Digital democracy for the automotive supply chain
There is a wider demand for and adoption of digital tools and data analytics in supply chain logistics, and with that comes a need for more expertise across the different functions and the placement of core data science teams.
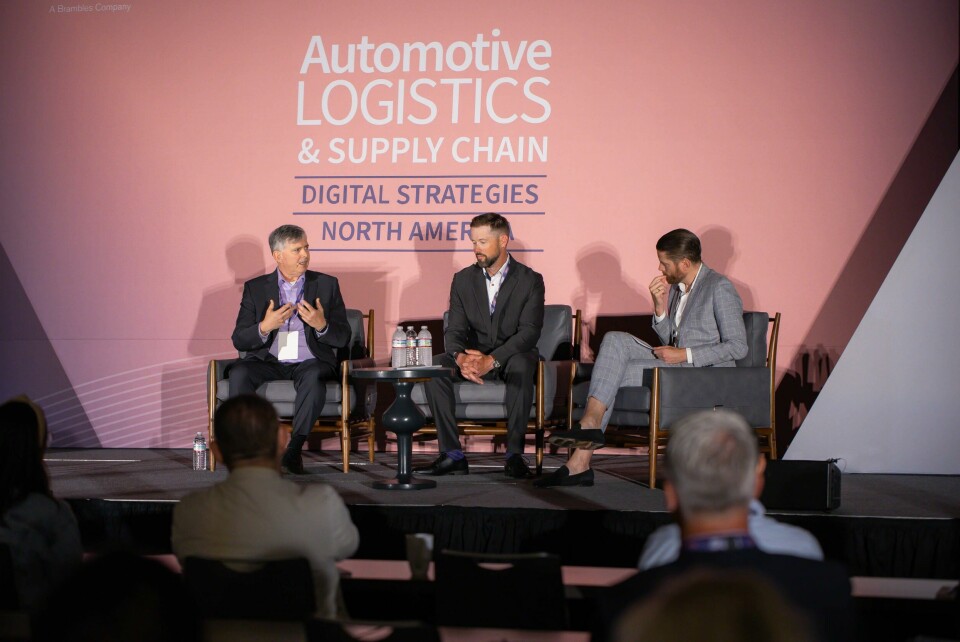
Speaking at last week’s inaugural Automotive Logistics and Supply Chain Digital Strategies North America conference in Nashville, Tennessee, Ed Stachowski, director of data science and machine learning at Ford, said his Supply Chain Analytics department is getting more requests for machine learning (ML) and artificial intelligence (AI) applications.
That greater demand for provide visibility and prepare for risk has been accelerated by the pandemic disruption and the consequent impact on the semiconductor supply chain.
“Supply chain resiliency became really important through the pandemic and the semiconductor issue,” said Stachowski. “What we did there was an interim containment action, but it has to be broader [in future] and you have to sense that risk through the tiers regardless of what the component might be that could cause disruption.”
Greater complexity
The wider adoption of digital tools brings a new layer of complexity as data is sought from across the supply chain and the third-party logistics providers supporting it. For example, there are now a number of examples where digital twin technology is being used in self-contained manufacturing systems but there is more complexity when building a digital supply chain replica that is fed with active data from a variety of sources.
“We have more complexity as we start to look at outside data from third-party vendors and as we start to dive into the tiers,” said Stachowski. “It seems like we have very disparate systems not only in production but in logistics across the different regions, so it is quite complex.”
Scott Sloan, chief architect for the automotive industry at technology infrastructure provider Kyndryl, agreed.
“When you think about the supply chain and you bring up all the external data it is also about the people and processes, which are much broader,” he said. “To have a consistent strategy that is able to bring all that together [means] the levels of complexity are much greater.”
Automation of processes will help manage the complexity, according to Sloan, and he likened the technological transition to the previous move from mass production to mass customisation.
“As we shift the supply chain, being able to provide the sensing and response at a microlevel, and being able to wrap those into the larger logistics moves, it will become more automated,” said Sloan. “Ten years from now we will be looking at systems that we simply assume are going to provide a level of automation that does not exist today. It is much more ‘the human in the loop’.”
Informed decision making
That looped-in human is going to be more empowered as a consequence thanks to a foundation in tools and training, providing those who are currently requesting analytical reports with the ability to generate their own. The democratisation of data has driven a distinct shift in roles, according to Sloan, and more of a focus on business users taking on responsibilities that they would not have previously. That is an organisational change where the boundary between IT and business has been redefined. Users have new tools and with the push into generative AI the adoption of tools for automation is accelerating.
“One of the things we always try to do in this sphere is to push local and [enable] people to make informed decisions,” said Sloan. “That is where we are seeing the initial uptake – being able to supply those people with tools so that they can much more easily make rational decisions based on data.”
Stachowski said that capability was a quick win for the business team and enabled Ford to focus on and identify long term solutions rather continually reacting to things on an ad hoc basis. “It’s about the team doing better and also avoiding the rebuilding of something that is already there,” he said. “We see a lot of duplicate efforts in the organisation and one side of the business may not know that something is being developed. Commonality is key.”
Stachowski added that early data engineering is important for data democracy. “You need to understand what they are calling for in the report and why, and what are they doing with [the data] after, how are they transforming whatever they are pulling out of the cloud.”
Data needs to be coherently aligned across the supply chain so those relying on it for more efficient services can clearly understand what it means for them. Consistency depends on a common operating platform and a common semantic layer, according to Sloan. “You need to be able to build data products consistently [with] an enterprise master data management strategy,” he said. “To provide that metadata and build that semantic layer, is definitely a supportive approach.”
Sloan added that establishing a common semantic layer is the lowest common denominator in the drive toward automated business applications and critical to build an enterprise view. He also said that using language models in procurement is a good example of where coherent data is accelerating decision making.
Instead of driving ad hoc reports from procurement on a monthly basis from which to make a better choice of supplier, carmakers can use large language models to generate reports for themselves. “It is being a support aid to the procurement specialist and helps them makes concrete decisions every day,” said Sloan.
Ultimately digital technology is being more widely adopted to manage risk and build resiliency. Stachowski said that at the earliest part of the sourcing process Ford is already building models to predict risk to avoid disruption to inbound freight and resort to premium freight services. The carmaker is using prediction models and ML to assess risk to suppliers and identify priorities for further action or changes that need to be made in the supply chain.