Audi’s logistics part 2: Pursuing practical progression
There is little question that finished vehicle logistics has been among the least automated segments of the overall automotive production and supply chain process. From loading and unloading vehicles to and from trucks, ships and rail wagons to inspection and parking, as well as scanning vehicles into inventory and tracking systems, outbound logistics has remained, by and large, a manual, labour-intensive operation
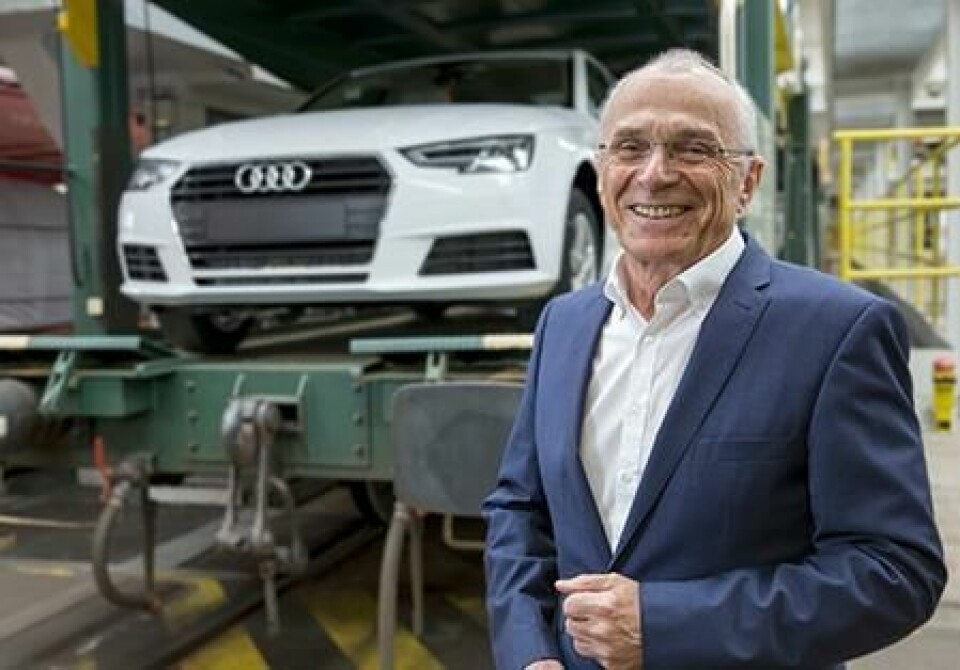
Audi’s logistics part 1: Prepared for a new reality
There is little question that finished vehicle logistics has been among the least automated segments of the overall automotive production and supply chain process. From loading and unloading vehicles to and from trucks, ships and rail wagons to inspection and parking, as well as scanning vehicles into inventory and tracking systems, outbound logistics has remained, by and large, a manual, labour-intensive operation.
Just as obvious is how much this could dramatically change in future. The eventual rollout of autonomous vehicles and trucks could automate loading, delivery and many yard and storage operations. Artificial intelligence within a connected vehicle, meanwhile, could effectively take over planning, scheduling and even accessory installations, as vehicles decide for themselves which parking spot or workstation they should move to next, and which mode of transport they should use to reach their final destination.
While such levels of autonomous driving and machine learning may not be so far off, the point at which vehicle logistics sees such radical transformation is far from clear. To make large-scale industrial operations such as loading and inventory management effective, operators typically require homogenous processes across the thousands of vehicles a given plant or port may handle each day. Having just a few vehicles capable of parking themselves, or a portion able to communicate with each other via mobile networks, will not immediately offer huge potential.
In a fast-moving but low-margin operation like vehicle logistics, the scope for large investments in new systems and bespoke technology is inevitably limited.
Such financial restrictions are perhaps most evident in the fact that even in areas where software offers fast optimisation, such as yard and transport management, many carmakers and vehicle logistics providers still depend on manual calculations or spreadsheets.
The transition to new technology raises questions over how carmakers and logistics providers should manage the change from traditional operations to highly automated vehicle logistics. What, if anything, comes in between, and how fast should the industry adopt new processes and equipment?
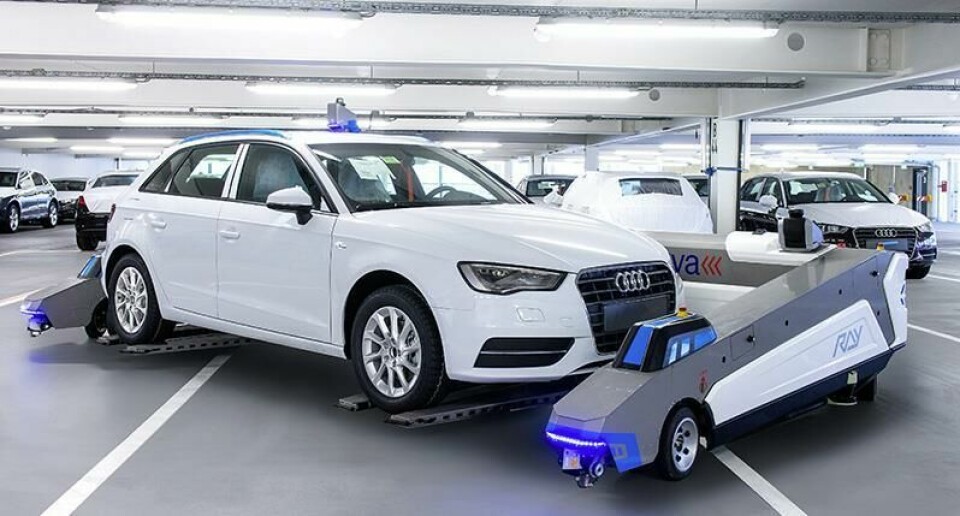
Audi’s digital moves
One example can be found at Audi, which has already broken the mould when it comes to automation and advanced processes in vehicle logistics, both in physical operations and in planning and scheduling. Although Audi, together with the Volkswagen Group, is investing heavily in autonomous vehicle technology, its brand and plant logistics teams are not waiting until all vehicles have achieved level four or level five autonomy to change vehicle handling and loading operations.
Instead, over the past two years, the carmaker has been increasing its use of specialised transport robots which autonomously collect and sort finished vehicles within the carmaker’s Process House, a multi-storey storage and loading facility at its plant in Ingolstadt, Germany, Audi’s largest factory and its global headquarters.
The so-called Ray system, which consisted of just two automated guided vehicles (AGVs) in 2015 but has since grown to 12 , currently handles almost all of the vehicles bound for rail transport from the plant. According to Dr Michael Hauf, Audi’s head of Markenlogistik (brand logistics), which is responsible for all logistics processes including vehicle handling and distribution, it has successfully reduced walking distances for employees and improved overall productivity at the Process House.
“The Ray transportation system is a valuable temporary technological solution until all cars have autonomous driving functions,” says Hauf.
Automation is not the only focus for further digitalising vehicle logistics. According to Hauf, Audi, together with Volkswagen Group’s central logistics department, Konzernlogistik (group logistics), is investing further in central planning systems for managing outbound capacity and vehicle visibility across all brands. Audi is also looking specifically at rolling out RFID and self-service terminals for truck arrivals and departures at plants.
The carmaker’s brand and plant logistics are also working together with data teams, including at Audi’s plant in Neckarsulm, in south-west Germany, analysing timings across each stage of production to predict more precise release times for vehicles to truck carriers. Instead of notifying carriers that a vehicle is ready for collection only after production, and giving them several days to collect it, the plant can now inform carriers a day in advance of release and with a timeframe of 2-4 hours for pick-up.
“We do this via analytical tools, with a dedicated big data team of four doing calculations and using new project management methods, such as ‘Scrum’,” says Johannes Marschall, head of plant logistics at Neckarsulm, who is closely involved in the project. “It is really a blending of work between brand logistics, plant logistics and our data team.”
Like other carmakers, Audi is also studying carefully how to improve visibility in the outbound supply chain, including through the use of in-vehicle telematics and satellite tracking.
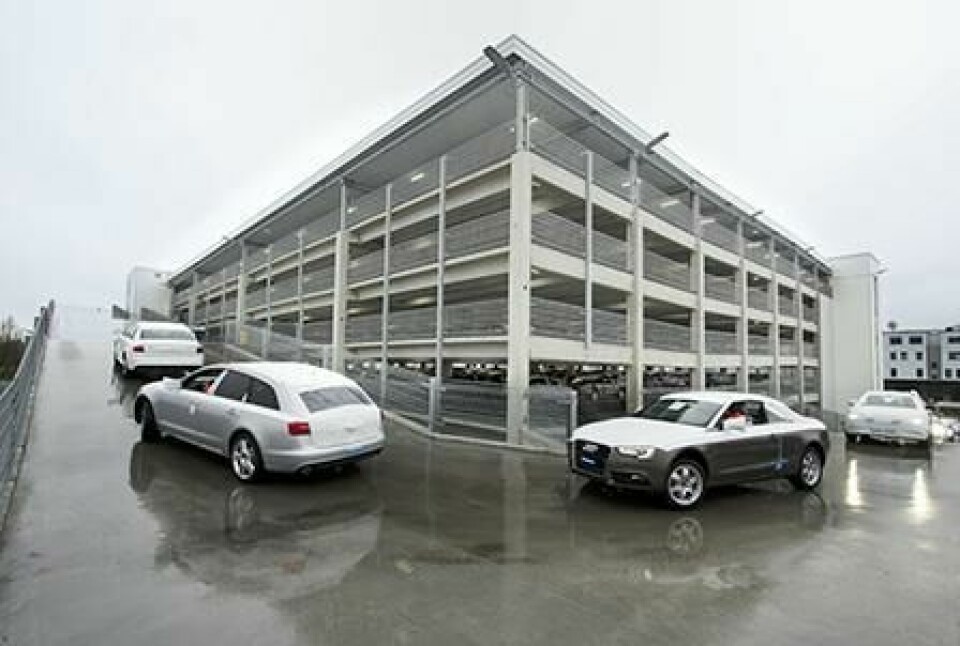
While these and other projects demonstrate how vehicle logistics can benefit from digitalisation, Audi is not pursuing investments in these projects just for the sake of using new technology. Instead, the systems are in response to business cases to solve specific issues and improve productivity. Plants like Ingolstadt, for example, have very limited space and thus make use of multi-storey car parks, which has made the use of Ray robots more optimal. Likewise, a shortage of truck transport across Europe has made it vital to have better forward visibility and maximise available truck capacity. And while improved vehicle visibility is a priority, Hauf stresses that Audi will only go so far as what works for customers.
“There is and must always be a strong business case when implementing a new technology,” he says. “The only goal is to increase the overall benefit for customers, whether in reducing delivery time or lowering overall transport costs.
Ray of innovation
The Ray transport system, which Audi has developed with Bavaria-based robotics firm Serva, is a rare example of using advanced robots in vehicle logistics handling. After a successful pilot, the project has moved into serial production.
The Ray system currently operates on the first floor of the Process House. Vehicles that are cleared from the assembly line are moved manually to the Process House lift, which takes them to the first floor for inspection. From there, Ray transports each vehicle to an interim storage area, from which point Audi’s systems designate their position according to destination. The AGVs then move the vehicles to their designated slot – for example, on the outside right for the US, or outside left for different European destinations. Once there are enough vehicles positioned for a rail wagon load, Ray sorts them again into the best shipping order based on their delivery allocation. From there, the vehicles are manually driven to a lift, which partly automates loading onto rail wagons.
Prior to Ray, employees in the Process House walked to and from each of the vehicles they moved, but the system has reduced these walking distances considerably. Currently, the AGVs carry out around 8,000 daily transport moves. The system is able to handle up to 2,000 vehicles per day moving each in and out of the Process House.
Each Ray unit consists of a six-metre long, three-metre wide frame equipped with laser-based navigational guidance technology. The laser sensors are used to scan cars at a defined transfer point to determine their exact position and dimension. The AGV then adjusts its lifting mechanism depending on the vehicle’s size and carefully lifts it using forks under the wheels.
Within the Process House, Ray uses RFID tags to identify and verify the vehicles that it moves. It also uses a laser scanner to navigate across the floor inside the building, which includes a number of tight and narrow areas. After working out some initial, minor issues, Audi’s logistics team reports no issues with damage in vehicle handling or in the AGVs navigating the floor space.
“There is and must always be a strong business case when implementing a new technology. The only goal is to increase the overall benefit for customers, whether in reducing delivery time or lowering overall transport costs.” - Dr Michael Hauf, Audi
The Process House includes an automatic battery charging station as well. When batteries need recharging, the AGVs move to the charging station, which exchanges its battery in under two minutes, leaving the low battery to charge in time for the next AGV.
The Ray system and the sorting operation is constantly monitored via a control room onsite, which includes a digital visualisation of the floor, with tracking of every AGV by colour. The system allows the Audi logistics employee to monitor the entire process, from handover at the assembly line through to the sorting process and rail loading.
According to Michael Hauf and the vehicle logistics team on the ground in Ingolstadt, while the operation has proved effective, Audi also has the flexibility to carry out sorting and vehicle movements manually during peak periods. “We are very easily able to add manual processes back in and always have that as a backup plan,” says Hauf.
A number of updates are in development for the project as well. Currently, the AGVs are only useable indoors, as Ray uses a laser scanner for navigation, which would be difficult to duplicate outdoors. Mixing the AGVs with other general traffic, such as truck carriers for loading or other vehicles driven for inspection or other processing, would also require much more development. The current robots would also not be able to operate in the rain or snow. According to Hauf, Serva and Audi are discussing the development of an outdoor version, but it is still in ‘Kinderschuhe’ – at very early stages.
However, Ray still has further uses in its current form. There are plans to expand its use to cover all floors of the Process House in Ingolstadt, for example, while Audi is also preparing to install similar systems in other factories. A version of the system is likewise being developed to move containers and other large items, such as electric batteries.
A big data pearl for yard management
Just as Ray is a useful solution for dealing with space limits at a number of Audi plants, the carmaker is also looking to new technology and IT processes to help manage shortages in space and capacity. With the recovery of the European market in recent years, for example, Hauf points to shortages of truck capacity in Europe.
Audi has an advantage in that more than 70% of the vehicles it builds at its European plants move by rail, including around two-thirds of production to the port of Emden in northern Germany, which is the Volkswagen Group’s primary finished vehicle port in Europe. However, for destinations that are not served by rail, or in the face of strikes by rail drivers or disruption – including several accidents and major storms that have hit northern Europe in recent months and virtually shut down the rail network – Hauf points to “tremendous problems” securing truck service quickly.
The main issue, according to Hauf, is not necessarily with the number of trucks available, but rather with driver shortages in central and western Europe. “The driver shortage is currently our biggest problem in outbound logistics and so within the Volkswagen Group, we have had to focus on solutions,” he says.
One way in which Audi has been able to improve resource management for vehicle logistics is a new process that allows for more accurate advanced release schedules for vehicles. Up to now, Audi’s plants, like most of those in the automotive industry, have tended to notify vehicle carriers that specific vehicles are ready for dispatch only once they have cleared ‘checkpoint eight’ – the point at which the manufacturing team approves the vehicle from the assembly line and hands it over to the vehicle logistics team. Once the carriers are notified, they usually have up to 48 hours to pick up the vehicle from the plant.
Notifying carriers after production has traditionally been the best way to ensure carriers build optimal loads based on actual volume. Although Audi has a stable production system, which includes a frozen period for the production sequence of seven days prior to final assembly, within the plant this order is constantly optimised and adjusted along the assembly line based on capacity, supplier delivery and other constraints. These adjustments mean that it has been difficult to predict in exactly what order the final vehicles will be finished. Without this precision, notifying trucking carriers in advance could result in idle capacity, with trucks left waiting for particular vehicles to complete a full load, if the forecasts prove inaccurate.
At the same time, waiting until vehicles are built also creates slack in the distribution system, with vehicles taking longer to be delivered and logistics providers only dispatching trucks once they are sure of loads. If, on the other hand, the sequence of vehicles could be accurately predicted, it would both reduce overall lead times and also allow carriers to optimise delivery loads in advance.
Achieving this goal, however, depends not just on vehicle logistics, but on accuracy across the entire supply chain. At Neckarsulm, Audi has been running a predictive yard management project that seeks to do just that, thanks to a ‘data lake’ across plant logistics and assembly processes through to checkpoint eight, according to Johannes Marschall.
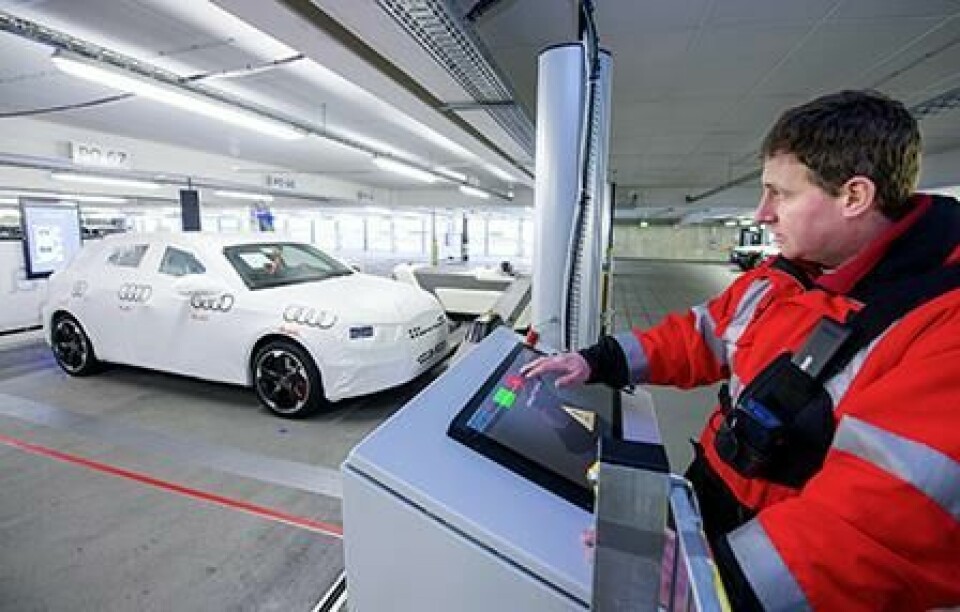
The project has involved collecting and analysing data across all the timeframes within the plant, starting from body-in-white and continuing through paintshop, trim and chassis, and so on, including timings, deviations, changes and disruptions up to vehicle handover. Based on a statistical and dynamic algorithm, Audi predicts when each specific vehicle will clear checkpoint eight.
In between body-in-white and checkpoint eight are dozens of process steps that need highly accurate forecasts of timing if the eventual timeframe is to be reliable. “For example, prior to the handover to vehicle logistics, there is checkpoint six B, when a car is finished but still subject to further inspections,” Marschall says. “Between six B, checkpoint seven and eight, a lot can happen.”
The process is a close collaboration between the plant logistics team, which is effectively responsible for all the materials handling and inventory flow for each process step, and the brand logistics team, which is responsible for inbound and outbound logistics, as well as a dedicated data team.
The project is also in some ways the continuation of a longstanding project at Neckarsulm to perfect ‘pearl chain’ inbound deliveries – or long range just-in-sequence supply. With pearl chain deliveries, suppliers and logistics providers use the seven-day frozen period to pack parts in the exact sequence of production even for material that may be located hundreds of kilometres from the plant. For years, Audi’s logistics and production teams have worked to improve the accuracy and reliability of these production sequences and they have achieved high levels of accuracy in Neckarsulm. Now, with predictive yard management, Audi is effectively “driving the pearl chain throughout the entire production system in the plant,” says Marschall.
The yard management project began in 2016, but has started to bear more fruit since the autumn of 2017, when daily forecasts were rolled out to carriers for vehicle releases 24 hours in advance. “We see, so far, that the forecasts work and that they are helping carriers to handle vehicle loads more efficiently and faster, because we order exactly the trucks that we need, when we need them,” says Marschall. “The carriers have no idle time and almost no waiting time.”
According to Michael Hauf, if the pilot ultimately proves successful in Neckarsulm, it will be rolled out to other Audi factories. “Predictive yard management is an interesting approach, especially where you have a lack of yard space for vehicles,” Hauf says.
There are other areas in Audi’s vehicle logistics that are looking to build data lakes and carry out predictive analytics. The carmaker, together with group logistics, has sought to take the lead in predicting the estimated time of arrival (ETA) of a vehicle across the outbound supply chain, including to vehicle carriers as well as to importers and national sales companies. A week-specific ETA is given to dealers and importers from the point of order, for example, and then tracked and updated across the process chain.
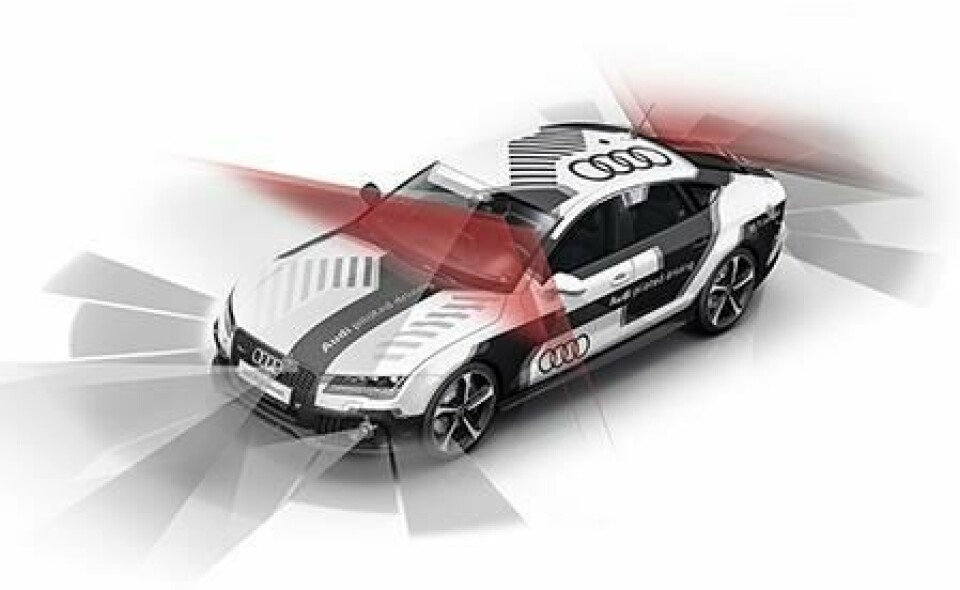
The ETA process covers the entire supply chain, looking at data and timings from supplier ordering and capacity through to manufacturing and distribution of each vehicle. For outbound logistics specifically, Audi also carefully tracks every vehicle within a so-called Liefertreuetisch, or delivery reliability table, which it uses to identify key bottlenecks and delays within vehicle delivery and how they affect promised delivery times to customers.
Recently, Audi has further improved the metrics used for ETA and delivery reliability, including by identifying the main causes for delayed delivery, such as new supplier structures or the ramp-up of a new plant.
“These expected effects are now considered in every delivery date calculation and communication,” says Hauf. “Together with the Liefertreuetisch to identify other delays, we were able to increase delivery reliability from an already high value of 96.4% in 2014 to 97.1% in 2017.”
Connected HERE, there and everywhere
With the inevitable rise of the connected car, including in-vehicle telematics and satellite connections, more manufacturers continue to explore the potential of using these features to track and locate vehicles in the distribution chain. Several industry-wide working groups and associations are currently working on appropriate standards to help facilitate this development.
But Michael Hauf also stresses that Audi is not in a ‘wait-and-see’ mode over using vehicle connectivity as part of its logistics processes. The carmaker is working closely on a real-time visibility service with HERE, a developer and provider of cloud-based mapping services in which Audi holds a stake in a consortium with BMW, Daimler, Intel and other technology partners.
Hauf points to the advantage of working with HERE, which has considerable experience in tracking. With the company’s link to other German carmakers and global IT companies, meanwhile, it is also an obvious opportunity for solutions that work across the sector.
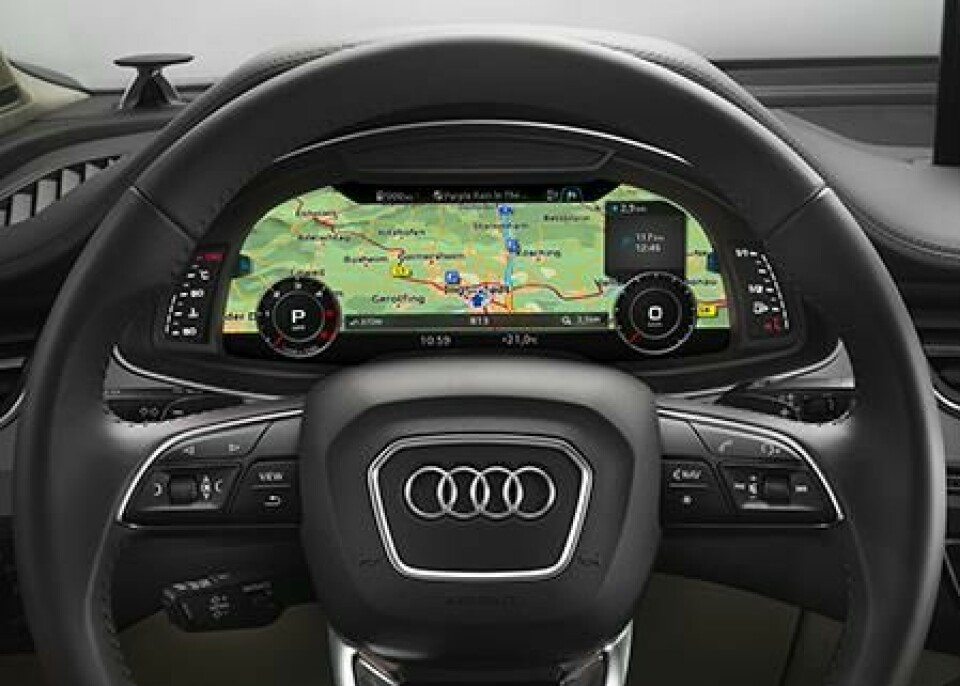
“We’ve recently spoken with the German Ministry of Commerce in Berlin about how German and European carmakers can work together on the same problems,” says Hauf. “For something like vehicle tracking, it would be better to coordinate this at a neutral industry level, such as via the VDA [the German automotive association] or ACEA [the European automotive association].”
While not a competitive issue, Hauf adds that offering advanced visibility to distributors or even end customers must prove to add value, if it is to warrant significant investment. Hauf does see value in having increased visibility at nearly every stage of the supply chain for logistics and production teams, and even for verifying parts and vehicles to regulators and border authorities. However, determining how much of that should be shared with customers has to be done together with the sales division and distributors, he says. Just because it would be possible to show a customer where his car is during the production cycle, such as when it has received an engine, and when it will come off the production line doesn’t necessarily mean it will be valuable.
Such business cases will be determined to ensure investments are not wasteful, including the further rollout of automation such as Ray or predictive yard management. However, the early results of such projects so far have tended to point towards the benefits of a more connected, digitalised vehicle logistics process. If that continues to be the case, as so much suggests that it will, Audi is ready to go further.