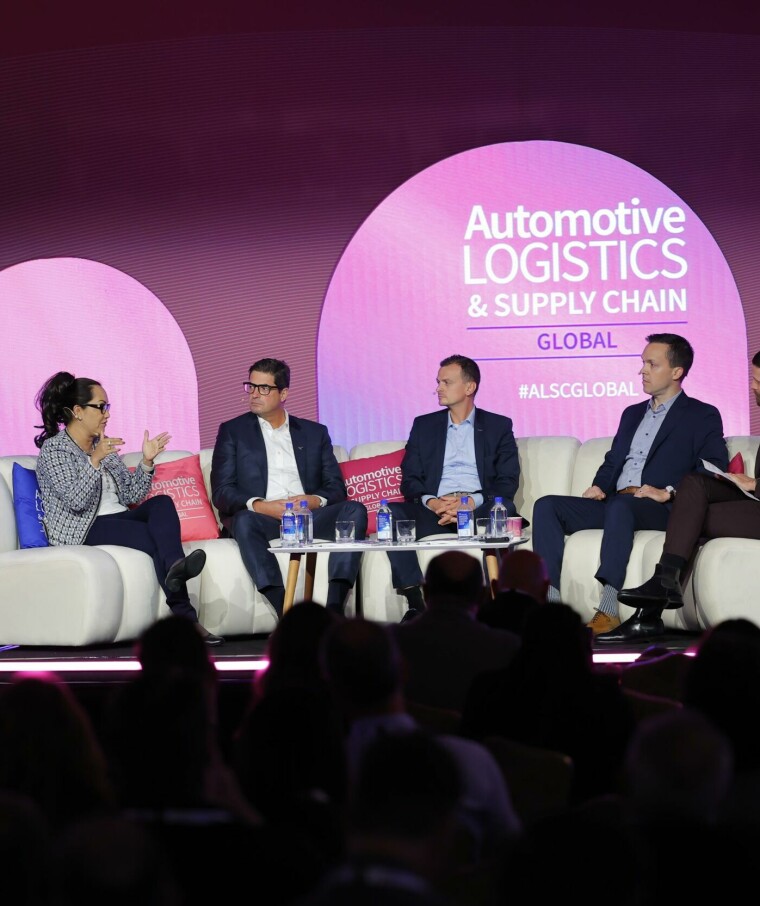
The latest insights from Automotive Logistics & Supply Chain Global 2024
Hello everyone and welcome to the Automotive Logistics and Supply Chain Global 2024 recap blog, from our event which took place on 24-26th September at the Henry Hotel in Dearborn, Michigan. Stay tuned to get the latest updates and insights on our conference speakers and the sessions here!
October 3
Jeff Morrison, senior vice president, global purchasing and supply chain at General Motors took to the Red Sofa to discuss how the OEM is deepening its partnerships with suppliers.
Watch the full video below now.
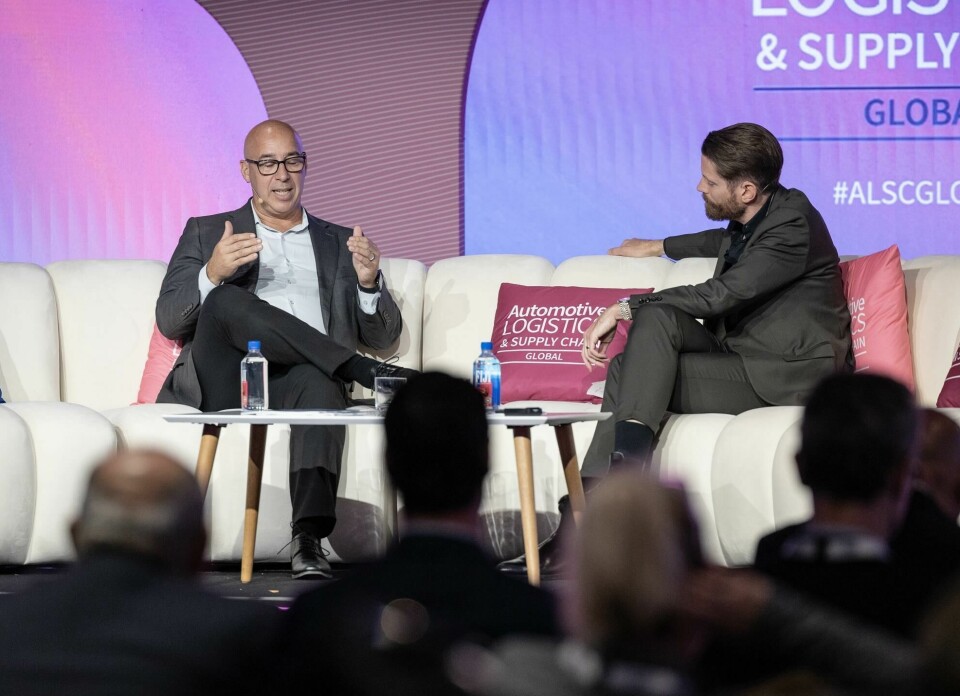
October 1
GM relationships with suppliers and partners based on preference
In the final session of the conference Jeff Morrison, senior vice president, global purchasing and supply chain at General Motors, joined Chris Ludwig for a fireside chat about the supply chain lessons learned post-Covid and what GM is now looking for from a logistics perspective to support the transformation to battery electric vehicles (BEVs). That includes a preference for anchor customers when allocating capacity.
Morrison explained that the Covid pandemic had disruptive repercussions for the supply chain that drove GM to look for more transparency in the supply chain and a greater understanding of where its tier-n suppliers were located. With that GM worked on better management the suppliers further along the supply chain and Morrison said it has become more creative in managing supply chain disruptions, notably the consequent shortage of semiconductors.
“We were able to take the learnings [from Covid] and apply them to focusing on semiconductors and specifically how do we flex the capacity… and apply it to the right products and the right modules so that we can build an optimum mix for some period of time from a logistics standpoint,” said Morrison.
Closer management of the supply chain to avoid disruptive gluts in production results in steady flow of vehicles to market, which is honey for the supply chain, according to Morrison. Now it is looking at how to industrialise and scale future technologies, including for electric and autonomous, software defined vehicles.
“It has been a crazy time but as we sit here today, it feels like we finally have some momentum behind us and that these issues we had in the past are largely gone,” said Morrison. “We’ve been successful building out in parallel all these great things that we need to be focused on for the future. We’ve strengthened relationships with suppliers and partners, and I think we’ve realized the importance and how critical it is that we have great relationships, not only with our direct suppliers but the key suppliers in the value chain.”
Morrison said that GM realised very quickly that the semiconductor manufacturers valued hearing directly from GM because it gave an unfiltered view of what we see automotive doing and what that demand looks like.
A good example of the resulting strength in supply is the direct agreement GM signed with chip supplier GlobalFoundries in 2023 for the long-term guaranteed supply of semiconductors, establishing what it “a dedicated capacity corridor exclusively for GM’s chip supply”.
Morrison said that the difference in supply chain communication and engagement between three years ago and what it is now is the difference between night and day. Supplier relationships are strong and GM has fully mapped out its products and is actively managing the supply chain behind them.
That includes electric vehicles (EVs) and the batteries powering them.
“As you look at batteries, the critical minerals and battery raw materials that feed into it, we recognise how there is a scarcity and there is a need to build capacity, and we know that we need a partner to do that,” noted Morrison.
He said that GM was now evaluating its strategic supplier relationships, including logistics providers, and whether it is running them in a more transactional way. GM has now spent a lot of time looking at some of the critical partnerships and strengthening them by moving from short-term transactional agreements with ones that are longer term, more strategic and more secure.
“That is kind of a win-win for both and I think that will continue to be important in a lot of areas, and that’s an area that we definitely want to continue with,” said Morrison.
However, Morrison also had a warning for logistics providers and said they need to give GM the preference he feels the carmaker has earned. That is especially the case in terms of capacity at the ports and logistics services, given the new competition for capacity, including from Chinese carmakers in Mexico. That included for finished vehicle movements, to which Morrison appealed to providers of finished vehicle logistics:
“When you think about new entrants that are coming in, whether it’s here in the US, Mexico or around the world, as you’re allocating capacity out, please do not forget your anchor partners,” he said. “[It could be] port congestion for vehicles in Mexico, because we’ve got new entrants that are coming in and basically using what should be VDCs in a port as storage locations [which is] impeding us as big anchor customers in there. Please give us the preference that I think we have earned over this amount of time and I promise you, if you don’t give us that preference, we will probably not forget that either.”
Morrison said that logistics out of Mexico had improved but there are still challenges in moving vehicles and materials northbound across the border with the US. Strategic relationships and contracts are again an important factor in securing the capacity required.
“The other thing that we did is put a spotlight on some of the block and tackle operational things,” said Morrison. “We need to look at managing with excellence and trying to minimise as much waste as we can, and get maximum utilisation out of the assets that we do have at our disposal to move things right.”
Morrison said that GM had “found a ton” of operational opportunity that the teams have been able to focus on.
“As we sit here today, we have much sharper operational performance, better partnership at all levels, and strategic agreements that really kind of set ourselves up for success here as we go forward to work together,” he said.
Morrison also spoke about reinventing logistics for EVs, especially for finished vehicle movements. The transformation to battery EV (BEV) production has disrupted the traditional incremental changes to production and supply that preceded it and that brings with it complexity that has a higher cost. Logistics will have to play its role in helping to make BEVs more affordable. For inbound material that includes identifying whether material shipments are being cubed as optimally as possible, is the container size optimal, is there a better mode of conveyance, and where can logistics partners help with more efficient consolidation and deconsolidation.
In terms of the movement of finished BEVs, GM is going to have to review the transport mode given the restrictions on weight for loaded road haulage equipment, which can reduce the number of vehicles per transporter unit from between eight and ten to three or four. Going forward that is not going to be efficient and Morrison said rail is a very efficient way of transporting vehicles from the assembly plants to market.
“We to be aggressive about what that looks like and how we do that as the right business case,” he said.
That could translate as greater support from GM for investment in new equipment.
September 28
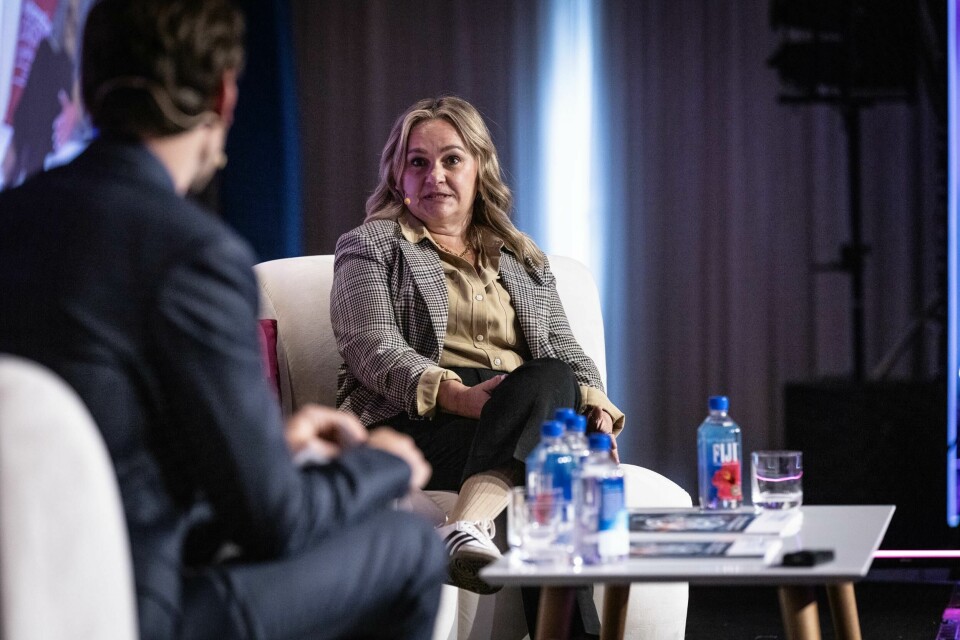
Collaboration on data is crucial for a resilient supply chain
As the automotive supply chain becomes more complex, building resiliency to mitigate disruption becomes even more important. Risk management experts from American Axle and Manufacturing (AAM), RXO and supply chain software provider Avetta used this week’s ALSC Global conference to redefine what resiliency means and what needs to be done to maintain supply chain flexibility as the needs of the market change.
The panel agreed that resiliency mean the ability to recover and get things back to normal. RXO’s senior vice-president Dennis McCaffrey said that depended in good preparation and the ability to foresee potential disruption.
That has become more difficult given the pace of change in the automotive industry and geopolitical or climate problems around every corner. The answer is closer collaboration and shared learning with supply chain partners and customers, and investment in the latest software. Ana Lucia Ochoa Lorenzini, global director supply chain management in the Metal Forming division of AAM, said these were two principal things to consider when managing network volatility
“We have been developing a lot of tools internally and we work in risk management,” she said. “We have also been participating with the OEMs and have set up steering committees with a lot of our partners and other tier companies. That allow us to be better prepared for what is happening [because we are learning] from their experiences, we’re learning from each other.”
Digital tools are helping in that more collaborative approach to risk management and Birdo Richards, vice-president of global sales for Avetta said that support was helping managers cope with an increasingly cross-functional role.
“What we do is we help people qualify, manage and monitor their suppliers and contractors on an ongoing basis,” he said. Avetta has moved on from helping large organisations focus on safety and procurement because supply chain and logistics managers are being asked to do more to maintain flexibility and curtail disruption to the inbound flow of parts and materials.
“They’re being asked to know about different regulations and different components, and with the global interconnected supply chain we have today, there are also impacts way further down the supply chain,” he said. “If they miss some of their pieces, they could cause disruptions down the line for their team members or even their customers. So it’s important for us to really plan ahead and be proactive.”
The automotive industry has traditionally been ahead of the curve on being proactive, according to RXO’s McCaffrey. That is because of its long-held just-in-time delivery model of production. “Supply chains require you to be able to react and adapt quickly because you don’t have a lot of safety stocks,” he said.
Using expedited services is reactive by nature and RXO began as an expediter for the automotive industry but McCaffrey said company has grown to a $6 billion transport broker and freight forwarder over the last 30+ years with hundreds of thousands of carriers and 12 different service offerings. That organisation calls for proactive planning to make the network resilient.
As automotive and manufacturing sectors prepare contingencies to cope with the potential longshoreman strike that could hit ports up and down the US east coast next month McCaffrey referred back to the very short-lived Canadian rail strike in August.
“We had six months of planning with an OEM leading up to that and part of that is having a really strong relationship,” he said, adding that having playbook from prior events and a continuous improvement process in place was very valuable. “
A post-mortem strategy to disruptive events better equips you for the future, according to McCaffrey.
According to Birdo Richards there has been a major proactive shift from looking at lagging indicators to looking at leading indicators, and that information is fed into the latest AI tools to support predictive analytics. Avetta helps customers assess subcontractors on payment history, timeliness or quality of operations. “ We look at what can we do to predict who is going to have the most risk to our supply chain and also who’s going to impact something downstream?,” said Richards. “As we see with many industries,[automotive] is really starting to move more to a how can we predict what’s going to happen and use leading indicators rather than just looking at past results to identify that risk.
What is also important for AAM is building buffer capacity and diversifying into underutilised regions for dual sourcing. “We are building our tools based on what we have learned from previous situations and that’s what we’re implementing right now to be better prepared and build the right amount of stock in the right places,” said Ochoa.
September 28
Managing talent to drive supply chain excellence
Students from Michigan State University, Wayne State University and Northwood University are joining a workshop on managing talent to drive supply chain excellence, with a panel led by Daniel Schwartz, director of Global Distribution Operations, Service, Rivian; Adam Olson, vice-president, Logistics Mobility Americas, Bosch; and Julie Luna, chief commercial officer, North American Rail and Intermodal, Jack Cooper.
With all three panelists working in very different organisations, in terms of structure and size, each of them have unique talent needs.
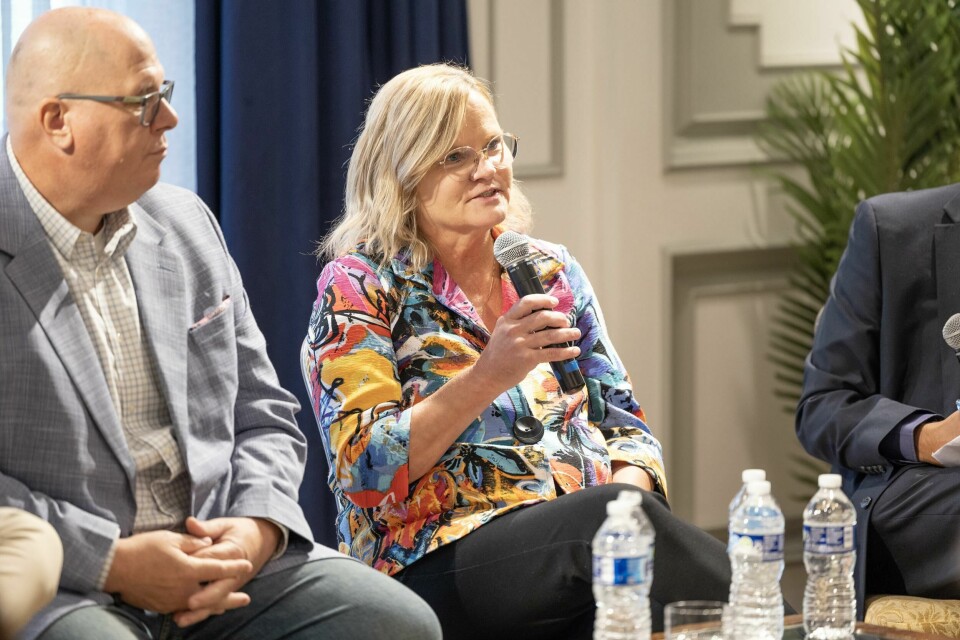
Jack Cooper, which is family-owned and women-owned, has the benefit of speedy reactions. “Our business is much faster to react, you don’t have as much bureaucracy,” Luna says. “You’ve got one woman who owns 51% of the company and she’ll always take your call if you need anything. It attracts talent differently and you’ve got to be comfortable with the family dynamic, but it’s also one that’s been very fun.”
Bosch’s Olson says that despite being a worldwide company “where it sounds like you could get lost in the weeds”, you can make your own pathway due to the vast resources at a larger firm. “There are lots of different development opportunities so you can flourish in a lot of different ways,” he says.
Schwartz says that Rivian, as a start-up, is fast-paced and needs talent that can manage that. “In logistics and supply chain the pace is fast, it’s exciting working in this industry because challenges are popping up everyday and you have to react to that, but in Rivian times that pace by ten,” he says. Schwartz says the company has a bootstrap mentality due to its age. “Four years ago, we didn’t have many processes or systems, we were a tiny team. Now we have hundreds of people, building distribution networks and full supply chains,” he says. “What drives our needs is this reality that we move at an expedited pace and we’re building from a foundation to a more mature organisation.”
In hiring and retention, all three panelists agree that culture and mindset is a factor in attracting new talent to their companies. Rivian’s Schwartz says that the company’s focus is more about attracting talent with the right mindset and fast pace, rather than attempting to find the “perfect” candidate. “Almost every single person on my team had zero automotive experience,” he says. “We open the door a bit more broadly to bring people in.”
September 26
“Customers need to be prioritised” - Heather Latham
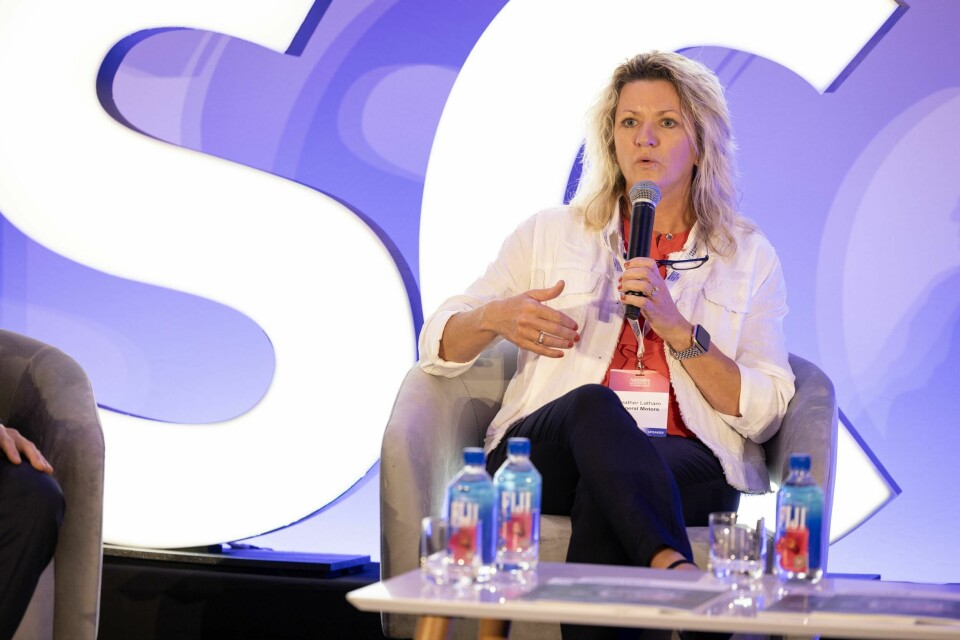
The automotive industry is transforming its service parts supply chains to meet evolving customer demands, particularly as electric vehicles (EVs) rise in prominence and consumers hold on to their vehicles longer. Heather Latham, director of supplier management, customer care and aftersales at GM, highlighted that while keeping assembly lines running remains crucial, the industry must equally prioritise customers. “It’s not an either/or; it’s an ‘and’. The customer must be at the centre,” Latham emphasised.
Alfonso Rodriguez, senior director of supply chain planning and commodity purchasing at Zero Motorcycles agreed, stressing the need to maintain service excellence even as EVs require fewer repairs. “Our CEO has made it clear that service care is a priority, if your brand reputation takes a hit early – as we consider ourselves a start up in maturity – it’s hard to recover,” he said.
Christiane Meyer of Penske Logistics highlighted the need for adaptable systems and increased precision in service part distribution. “We have to be on our feet constantly,” she explained, underscoring the complexity of balancing customer demands with operational realities.
The shift towards customer-centric models is reflected in faster part deliveries and more robust supply chains. Both GM and Zero Motorcycles are committed to reducing order times, with Rodriguez commenting that Zero Motorcycles is aiming to replace parts within 48 hours. The future of service parts logistics is tied to efficiency and reliability, making it a key competitive differentiator.
September 26
How GM boosts resiliency through predictive AI
It’s day two of ALSC Global 2024! After a relaxing boat ride on the Detroit Princess last night, hosted by Ryder, we are ready to hear more from the logistics experts on stage today about the not-so-smooth sailing the industry is experiencing.
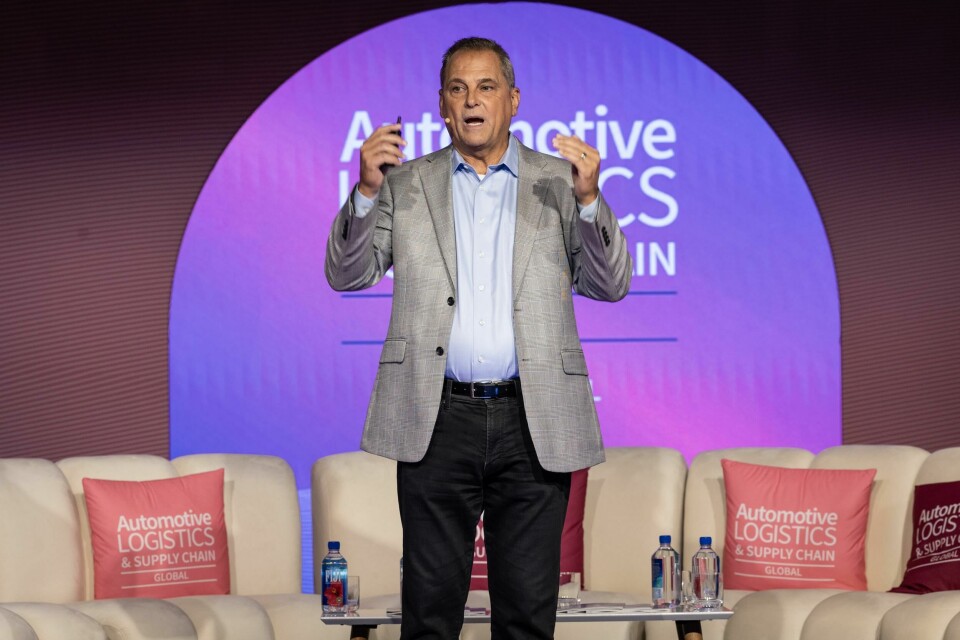
In the first session of the day we’re hearing from David Leich, executive director, Global Supply Chain at GM; Marzell Bandur, vice-president of Transport Management & IT Innovations, Bosch; Salim Shaikh, chief vice-president, Industry Strategy Automotive, Blue Yonder; and David Resetar, senior vice-president, Global Head of Vertical Market Automotive, DB Schenker.
When discussing the roadmap for connected and predictive supply chains, GM’s Leich says that the OEM is using a variety of technologies, from supply chain mapping to real time event monitoring, AI, and something GM has been working on for several years which it calls the ‘Supplier Home Dashboard’.
“We use this machine learning tool to give us the parameters of what are the highest risk suppliers that we should be concerned about in a proactive way,” Leich says. So if suppliers that are trending negatively based on a whole bunch of interesting analytics that we use with machine learning, we can see real time risk ratings for every supplier. And that gives our team the top suppliers that we should be engaging with proactively to make sure that they can put actions in place to mitigate issues before something becomes a bigger issue.”
September 26
Welcome to day 2!
Welcome to the second day of sessions at the Automotive Logistics and Supply Chain Global 2024 from the Henry Hotel in Dearborn, Michigan.
After an action packed day full of insights and key discussions on the logistics and FVL industry yesterday, the night ended with our 750 speakers, partners, and delegates setting sail on the Detroit Princess Riverboat for a Networking Dinner hosted by our Premier Partner Ryder System, Inc.
Today, we will see leaders from GM, Nissan, Rivian, Bosch, American Axle & Manufacturing, Jack Cooper and many more discuss the trends, challenges and potential solutions in supply chain, automation, logistics and next gen talent.
Stay tuned for more live updates from the event!
September 25
Timely and open communication during crisis with Nissan, VW, ProTrans and Ascent Global Logistics
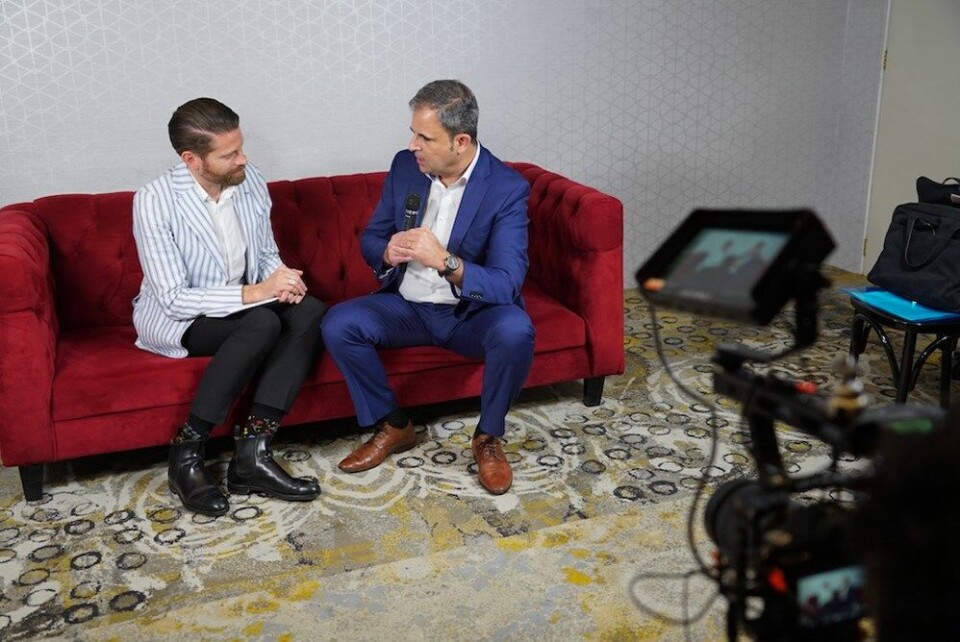
In our final session of day one, we are discussing how to master supply chain complexity with a keynote from Paulo Monteiro, head of Logistics, Volkswagen Group of America Chattanooga Operations, followed by a panel where he joins Gerardo de la Torre, regional senior director, Supply Chain Management (SCM) US & MEX, Nissan Group of North America; Daryl Knight, chief commercial officer, ProTrans; and Micah Holst, executive vice-president of Business Development, Ascent Global Logistics.
The panel is discussing the importance of timely and open communication across the supply chain, particularly in times of crisis – something that we’ve heard repeated throughout today’s panel sessions.
At Volkswagen’s Chattanooga plant, flexibility in production is a key strength, allowing the company to adapt to various challenges. “We can produce both petrol and electric vehicles on the same assembly line, offering the ability to shift production based on current needs,” says Monteiro.
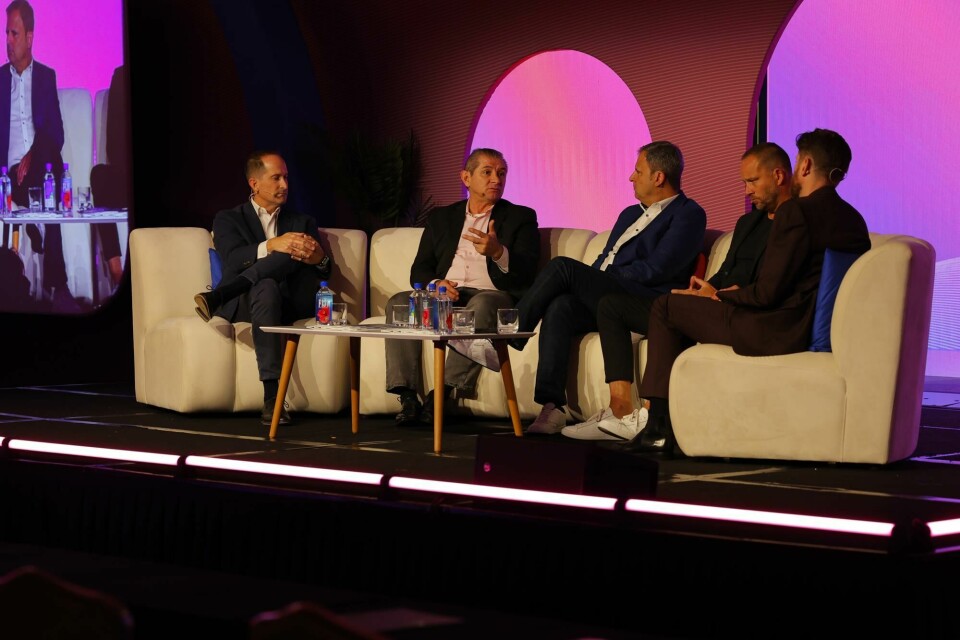
“This flexibility is further enhanced by our multiple commodities sourcing strategy, which enables the same product models to be produced in various locations. For example, the Atlas model produced in the US can also be produced in China, with only minor differences.”
Knight adds flexibility needs to be defined in alignment across the supply chain. “Defining what flexibility means allows you to actually deliver upon that,” he says. “What does it really mean in practical reality when you have to execute against that.
Nissan’s De la Torre says that having invested more than two years in creating digital tools with partners in the supply chain network, the flow and exchange of information and data is allowing the OEM to be more predictive and efficient.
He says that what the carmaker calls “internal Nissan data” is made up of data from inside Nissan’s operations but also includes supplier delivery performance, expediting costs, quality issues with the suppliers and more.
“We call that ‘Nissan internal data’, but it is together with what is external data,” he says. “We are taking the best of both, sourcing data for initial alerts and predictive alerts.”
September 25
”There’s a continued mismatch between capacity and demand due to volatility in production” – RPM’s Sean Baltazar
Improving finished vehicle logistics (FVL) is crucial for carmakers seeking to enhance efficiency, quality and delivery. A panel of experts from Ford, Celonis, RPM and Cognosos emphasised the importance of leveraging data and technology for optimal results.
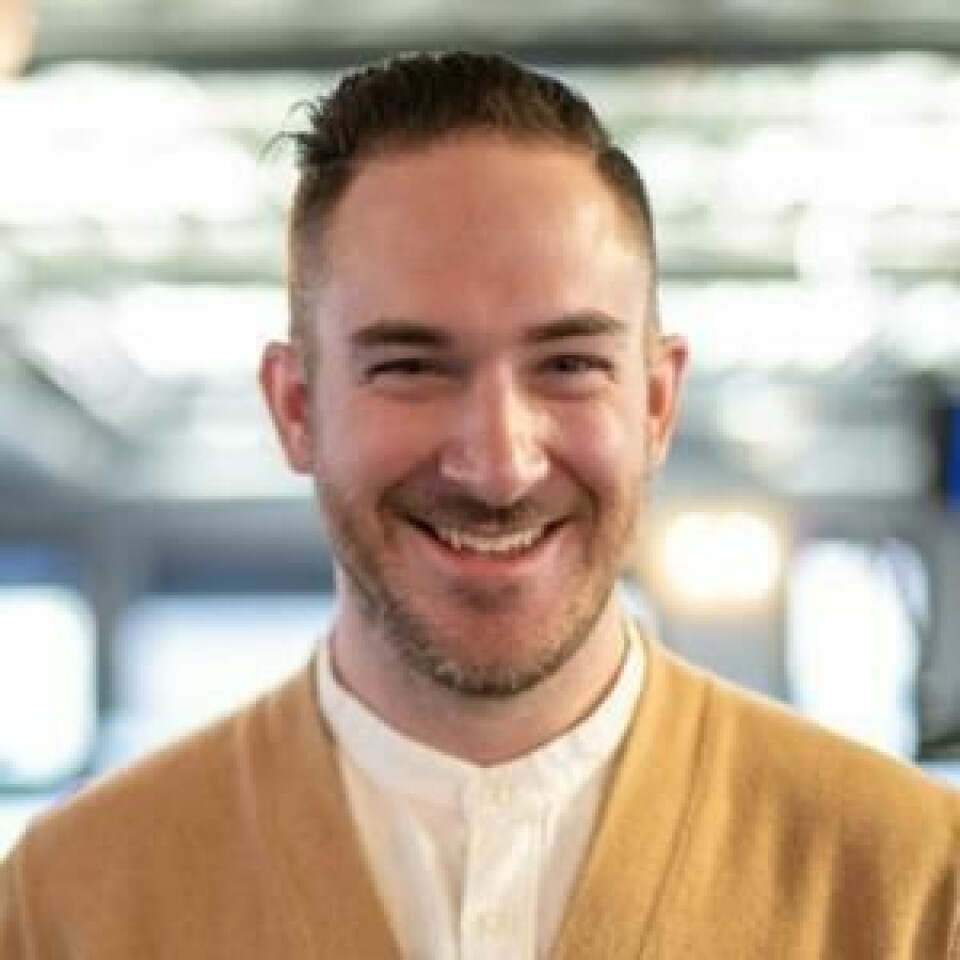
Sean Baltazar, senior vice-president of sales from RPM highlighted that the past two years have intensified supply chain challenges, noting, “There’s a continued mismatch between capacity and demand due to volatility in production.” For transportation providers, timely and accurate data is key to tackling these inefficiencies.
Global automotive and manufacturing industry lead, Julian Thomßen at Celonis discussed the benefits of digital twins and data integration, which provide an end-to-end view of vehicle logistics. “Customers are really looking for the end-to-end picture,” he said, adding how generative AI could further support this transformation by analysing complex business processes.
Anthony Butler, director of product, logistics at Cognosos stressed localised solutions, saying, “We focus on reducing search times and improving operational efficiency by streamlining vehicle tracking systems.”
Ford’s senior director, supply chain analytics, Oleg Gusikin, elaborated on the company’s digital transformation and data approach: “We’re building an end-to-end digital twin, combining data across the supply chain to optimise systems-level performance.” This comprehensive data strategy, integrated with advanced analytics, enables Ford to optimise logistics operations holistically he emphasised.
Collaboration across departments and partners, along with data transparency and trust, remains key to addressing inefficiencies and driving progress in FVL operations.
September 25
Red Sofa interview with Jessica Hanson, Bosch North America
In the first of our ALSC Global 2024 series of Red Sofa Interviews, brought in partnership with Unipart, we sat down with Jessica Hanson, vice-president of Logistics, Bosch North America. She spoke to Christopher Ludwig, chief content officer, Automotive Logistics about investing in contingency plans, partnerships and new technologies to stay flexible and innovative.
Watch the Red Sofa now.
September 25
Need of the hour: AI-based risk scanning and flexible, collaborative supply chain management
Automotive supply chains face unprecedented pressures, but collaboration and data-driven strategies offer hope, as industry leaders shared during the panel discussion, “Top tier logistics: managing excellence in end-to-end automotive supply chains”. Mike Tickle, director of supply chain planning and performance at JLR, emphasised the need for “AI-based risk scanning” and flexible, collaborative supply chain management. He stressed the importance of strategic partnerships to align supply and demand planning more effectively, particularly given the lasting challenges posed by the semiconductor shortages.
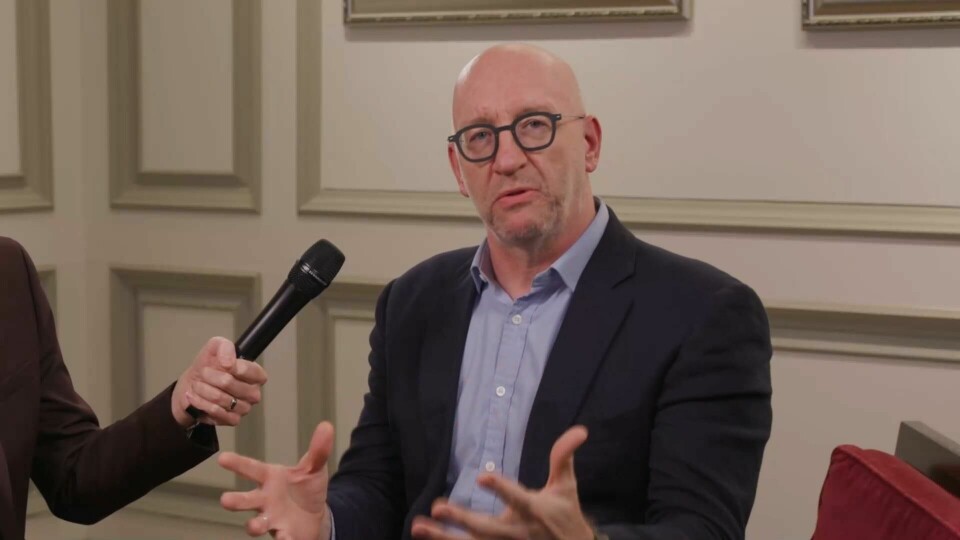
Patrick Bauer, vice-president supply chain at IAC Group, highlighted the lingering effects of Covid-19 and how mismatches between forecasts and actual demand, especially for electric vehicles have left inventories bloated. “We need to collaborate better with our partners to manage the entire supply chain,” Bauer remarked.
Tom Regan, senior vice president at Ryder Systems, noted that scaling capacity up is often easier than scaling down, and integrating AI tools could improve planning accuracy. However, he cautioned that without solid data, “it will all die on the shop floor.”
Mike Erickson, president of AFMS, echoed the need for deeper collaboration, particularly in logistics. “The 3PL relationships have expanded… almost every company is using them,” he said.
Enhanced data sharing and trust were recurring themes, as all speakers agreed on the need for closer partnerships to mitigate supply chain volatility.
25th September
“Negative public image can lose customers for life,” warns Ford’s Benjamin Pohl
After lunch, we’re joining Benjamin Pohl, supervisor, Vehicle Shipping Quality, Claims and Damage Prevention, Ford Motor Company for a workshop on damage prevention in finished vehicle logistics.
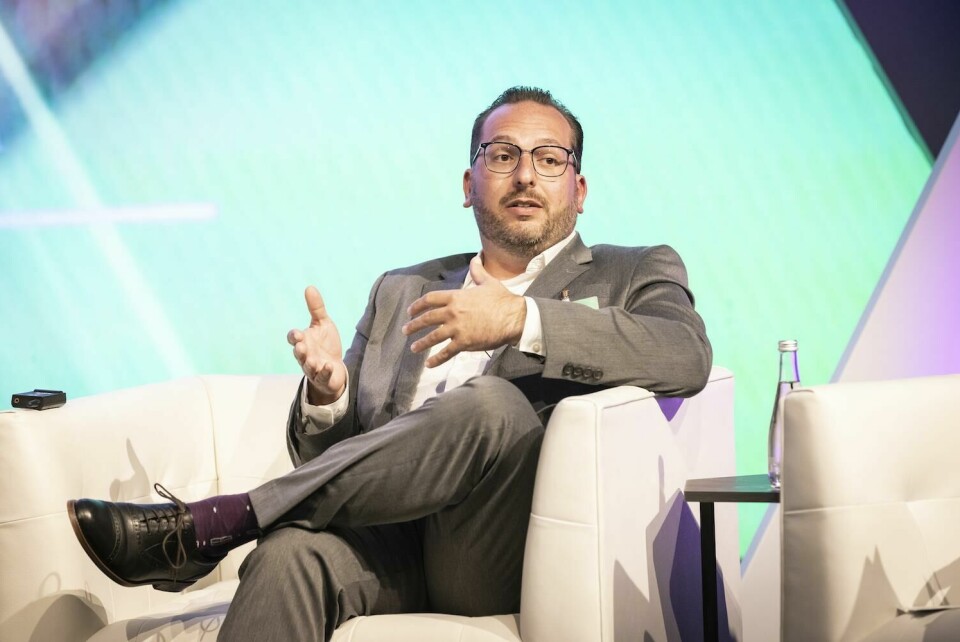
Pohl says that damage prevention is crucial not only to keep deliveries on time and customer satisfaction high, but also to prevent loss of finances. He says that while losses can be incurred from needing to repair or scrap vehicles, another risk to cost is growing.
He explains that the rise of social media in capturing FVL accidents, such as hitting a bridge or tunnel, can have a huge influence on business. “It’s the power of social media and how it spreads so quickly,” Pohl says. “The carrier hasn’t even told me about the incident, but I can see it on social media, because it’s moving faster than we can handle.”
Having a negative public image of who you are hiring to ship your product can lose customers for life, he says.
To mitigate this, it’s important to discuss and define what quality is with your supply chain network and ensure you’re aligned. “You’re never going to get to 100% damage free FVL, but we can fight to get really close,” he says.
September 25
“You’re looking at a 50% reduction in capacity soon” – Nissan’s Todd Myers
In the first session dedicated to finished vehicle logistics at this week’s conference speakers from Nissan, Glovis America, D-Troy and Michigan State University discussed the pressures the shift to electric vehicles (EVs) was putting on vehicle logistics across the transport modes, and what the sector needed to do to make road and rail transport as clean the EVs being moved.
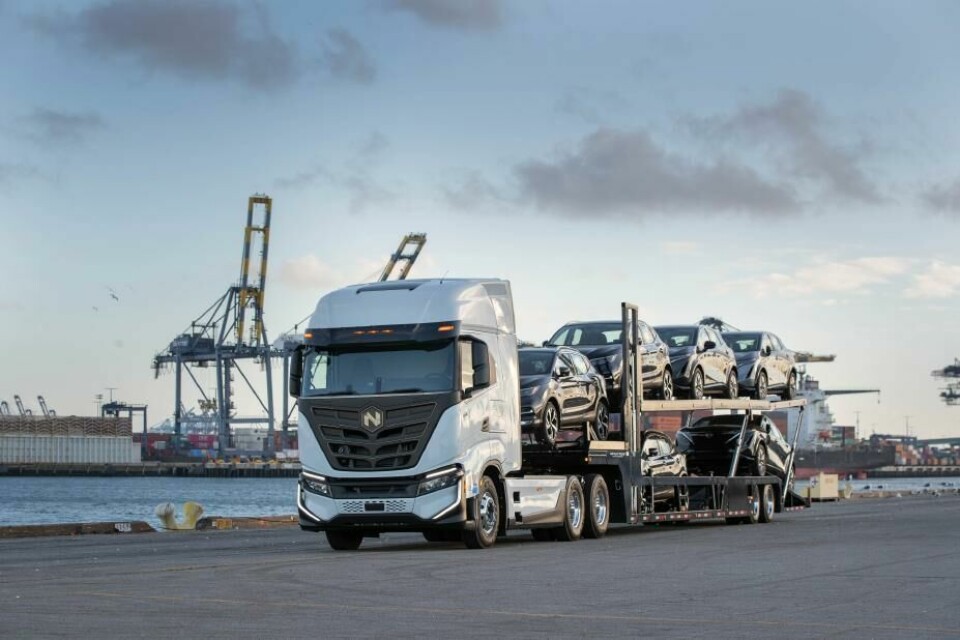
Todd Myers, director of finished vehicle logistics at Nissan North America said the biggest impact is going to be on road-based haulaway, with each transporter unit losing anywhere between two to five vehicles because of the added weight of the EV battery and the trend to larger SUVs and pickups. Vehicle carrying trucks in the US have a loaded-weight limitation of 80,000lbs (36 tons), something made further problematic once transport companies adopt electric trucks, which will be significantly heavier, again because of the battery.
Myers said that the road-haulage sector will have to look at working with vehicle manufacturers and sharing available transport capacity, organising a system similar to the rail car pooling management offered by TTX. Myers said that meant getting around antitrust and privacy legislation but the capacity shortfall is going to be exacerbated by a truck driver demographic that is not being renewed as older drivers retire.
“You’re automatically looking at a reduction in capacity of 50% plus, so it’s a big problem and it’s coming soon,” warned Myers. “As soon as the market starts pulling in the EVs at a greater rate [the problem] is really going to surface.”
Charles Franklin, senior national manager of business development at Glovis America described some of battery EVs coming market as “beasts” and echoed Myers’ concerns over transport capacity.
“There are some vehicles coming out in the near future that are 10,000 pounds each,” said Franklin. “You’re going to suck up all of the capacity of a truck with just two or three vehicles in some instances, trucks that could have carried nine [sedans] back in the old days of [combustion-engine] vehicles.”
That in turn will have a huge impact on the cost of shipment, added Franklin. He said what is important for the future is to include vehicle engineering teams in pre-production discussions with logistics experts to ascertain whether the vehicle planned is actually able to be shipped efficiently. In relation to battery EVs, considerations also need to be made for the charge on international shipments, such as a program that enables to car to sleep on long journeys.
Franklin also pointed out that the technology in EVs needed to support the streaming of vehicle data (or reflashing) that allows better traceability and identification at the ports.
“We have got to get more technology to allow the streaming of data to these vehicles,” said Franklin. “It doesn’t make sense for you to have 4,000-5,000 vehicles at a port that someone has to physically touch. Beachfront property is expensive and you got your vehicle stuck there.”
Agustin Sustaina, chief commercial officer, at D-Troy, which offers dedicated finished vehicle door-to-door transport services between the US and Mexico, also pointed to the training for drivers and operational crews that is needed for moving battery EVs by road. Sustaina said managing battery EVs in transit is different to traditional combustion-engine vehicles.
In terms of traceability and more accurate tracking, rail is beginning to benefit from a new service called RailPulse, which Val Kucherenko, director railway education at Michigan State University’s Center for Railway Research & Education, said heralded a “revolution”.
The RailPulse technology platform provides real-time railcar data via GPS and other telemetry sensors installed on railcars that feed data to a platform on railcar location and condition to help shippers, lessors and railroads optimise fleet performance, visibility and safety to keep freight moving.
“In the rail industry, visibility has been a challenge but its actually changing,” said Kucherenko “[RailPulse] is transforming the approach to visibility when it comes to railways and the commodities shipped inside the rail cars.”
He explained that RailPulse is promoting the attachment of the sensors on rail cars enabling stakeholders including OEMs to see what is going on with railcars and where they are at any one time.
“As of today, I believe they operate or control 7,000 rail cars, a small fraction of the total railcars being used in North America, but with time it will definitely change the industry.”
September 25
Breaking barriers with women in automotive logistics!
We’re now talking about breaking down barriers to attract and promote more women in the industry, with Viriana Columbia, head of Automotive Vertical, North America, Maersk; Mary Helen Montalvo, director of NA Business Development, Tri-National; and Skotti Fietsam, senior vice-president, Supply Chain, Accuride.
Despite improving in recent years, there are still challenges present for women in the automotive logistics and supply chain sector. Maersk’s Columbia says: “Women are still significantly underrepresented in the business, there’s still unconscious biases which influence hiring opportunities for women, and work life balance is still a challenge, as in this industry you work very long hours with lots of travel going on.”
To overcome these obstacles, Columbia says you must challenge your company to provide more options and flexibility. “You have to challenge your work environment to come up with ways to help women have that work life balance, maybe working three days a week or doing your 40 hours in four days, having those options to help motivate women to want to go into leadership roles.”
Fietsam and Montalvo both agree, and say it is important to take on the responsibility of making change yourself. “If your company doesn’t have a DEI programme, then you start one,” says Fietsam.
Viriana adds: “Start connecting with mentors in the industry that are involved in DEI groups and ask what they are doing and what programmes they have available. Then start building a business case to bring to your leadership team. Start small, test it, prove it and then from there, make it bigger.”
September 25
“The Panama Canal remains a choke point,” Skotti Fietsam, Accuride
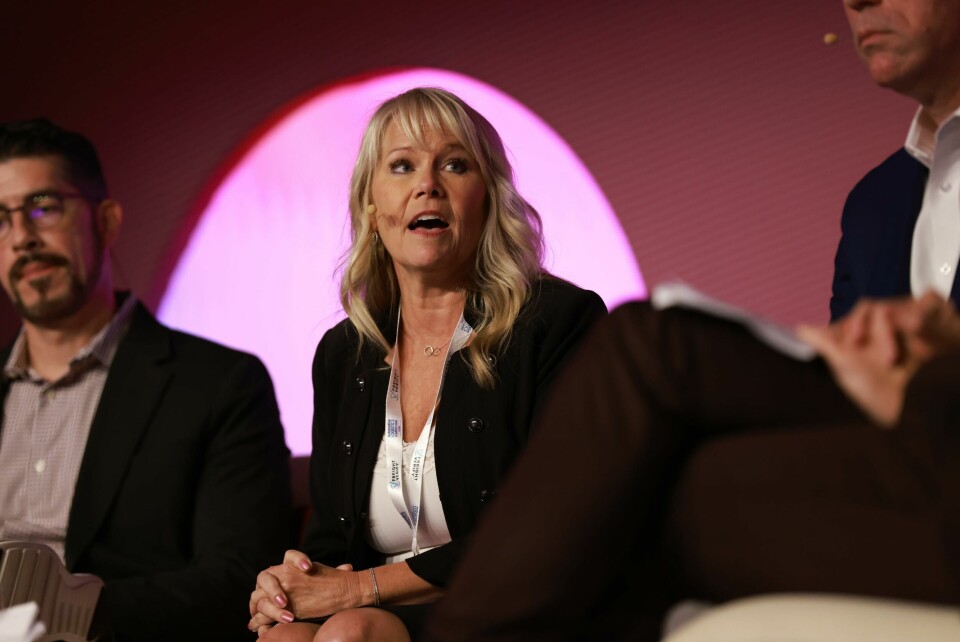
Cross-border logistics in North America continues to face significant challenges, as highlighted by industry experts during the panel discussion, “Borderline brilliance: creating seamless international parts flows”. Jessica Hanson, vice-president of logistics at Bosch, pointed to recurring issues at the Mexico border, labelling it a “yellow zone” due to regulatory constraints and security risks. In contrast, she noted that Canada remains stable with minimal disruptions, primarily driven by regulatory changes.
Skotti Fietsam, senior vice-president supply chain at Accuride, expressed concerns over upcoming strikes, particularly on the US east coast, while also flagging congestion on the west coast due to diverted traffic.
“We’ve had to divert from the Red Sea, and the Panama Canal remains a choke point,” she said, underscoring the global nature of these disruptions.
Frank Bateman, vice-president supply chain at Ryder Supply Chain Solutions, emphasised the importance of better coordination between federal and state governments to handle issues like migration more efficiently. “We need federal and state governments to work in conjunction, not in silos,” he stated.
Sean Leary, general manager automotive and mobility at DSV, highlighted the potential shift to air freight to alleviate congestion but noted that capacity constraints remain a looming challenge.
The panel agreed on the necessity of investing in infrastructure, with Hansen advocating for greater contingency planning, including route diversification and inventory optimisation. “You need to maintain collaboration with your supply chain partners,” she stressed, underscoring the critical need for real-time visibility and proactive management to navigate these disruptions effectively.
September 25
‘Untangling digital spaghetti’ with Kiki Nice, Detroit Diesel Daimler Truck North America
As this is our biggest conference ever, we have now split across three different streams. Kiki Nice, manager of Supply Chain, Detroit Diesel Daimler Truck North America is leading an interactive session called ‘Untangling digital spaghetti’ which is focused on bringing stakeholders together to exchange and work together on common challenges in connecting logistics systems and tools, and sharing common solutions that will help logistics managers make significant strikes in digital transformation.
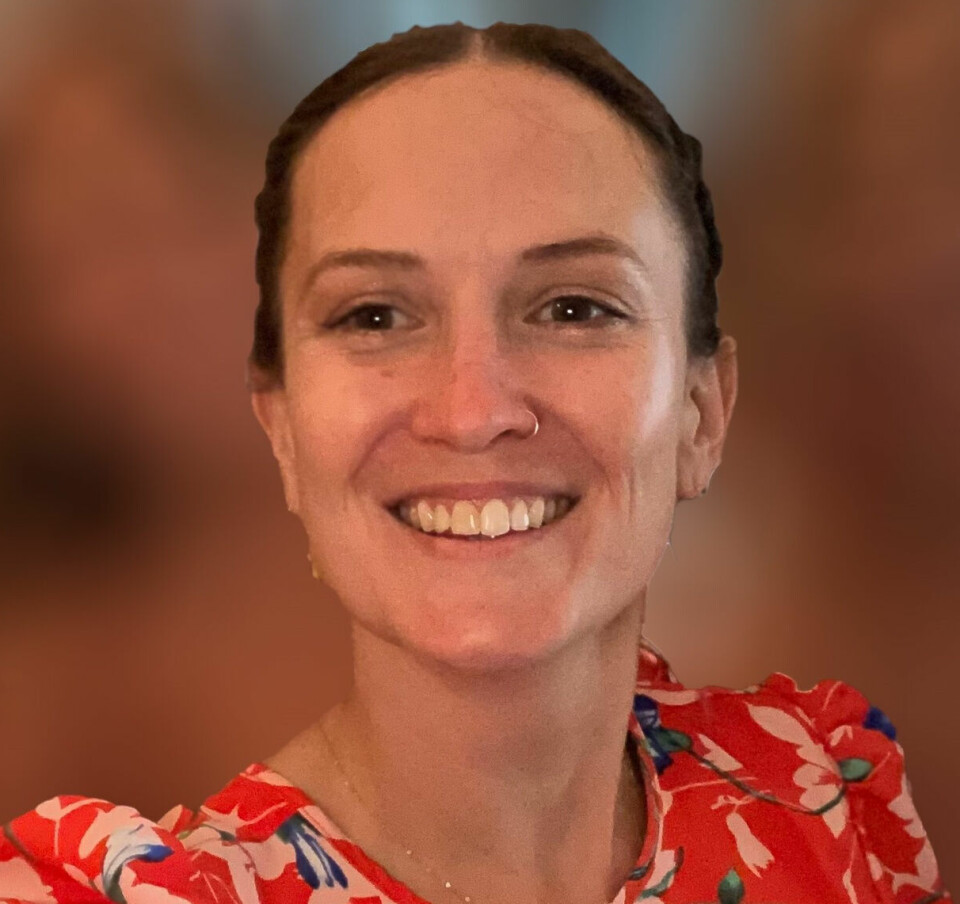
Within the session, the delegates are being split into groups to discuss their challenges and participate in peer consulting. One group’s challenge is that there is a lack of integrated systems leading to a lack of visibility, particularly in the logistics sector where there has been a trend of acquisitions over time - a recent example of this being DSV’s acquisition of DB Schenker.
Regional preferences for certain systems can cause issues related to internal consensus, which can cause a lack of visibility to the inbound supply chain. Variance in external service providers cases a challenge in data consistency and accuracy.
An example given was that different plants in Mexico are sharing some of the same suppliers, but only each individual plant has visibility of their supply chain, so optimisation and efficiency opportunities are being missed.
September 25
First session kick off with Mercedes Figueroa, Christoph Seitz, Gabriel Mair, Jim Mancini and Christopher Ludwig
In our first panel session, we are joined on stage by Mercedes Figueroa, vice-president of Logistics, Stellantis North America; Christoph Seitz, global vice-president, Finished Vehicles, DP World; Gabriel Mair, Commodity Procurement director, Transport/Logistics and Capex, GKN Automotive; and Jim Mancini, vice-president, North American Surface Transportation, C.H. Robinson.
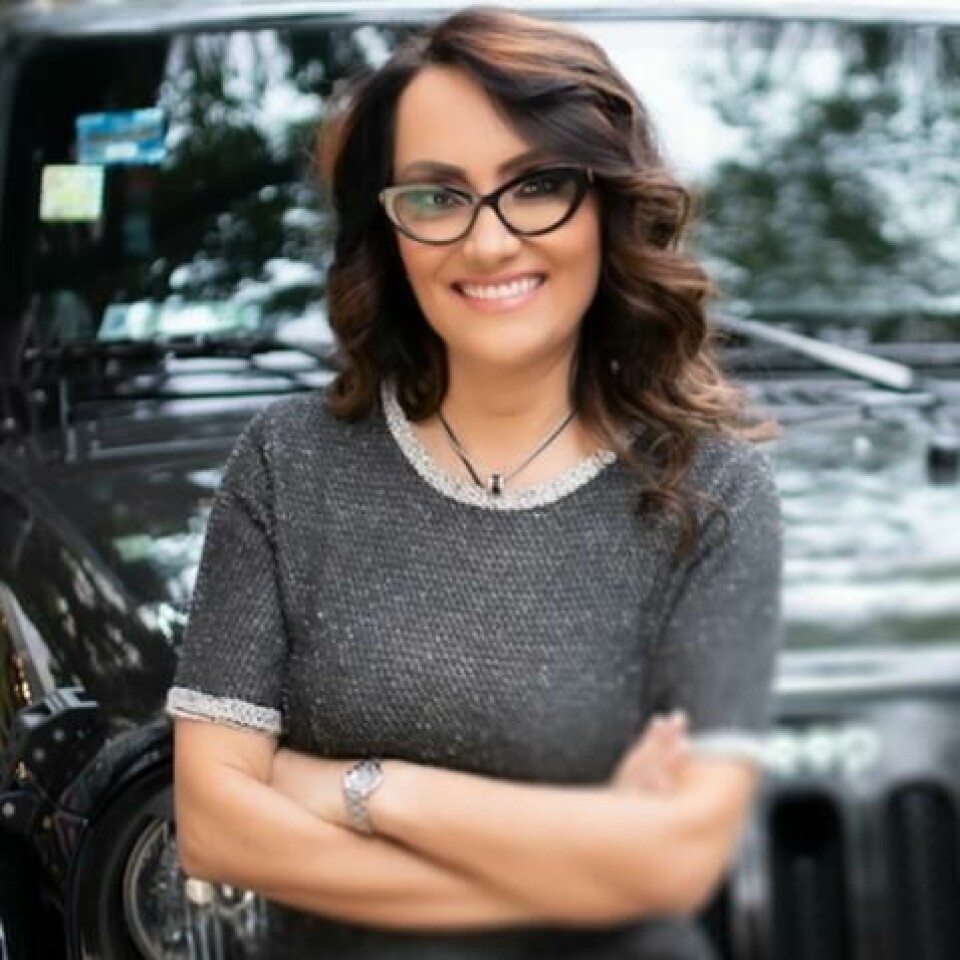
The panel are discussing collaboration within the logistics industry, particularly between OEMs and logistics service providers, which has seen a positive boost in the last few years.
Stellantis’ Figueroa said that collaboration and communication has mostly improved. “There is still a little roadblock we have to overcome in terms of legal and the right way to communicate and share data,” she says, “but we have talked more in the last two or three years, even in these conferences about sharing network capacity, for example.”
DP World’s Seitz says: “I’ve never seen the level of collaboration between the OEMs and service providers as I have in the last year and a half or so. It’s very encouraging and I hope it will last a long time.”
Mair from GKN Automotive says that it’s important to have a commitment internally with stakeholders but also across service providers. “By having the baseline in place, we have a positive experience and a positive mindset.”
Figueroa adds that in this communication, digitalisation and data is an important focus: “A good example is seen in collaboration across difference service providers, where they are putting together projects.” She says that in some cases, for example, service providers are looking at where rail ramps could be placed in areas of significant need by automotive OEMs and even OEMs from other industries.
“Their ability to ground that with facts and say what is going to be the benefit for us and the others involved is so important,” she adds. “So the final benefit is tangible with data.”
25th September
Welcome by Chief of Content Christopher Ludwig!
Welcome to the first day of Automotive Logistics and Supply Chain Global 2024! Christopher Ludwig, Chief of Content, Automotive Logistics is first on the stage to kick off today’s panel sessions.
Throughout the next two days, we will discuss with logistics experts how you can master complexity to control your supply chain destiny – something that’s ever more important as complexity increases.
“It goes without saying you’re facing significant disruption from weather, strikes and the market,” Ludwig says. “On the logistics side, we’re looking down the barrel of what seems like a probable strike [on the east and Gulf coast ports]. Whether it lasts from several days to weeks, the impact across the supply chain will last considerably longer than that. It’s part of a trend, we saw the west coast impacted by the Canadian rail strikes, and last year the UAW strikes. If you’re not pulling forward months in advance it’ll be difficult to react without flying parts around.”
In Mexico, nearshoring trends continue, while the US Mexico border continues to face delays. And across North America, all these problems are compounded by market disruption, a mismatch in forecast demand versus actual demand particularly in EVs, and OEMs facing challenges including profit warnings and financial issues which is felt across the logistics network.
All of these problems mean that competitiveness of logistics has become essential, and a resilient and flexible logistics network is a strategic advantage. There is an intense focus on flexibility, with digitalisation playing a huge supporting role in this, though data science and analytics and how it’s used in demand and supply planning and risk monitoring, and master data strategies. But these things take investment, and the industry is experiencing a cost reduction-investment paradox. Over the next couple days, we will discuss how to invest in these massive data strategies and transformations, through partnerships and through cutting costs, while still increasing value.
September 24
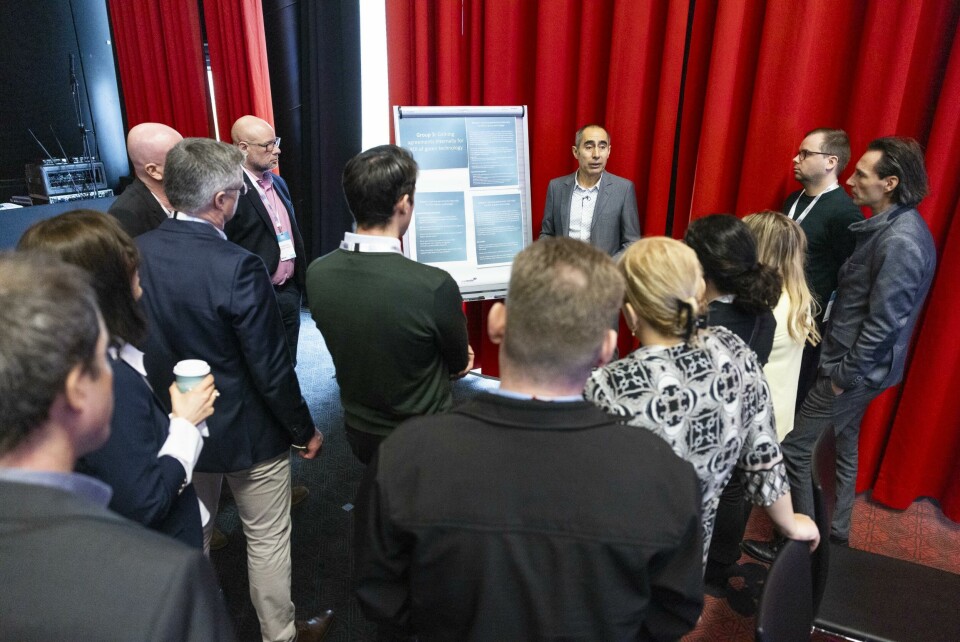
Over the next two days, one of the main focuses of the event will be on making automotive logistics more sustainable, and enabling the scaling of green logistics technologies throughout the North American supply chain network.
Six months ago, at our ALSC Europe event in Bonn, Germany, Automotive Logistics held a Sustainability Ideas Lab where experts from JLR and Mercedes-Benz led discussions about steps the industry can take now to help drive sustainability innovations and partnerships.
September 24
And it’s here! The event is kicking off today with a pre-conference round of golf day, sponsored by DP World, followed by a welcome cocktail reception, hosted by AXLE Logistics.
The next two days will see experts from the automotive logistics space get together to discuss how supply chain organisations are navigating complexities by optimising operations, digitalising processes, and adopting green practices. Through multiple panel discussions and workshops, leaders and experts will also explore the evolving roles of logistics providers and technology specialists in supporting manufacturers with innovative solutions.
We are set to see speakers from companies including GM, Stellantis, BMW, Volkswagen and Nissan who will cover different sessions on 25th and 26th. Click here to see the full event agenda!
You can still watch everything in action virtually through our multiple streams. Click on the link below before it’s too late!
September 19
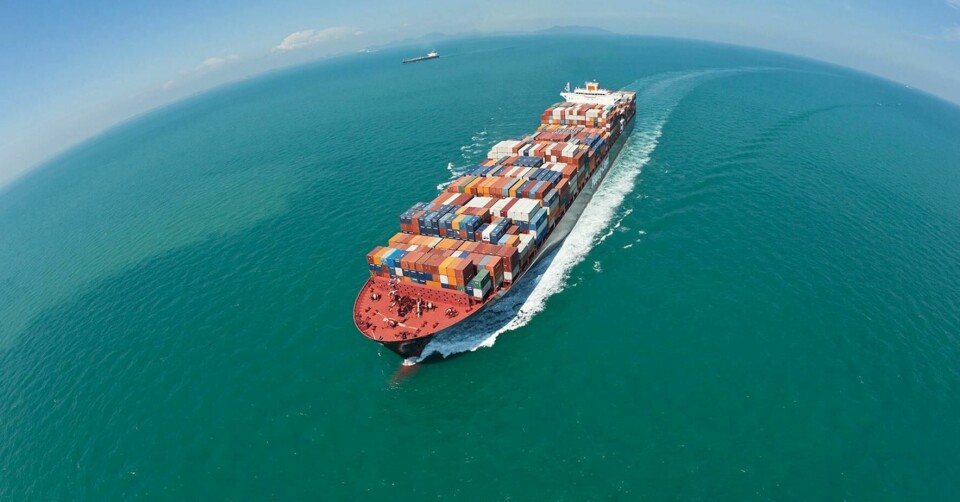
Ahead of our event in Dearborn, we will be sharing news and features in this live blog that relate to the topics and speakers that will be focal points at ALSC Global 2024, including shipping and port capacity in the North American vehicle logistics network.
A challenge sure to be addressed on the stage is the upcoming potential US east coast and gulf port strikes, as the International Longshoremen’s Association (ILA) gears up to strike on 1 October if an agreement is not reached with the United States Maritime Alliance (USMX).
Automotive Logistics is back with this year’s Automotive Logistics and Supply Chain Global 2024, at the Henry Hotel in Dearborn, Michigan. If you haven’t already, click below to register for the livestream to be a part of the must-attend event that will feature multiple panels, presentations, interactive workshops and roundtables, uniting experts and leaders in the industry includingJeff Morrison from GM, Mercedes Figueroa from Stellantis, Dr Ulrich Wieland from BMW Manufacturing Co., Paulo Monteiro from Volkswagen Group of America Chattanooga Operations, Gerardo de la Torre from Nissan Group of North America and Jessica Hanson from Bosch North America.