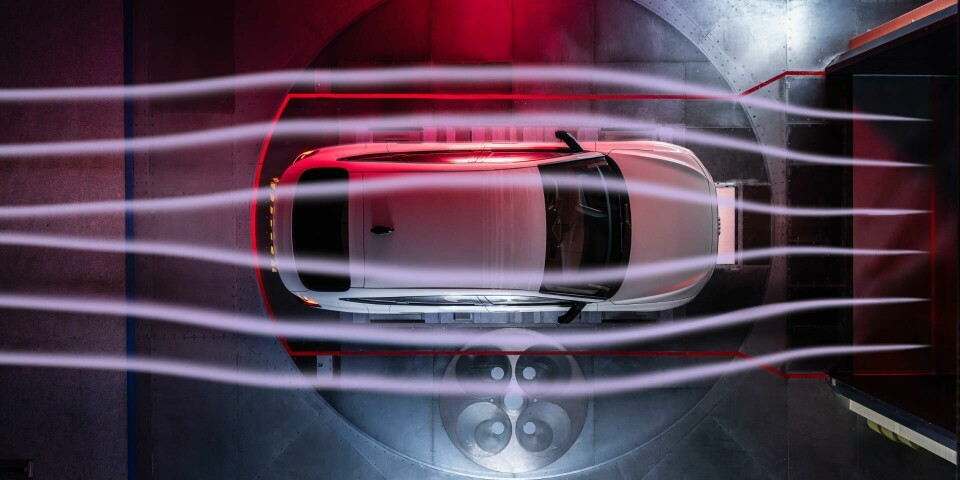
This perspective includes efforts to influence and reduce product and parts complexity in new vehicle programmes, working closely with Audi’s engineering and procurement teams
In the years since, Audi has further developed and articulated its supply chain vision and target for the future – notably in sustainability, cost efficiency, flexibility and employee attractiveness. In its target picture for the supply chain in 2033, Braun and his team have articulated an overarching objective for supply chain to be a driving force in the company’s operational and financial performance: Turning Motion into Progress.
The key aspect of this strategy is that Audi’s supply chain encompasses and considers all aspects in a holistic and equal way, including sustainability, automation, digitalisation, competitiveness and efficiency. According to Braun, all activities are consistently aligned with these target dimensions and with the wider production and group strategy.
“We focus on active implementation, despite difficult framework conditions, which we also try to change and shape,” says Braun. “The basis for this is our organisation and our defined common principles.
“Building and improving the end-to-end perspective across the order-to-delivery process will in many ways be how the supply chain organisation adds the most value across Audi, and its most crucial contribution to the 360factory strategy and this makes the difference.”
Supply chain influence: dousing the flames of complexity at the source
In today’s fast-paced automotive industry, carmakers must rapidly adapt their supply chains to maintain stability and enhance financial performance. This involves re-engineering logistics, modifying production networks, and simulating responses to sudden regulatory or trade policy changes. Both Audi and Volkswagen Group Logistics have invested in systems and processes to improve supply chain visibility and flexibility, including a better integration of logistics data and tracking across key flows in the network. Furthermore, the carmakers’ commitment to common data standards and exchange as part of the Catena-X initiative aims to enhance data exchange and visibility with supply chain partners.
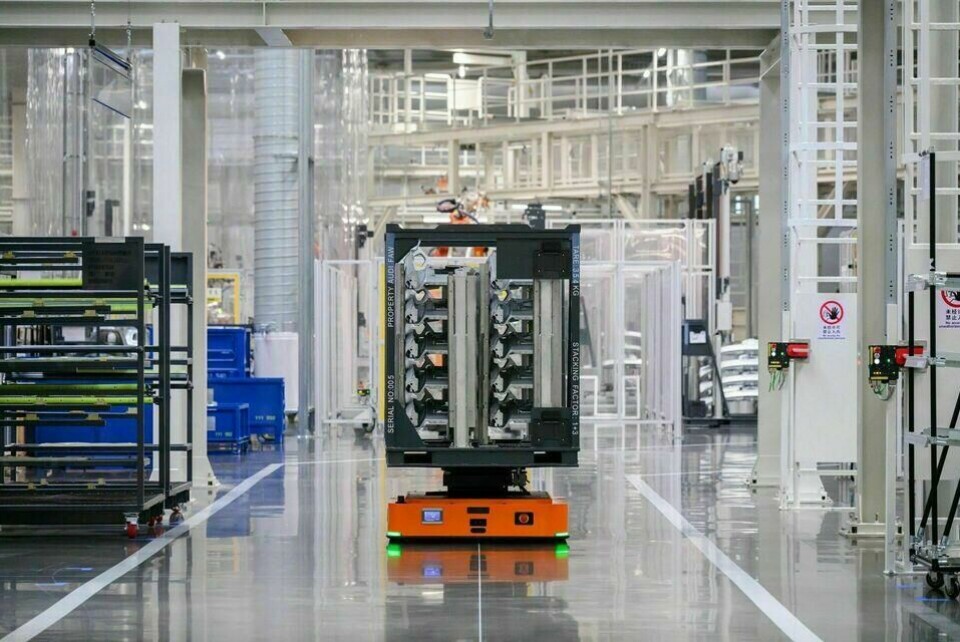
Audi and FAW’s new NEV plant in Changchun, China (pictured) has a high level of logistics automation and AGVs thanks to an optimised plant layout and material flow
But to create value and turn motion into progress, Braun is determined that the supply chain needs to take a more active role in driving long-term business decisions. One of the most critical areas for Audi’s supply chain is in reducing complexity from the beginning of vehicle development.
For both existing and new model programmes, Audi’s supply chain outlines an ideal end-to-end approach, a process that Volkswagen Group Logistics also supports where relevant. For example, the supply chain team from Audi’s plants in Germany and Mexico worked closely with local planners on processes and layout for optimal logistics at the carmaker’s NEV plant in Changchun, China – a majority-owned facility dedicated to EVs with Chinese partner, FAW, which started production in late 2024. Partly as a result, the plant has a strongly localised supply base of components and modules, with simplified material flows and high levels of automation.
Braun likens efforts to contain complexity in the supply chain to managing a fire at its outbreak. If you see the fire in the first minute, you can extinguish the flames with a bucket of water. Ten minutes later and you need a fire brigade to control it. After an hour, the house has burned down.
“If operations are already fixed, we have limits on how much we can optimise. But where we can influence the setup already on, we can have a significant impact on the entire company,” he says.
Defining and calculating part number impacts
For a premium carmaker like Audi, model variety and options are part of its business model and can also be very profitable. It is therefore important to distinguish between variation that adds value for the customers versus part variations that bring few if any benefits, and which add complexity as a byproduct.
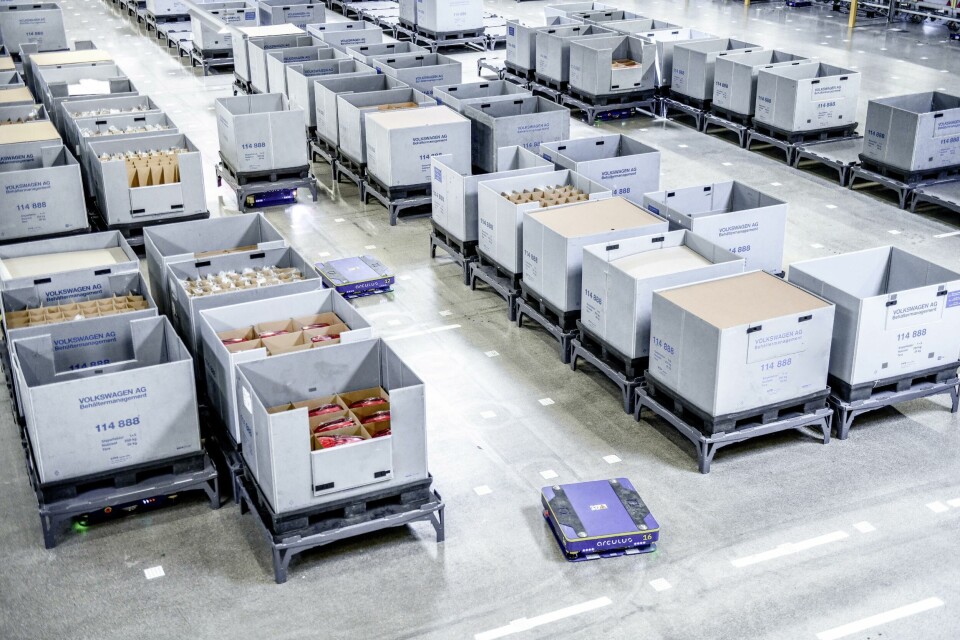
High parts numbers require more supermarkets for kitting and sequencing, such as at Audi’s plant in Ingolstadt (pictured), which the supply chain team wants to reduce for future models
That is why Audi’s supply chain team has focused on key measures to improve this visibility. One is through improved data integration that helps to capture cost, time and risk factors, for example. It is also collaborating with engineering and sales to determine the impact of vehicle package decisions on part numbers. By mapping how sales configurations translate into production complexity, the company can eliminate redundant variants. But equally, it can track where orders are meeting specific customer demand and improving financial returns.
“We have improved our data visibility across orders back to part numbers and inbound logistics and try to detect how a part number came into life and why,” he says. “We then try to influence the creation of part numbers and to reduce them, but always with end-to-visibility based on customer orders.”
“We have to optimise not only logistics flows but also working capital and financial flows, and to make sure that we make decisions based on these combined KPIs. A holistic order-to-delivery process must consider the impact of decisions not only on cost, but earnings. -Dieter Braun, Audi
At factories, for example, high part varieties increase the need for floorspace dedicated to such supermarkets, where more workers are required to sort, sequence and kit material. By combining more single parts into modules, these systems can be moved directly from docks or storage to the line. Furthermore, creating variance at the end of the line, for example in assembly, helps to reduce complexity in the material flow. All these often result in more opportunities for simple, scalable automation.
Such automated material flows are evident in the NEV plant in China, but much harder to achieve in existing plants. “Our task in logistics is to clean up this situation wherever possible,” says Braun. “We want to create a leaner value chain with standardised processes and bring it closer to an ideal situation.”
Braun acknowledges that the impacts that higher part numbers can have across the wider company are not always immediately recognisable. “For us as logistics – standing at the end of the chain compared to the tip of the iceberg – the effect of variance is physically visible in our supermarkets,” says Braun. “But there would also be savings in other areas below the water surface, such as engineering, quality or purchasing, because parts would not be developed, tested, procured etc.,” emphasises Dieter Braun.
The supply chain group is therefore working more closely with other departments, including holding regular deep-dive workshops and tours of parts supermarkets to show the impact that specific part variations have on production and logistics.
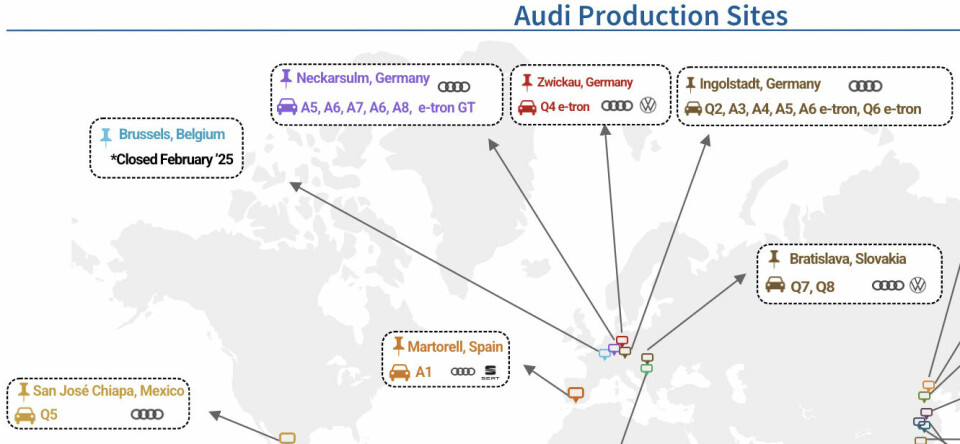
Click here to find out more about Audi’s global plant and logistics footprint
For example, shaping the design of more modules can influence sourcing and make/buy decisions. Single part numbers might be procured from far away supplier locations and remain competitive on total cost, even if logistics emissions and risks are higher. However, consolidating more parts into larger modules often makes it more beneficial to localise production either onsite or close to final assembly locations, especially to reduce transport emissions.
“Encouraging more modules tends to lead to higher localisation to a certain degree, which can reduce investments, working capital, emissions, risks and logistic costs,” says Braun. “But it is important to have the combined view and ensure that we have common targets.”
These shared goals are critical to how Audi works with engineers and purchasing to influence design and production decisions, including defined targets for part numbers for new vehicle programmes together with R&D. The supply chain team has also identified a list of the most critical heavyweight part numbers: if engineers stay within a certain range of these part types, it won’t cause problems for logistics; but as these heavy parts surpass the threshold, supply chain and R&D teams need to review them and find a solution together.
This process has been more deeply embeedded in the design of future Audi models, and Braun expects to realise its full impact in upcoming vehicle generations, including significant reductions in parts sequencing and all related expenses.
A sustainable logistics mission
Together with its partners and stakeholders, Audi is actively shaping its logistics network and operations to meet objectives in sustainability. For example, the carmaker will cut logistics emissions and reduce packaging waste as part of its Mission:Zero project. Since the beginning of 2025, Audi has achieved carbon net neutrality at its production plants. It aims to be net carbon zero across the company by 2050.
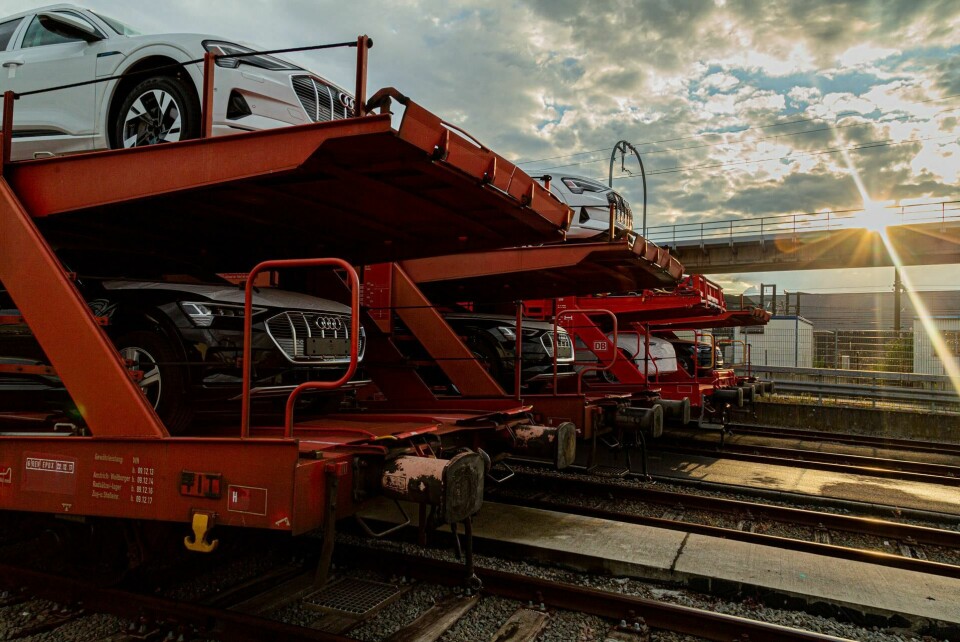
Audi has reduced emissions in logistics thanks to the use of rail freight, biogenic fuels in trucking and LNG for ro-ro shippping, with plans to expand use of alternative fuels and trials with e-trucks
The carmaker has made progress on the path to interim goals. The supply chain team has reduced packaging waste by up to 650 tonnes annually across all plants, including a significant reduction in interior filler packaging thanks to adapting materials and changing packaging design. Braun points out that this transition has been lengthy, especially as suppliers have not yet fully developed awareness of sustainable inner packaging.
Audi’s supply chain team has thus developed a packaging database that offers a quick overview of sustainable packaging designs and developed group-wide joint material standards for suppliers, including on the recyclability of packaging materials. “Now we are in the process of implementing these findings in new vehicle projects at an early stage,” says Braun.
The carmaker also works with Volkswagen Group Logistics to use more zero or low-emission transport, including emission-free rail for vehicle and material logistics in Europe and the use of ro-ro ships powered by LNG and Hydrotreated Vegetable Oil (HVO100).
By the end of the first quarter of this year, Audi will begin two pilots involving the use of electric trucks with the aim to better understand charging, process and technology requirements and prepare for a potential serial implementation in the next years.
However, to meet interim goals, Audi is committed to ramping up the use of alternative fuels, including HVO100 and biogenic fuels, which have helped Audi to reduce emissions by an estimated 12,000 tonnes per year compared to trucks using diesel. However, the infrastructure and cost basis for such fuels need further expansion, especially in eastern Europe, according to Braun. “We still see a strong need for action here and are already in contact with those responsible,” he says.
Teamwork is dream work for supply chain performance and attractiveness
Whilst advanced digital tools and technology will continue to play a greater role in Audi’s logistics, people remain at the heart of how its supply chain group will create more value for the company, including through creative ideas and partnerships. Dieter Braun wants to ensure that those working in logistics are well equipped to take a holistic approach, and to think critically when solving problems and influencing future decisions.
One key element of that is understanding that the supply chain covers end-to-end processes and is never isolated to any single plant or subset of processes. “Our organisation provides the condition that the overall result counts, not a local result,” he says. “We sensitise our people to have this holistic view and to try understand that every decision in the supply chain can have a big impact.”
That is why Audi’s supply chain team has put more focus on data strategy, information and visibility over order-to-delivery processes, including an emphasis on where AI can help to simulate possibilities and come up with better results.
For Braun, this mindset, combined with digital tools, will help Audi to adapt to further disruptions. He stresses the importance of supporting people in those challenging phases, including through training. It is also important to keep employees clear on their objectives and mission.
For Audi’s supply chain, the vision has become both clearer in creating more value and reducing complexity, but also more urgent in the face of slow growth, rising competition and geopolitical uncertainty. Braun believes this purpose is at the heart of what makes supply chain and logistics an attractive role – especially in such an international context as it is the case at Audi, even in stressful, uncertain times.
“We have such a broad approach with this end-to-end responsibility, making us so much more than just one thing,” he says. “We see the bigger picture, and I think that is very attractive.”
The next article in the series is on Audi’s supply chain organisation and its functions. A further article on its 2033 strategy will be published soon.