Ford changes EV outlook and realigns battery sourcing
Ford has changed tack on its electric vehicle (EV) plans and will now use hybrid technology for its three-row SUVs. The carmaker said it will take a special non-cash charge of about $400m for the write-down of product-specific manufacturing assets for the previously planned all-electric versions, which it will no longer produce.
Instead, the company said it will concentrate on commercial vans, pickup trucks and long-range SUVs for its next generation of pure EVs, vehicles it said that gave it a competitive advantage. Ford will make an electric commercial van at its plant in Ohio in 2026, followed by two pickup trucks in 2027. It said one of those will be a medium-sized pickup based on the platform designed by Ford’s California Skunkworks team and the other will be a next-generation truck to be assembled in Tennessee. Ford set up its Skunkworks team in February to develop a low-cost EV platform.
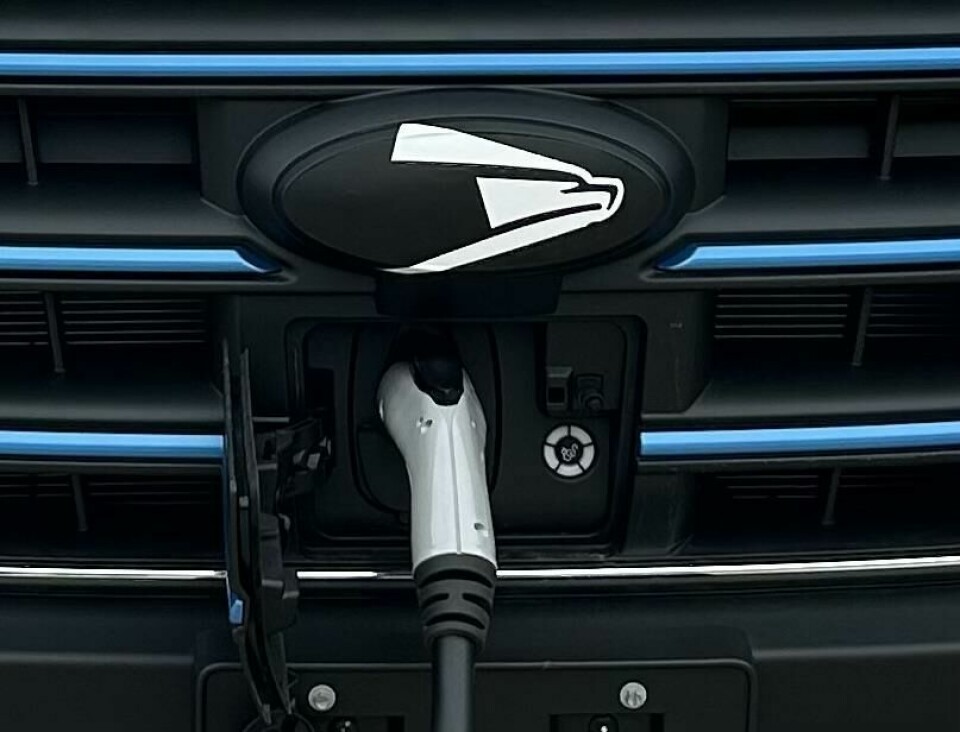
Ford said its mix of annual capital expenditures dedicated to pure EVs will decline from about 40% to 30%.
Project T3
Ford said the next-generation electric truck will build on the success of its F-150 Lightning, the best-selling etruck in the US. It is launching the etruck, code-named Project T3, in the second half of 2027 and it will be assembled at BlueOval City’s Tennessee Electric Vehicle Center. The launch is later than originally planned and Ford said that allows it to utilise lower-cost battery technology and take advantage of other cost breakthroughs while the market continues to develop.
Ford also said the next-generation F-Series Super Duty pickup will have a range of propulsion options, building on Ford’s hybrid truck sales with the F-150 and Maverick.
Battery supply chain
Ford is also realigning its battery sourcing to lower costs for EV production. The realignment is aimed to improve capital efficiency and qualify it for Inflation Reduction Act (IRA) production and consumer tax credits. The IRA, introduced in 2022, has revised and expanded tax credits up to $7,500 for purchasers of certain new EVs. To qualify for credits a certain percentage of the value of the battery components in an EV must be manufactured or assembled in North America. In addition, a percentage of the value of applicable critical minerals contained the batteries must be extracted or processed in the US or in a country with which the US has a free trade agreement, or must be recycled in North America.
“An affordable electric vehicle starts with an affordable battery,” said Jim Farley, Ford president and CEO. “If you are not competitive on battery cost, you are not competitive.”
That realignment in the battery supply chain includes moving some Mustang Mach-E battery production from Poland to the US state of Michigan in 2025 to qualify for IRA benefits. LG Energy Solution makes batteries for the Mustang Mach-E and E-Transit at its facility in Wroclaw in Poland but it also has a plant in Holland, Michigan.
Ford also said that lithium iron phosphate (LFP) battery production will begin in 2026 at BlueOval Battery Park Michigan, which is the US’ first automaker-backed LFP battery plant, qualifying it for IRA benefits and giving Ford one of the lowest-cost battery cells in North America.
BlueOval SK supply
The realignment of the battery supply chain also means the BlueOval SK joint venture in Kentucky will start making cells for the current E-Transit and F-150 Lightning in mid-2025, a move that will delivery significant cost improvements.
Meanwhile, the BlueOval SK facility in Tennessee will make cells in late 2025 for the new electric commercial van planned for production in Ohio. The same cells will used to power the next-generation electric truck to be assembled at BlueOval City and future emerging technology electrified vehicles. Ford said that a common cell strategy gives it a “significant sourcing flexibility for manufacturing across multiple segments and electrified platforms as the market continues to evolve”.
Ford said that market evolution was currently heavily influenced by China, stating that the EV market is “rapidly evolving as Chinese competitors leverage advantaged cost structures including vertical integration, low-cost engineering, multi-energy advanced battery technology and digital experiences to expand their global market share”.