*This article is part of a special focus on Mexico. For other features related to the automotive supply chain in Mexico click here; for more on finished vehicle logistics in Mexico click here.
In the fourth part of this special Automotive Logistics report, we discover that while Mexico’s OEMs rely on their international links, the local supply base is dense and developed, with a push for even more localisation
Mexico boasts a developed, local supply chain concentrated in clusters close to the US border, around manufacturing sites in Mexico City, Puebla and in the Bajio region that includes parts of the states of Guanajuato, Queretaro, Aguascalientes and Jalisco.
Large OEMs typically have localisation of 80-90% in Mexico, although this varies, Such a concentration allows manufacturers and 3PLs to run a sophisticated network of milkruns and just-in-time deliveries. Nissan, for example, avoids crossdocks for Mexican material, moving all supplies to plant by milkrun or direct, says Sofia Garcia.
Along with strong intermodal players, there are also a host of logistics providers running advanced consolidation, freight and tracking services, including Ryder, Penske, APL Logistics and DHL. “We are very active in milkrun and consolidation activities in the Bajio, as well as Monterrey, Saltillo and Mexico City,” says DHL’s José Luis Garcia. “That is where the market is and the tier one suppliers are.”
Most manufacturers report a push towards further localisation. The new plants, such as Honda’s at Celaya and Nissan’s in Aguascalientes, have supplier parks nearby. GM has a North America-wide strategy to pull suppliers closer to assembly plants, including in Mexico. “Localisation is a priority and in general we would see a trend that material coming from overseas in North America is located closer to our plants,” says Elliot Swiss.
Nissan also has a strategy to bring suppliers closer, with some coming to nearby industrial parks or even on site at plants. “We have had the strategy to bring suppliers to Mexico for a number of years, but on top of that we are using our growth to encourage suppliers to come next to, or inside our facilities, as we do in the US,” says Chris Styles.
Rafael López says that Ford is also trying to bring suppliers closer in Mexico to help manage logistics and engineering changes. “We have a supplier park in Hermosillo that has helped us to be more efficient” he says.
Sofia Garcia believes encouraging suppliers to relocate closer to Nissan plants requires collaboration with material purchasing. “I work together with our supply chain management and logistics team so that we develop and push suppliers to align to our locations as we grow,” she says. “If I tell them to have a yard or warehouse close to the plant, they often do it because they know it is important to our logistics to feed the plant and give us the best service.”
Fiat Chrysler currently has a higher share of international material and logistics for its Mexican production (including from both the US and Canada and outside NAFTA) compared to some other OEMs, as well as to Chrysler’s output in the US and Canada. However, according to Mercedes Figueroa, the carmaker’s purchasing and logistics teams still evaluate total costs for bringing items to point of use, including handling and inventory carrying costs, so the more distant or foreign supply chain is not necessarily the costlier one. “In this way, our purchasing team seeks to optimise the location of the supply base for every component in our vehicles,” she says. “At the same time, there is a minimum region content requirement that we also want to achieve.”
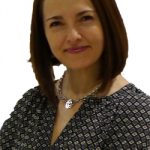
- Sofia Garcia, Renault Nissan Purchasing Organisation
For example, although it included international material, expanding Ram ProMaster production and the engine plant in Saltillo has helped to better fill Fiat Chrysler’s transport and storage assets for Mexico. “We could optimise and maximise the use of our assets like our consolidation centres, even consolidating the shipments of some suppliers that were shipping to the same location,” she says. “That has also helped us to get more competitive rates.”
Such a well-honed network is helping Mexico gain vehicle programmes at the expense of Asia or Europe, and indeed the US. Although some US and Canadian factories were impacted by weather this past winter, Figueroa says Chrysler’s Mexican plants were able to adjust production and delivery, thus avoiding loss of production. It has been similar for Nissan.
Styles adds that such flexibility will be the most important thing for logistics in Mexico. “Our supply chain needs to be able to react fast to the need for sales or manufacturing,” he says. Such a supply chain should be agile enough to jump between Mexico, the US and indeed other continents. If manufacturers can maintain this flexibility, Mexico should be well placed to keep on winning.