Emergency response: Weathering the storms
A volatile 2017 hurricane season saw successive storms hit the US south-east and the Caribbean, counting at least 500,000 vehicles in the US alone among its many damages and leading to emergency planning once again gaining a greater level of prominence within the finished vehicle supply chain. While matching the claims experience and damage repair responsibilities of the average car owner against those of an OEM or logistics provider carrying new vehicles is an apples-to-oranges comparison, all parties enduring the ravages of storm damage are faced with costly downstream impacts.
For new vehicles, the costs go far beyond repair. If the structural integrity and safety components of the vehicle have been compromised, consumer damage disclosure laws often result in the reclassification of vehicles from ‘new’ to ‘used’. Along with the significant depreciation of an asset, these vehicles may be removed from the new automobile supply chain altogether. Fortunately for many OEMs and their providers, the lessons learned from hurricanes and storms like Matthew (2016), Sandy (2013) and Katrina (2005) underscored the value of developing contingency plans that helped to mitigate the potential impact from the 2017 storm season, which includes the major storms Harvey, Irma and Maria.
[related_topics align="right" border="yes"]“Harvey and Irma resulted in insured losses to property from wind, inland flood and storm surge in Texas and Louisiana in the estimated amount exceeding $35 billion, but the majority of OEMs avoided the large financial losses to inventories in open storage because they heeded the warnings and took proactive measures to reduce exposure to the wind and flooding risks,” notes Timothy Doonan, senior vice-president for Tokio Marine Claims Service.
“OEMs are taking a much more proactive approach to looking at ways to reduce the impact of losses. They are preparing in advance and taking countermeasures to reduce inventory stock in areas of risk,” he adds.
An evolving approach Dr. Hans Bert Bong, former head of finished vehicle logistics for Ford of Europe and now a logistics consultant, points to an evolution towards more proactive management of weather-related events in the automotive supply chain, much of which is already evident on the inbound side. Bong notes that the old approach found supply chain managers focused on reactive rather than proactive measures. Depending on the severity of the event, production could be impacted for varying lengths of time.
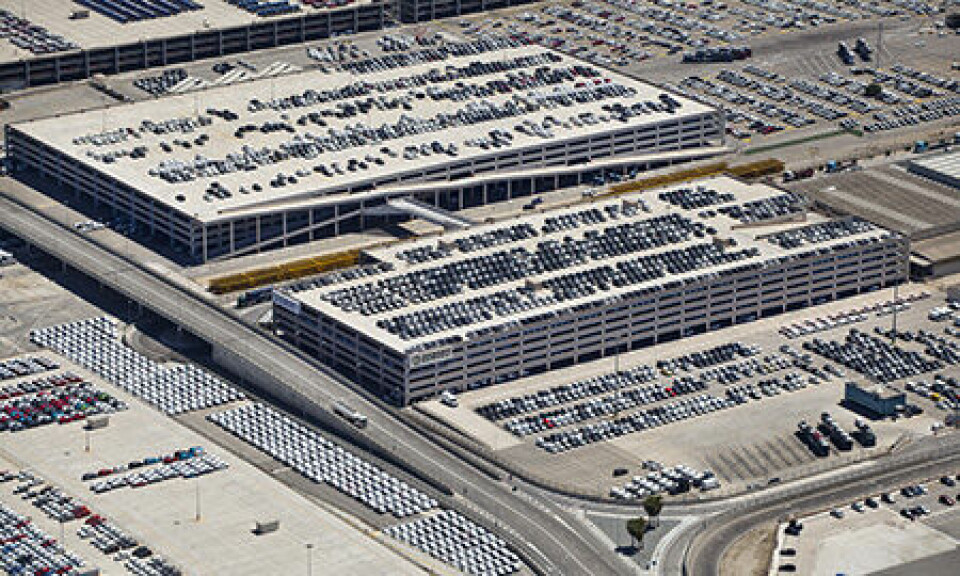
A focus on improving handling methods and storage infrastructure has led European vehicle ports, such as Barcelona, to invest in multi-storey parking facilities
At Ford, for example, Bong points to the use of a sophisticated forecasting, monitoring and action tool that the company started using several years ago, which maps and monitors every node in the supply chain.
The tool can evaluate numerous sources of information and risk categories to paint a comprehensive picture of the robustness or vulnerability of the supply chain, ultimately helping to reduce premium freight, he explains. The benefits of applying such a proactive system in outbound automotive logistics operations are potentially highly significant.
James Sadlier, director with UK insurance claims specialist Sevatas, says such shifts in thinking by OEMs are still taking time to gain traction, however. As he sees it, the automotive logistics market is competitive and price-led rather than risk-balanced. While he believes this market structure may keep premiums lower, he anticipates further changes.
“Insurance has now been able to influence OEMs to act in regard to large loss risks. The next challenge is for OEMs to get logistics providers to think similarly,” notes Sadlier. “The mitigating actions for most OEMs are in their infancy. Sevatas acts for many in developing these and is presently engaged with OEMs at different levels. The initial focus is upon better handling methods, storage infrastructure and maintenance.”
Sevatas has a service covering adverse weather planning that OEMs could pass on to logistics providers, but which, in Sadlier’s experience, is rarely requested even though it has many direct benefits, including those related to large inventories at vulnerable ports.
“Due to logistics synergies caused by seeking cost savings and speedy delivery timetables to customers, we see increased inventories at ports that pose a much higher scale of risk that, in turn, results in large financial loss when catastrophes occur,” adds Matthew Mackintosh, quality assessor at Sevatas. “The problem is that, whilst logistics chains have evolved, the insurance risk assessments sometimes lag behind.”
In Sadlier’s view, OEMs and distributors need to consider the costs and impacts that result from emergency logistics and recovery efforts more carefully in their planning and budgeting. “It is clear from our interaction with many parties that some are better than others at considering the risk, but there is a lot still to do in almost all cases,” he says.
[mpu_ad]Finding coverOne of the most obvious ways to mitigate damage would be to get vehicles under cover – both insurance-wise and also physically. In fact, getting vehicles to safe locations during weather events has become a priority for dealerships. Doonan notes that Tokio Marine Claims Service is seeing an increase in the amount of evacuation claims presented by dealerships. This rise in claims related to moving vehicles out of harm’s way illustrates the cost-versus-benefits issue that OEMs must address when confronting the potential impact of impending weather events.
“There are no easy answers for the OEMs, but we can say there are discussions between insurers and OEM risk management and logistics providers about preparation, planning, risk evaluation and loss-control actions that have resulted in protocols to monitor weather events, escalate preparedness, identify triggers to execute evacuation plans, order vessel diversions and initiate contingency planning with railroads and trucking companies,” says Doonan.
He points out that one of the best ways to minimise exposure for vehicles is to use multi-storey parking facilities, which are common in European vehicle ports but practically non-existent in private and public auto terminal locations across North America. The high cost of construction, combined with the relatively low cost of land in many areas, has so far held back the business case for such facilities in the US, although with changing weather patterns and space issues, this could change.
Open storage, according to Doonan, has increasingly become a focal point for insurance providers as rates have risen over the past few years for OEMs seeking coverage plans for holding vehicles this way. The use of hail nets to cover storage areas has become a more common practice in some locations, for example.
Dealers, auction and rental companies, meanwhile, have tended to lack the scale and centralised inventory to warrant building many protective structures, relying instead on weather prediction resources or targeted protection and repair.
Indeed, fast reaction to damage is still the norm in many cases for manufacturers as well, particularly the use of paintless dent repair (PDR) specialists to keep new vehicles within the supply chain without interruption. Darin St. Ivany, president of Dent-ology, maintains that protecting all vehicles against storms just isn’t feasible. He reports repair operations for as many as 30,000 vehicles in one project.
Even for such response measures, St. Ivany has seen Dent-ology’s clients place a higher value on a proactive approach to threatening weather in recent years. His company has added meteorologists to its team, providing the capability to provide real-time weather information. St Ivany notes that these updates are particularly valuable for rental operations that must mobilise rapidly to get vehicles within shelter. Dealership wholesale insurance entities, according to Doonan, have also placed a greater value on weather alerts.

Steps to mitigate damageLogistics providers are making efforts to better anticipate and respond to disasters, with the recent hurricanes providing prime examples. Ocean carrier and logistics provider Wallenius Wilhelmsen Logistics (WWL) has put proactive protocols in place, including close monitoring of weather forecasts from multiple sources, and working with customers and outbound carriers to facilitate movement to next destination as quickly as possible. WWL now carefully studies its historical notes regarding previous weather events when planning where to move inventory within a location – seeking the highest possible space when faced with potential flood damage situations, for example.
During the 2017 storm season, WWL used a site-based monitoring system, providing visibility on the vehicles in the company’s care with real-time reporting capabilities during, and immediately following, the weather event. Other proactive measures included maximising available indoor storage space and moving as many vehicles as possible into buildings at the company’s facilities prior to a severe weather event. The company also works with its OEM customers to limit the number of vehicles coming into an area threatened by significant weather.
“No two hurricane seasons are the same. Every pre-emptive action is made with our customers’ interests in mind and WWL is constantly refining our processes to meet customers’ needs,” observes John Felitto, president of the company’s North America processing arm, WWL Vehicle Services Americas. “One of the unique challenges of this season was the presence of multiple storms in the south-east and Gulf regions in a short period of time.”
In 2017, Darin St. Ivany and his team at Dent-ology had the opportunity to experience the costs that go beyond property damage when they took an assignment in Puerto Rico, following Hurricane Maria.
Because of the devastation and focus on life-saving shipments to the island, a car rental customer of Dent-ology asked St. Ivany to task a team to get vehicles with windshield and mirror damage back into operable condition so that they could be used to assist in the humanitarian efforts. Dent-ology worked on cosmetic damage to cars in the rental fleet as well.
Dent-ology had to ship its repair equipment ahead of the team’s arrival, with each employee arriving in Puerto Rico limited to one bag apiece weighing no more than 50 pounds (23 kilos).
“We wanted to get things addressed as quickly as possible. The humanitarian effort is obviously the most important effort going on,” explains St. Ivany, who is president of the company. “It was an important job. These companies are trying to provide vehicles to people who are responding to the damage while getting back to some form of normality.”
Car carrier United Road follows a three-tiered approach in its response to hurricanes and other severe storm events, according to the company’s president and chief operating office, Mark Anderson.
The primary focus is on safety, including ensuring that the carrier’s employees and independent contractors are not in harm’s way. United Road also works with its customers to move inventories out of markets that are predicted to be in a storm’s path, and then back in once roads are open and areas declared safe. During the 2017 storm season, the carrier moved a significant number of rental cars back into Texas and Florida, for example.
“Different customers will have different needs depending on inventory levels and market presence,” explains Anderson. “The immediate solution for many customers was to utilise haul-away as a solution to get vehicles into the areas to help their customers get to where they needed to be, and to provide minimum levels of inventory for various dealerships.”
According to Anderson, disruption to rail services also led to a surge in the need for truck capacity. “We were able to locate our assets as well as have many independent contractors reposition their trucks to help move the volumes our customers required,” he says. “The main challenge we faced was the ability to find freight out of these areas, and that issue solved itself over time.”
As participants in the automotive supply chain and insurance entities look to develop improved processes and strategies to address the increasing frequency of severe weather events in an age of climate change, James Sadlier of Sevatas notes that, while it’s impossible to predict the magnitude and timing of individual events, studying past and current storms could reveal hidden trends. The information gleaned from this type of study could assist insurers in establishing limit controls.
“Disasters are chaotic, irregular and uncertain, but discontinuous,” observes Sadlier. “The long-term view becomes more accurate in probability and predictability. Being discontinuous allows the intervention of planning that may benefit loss reduction. And loss reduction starts with routine mitigation in daily operations – actions that seem innocuous until the event does strike.”
"Insurance has now been able to influence OEMs to act in regard to large loss risks. The next challenge is for OEMs to get logistics providers to think similarly. The mitigating actions for most OEMs are in their infancy." - James Sadlier, Sevatas