Demand for rail transport is growing faster than service providers can keep up with, according to Siegfried Jung, head of planning and steering vehicle dispatch and transport at BMW Group.
[related_topics align="right" border="yes"]Jung says that increased demand for rail transport, from both public and industrial sectors, currently exceeds capacity. Rail infrastructure expansion measures, he points out, “require large investments and have very long planning and building timeframes” – often taking more than a decade to complete – and network providers across Europe have simply “reacted too late to the increasing demand”.
In real terms, suggests Jung, available capacity is shrinking, being further exacerbated by ongoing construction works, and will therefore continue to operate at sub–par levels for some time to come.
Jung adds that the decreasing availability of train drivers is also a factor, contributing to what he terms a “major bottleneck” in rail transport. Increases in the number and duration of recent strikes have made rail movements “more and more unreliable”, he says.
“In the last couple of months, strikes in France and Spain have blocked deliveries to these markets several times. Wagons containing our vehicles had to wait several days, [sometimes] weeks, before they could be moved to their destination,” he adds.
"In the last couple of months, strikes in France and Spain have blocked deliveries to these markets several times. Wagons containing our vehicles had to wait several days, [sometimes] weeks, before they could be moved to their destination." - Siegfried Jung, BMW Group
Other challenges include differences in track widths and rail systems, which limit international and intra–European rail traffic. Jung continues: “Some destinations, for example Koper in Slovenia, are only accessible via one rail track, which makes the route highly dependent on the condition and utilisation of this track.”
Of course, Jung is not the only one battling such difficulties. Frank Schnelle, director of development and planning at Hyundai Glovis, describes ongoing developments to switch more volume from road to rail as “challenging”, given current rail network constraints.
“It seems some networks are already at their full capacity and investment in rail infrastructure is mandatory for further growth. At the same time, pricing is not attractive and competitive enough,” he says.
Schnelle says that since 2016, Glovis has made use of rail backloads for its customer Hyundai Poland, with 88% of imports moving to and from the Koper facility now transported across Poland by rail, compared with 100% by truck previously.
“We operate two block trains a day from the factories to Koper; thus empty backloads are used whenever needed,” he says.
“Future developments will focus on integrating rail operations in dealer distribution systems using a ‘hub-and-spoke’ concept. Especially in times of truck capacity shortage, better utilisation of existing rail equipment is needed to support Hyundai and Kia's ambitious sales plan,” states Schnelle.
Elsewhere, Bernhard Rieder, spokesperson for ÖBB Holding in Austria, reports that the company is witnessing “very high volumes of vehicle flows, which are still growing”, while adding that the sector has “a limited excess capacity for unplanned volumes”.
Networks, ports and compounds are all close to the limits of their capacity, says Rieder, and there are shortages of rail cars as well. Developments over the past few months have only added to the congestion, including the new WLTP (Worldwide Harmonised Light Vehicle Test Procedure), which is causing “uncertainties and short-term traffic volumes for some OEMs”.
Rieder adds: “The necessary infrastructure construction works all over Europe during the summer season also increased unplanned volume and decreased capacity.”
Increasing demand for capacityIndustry consultant Hans–Bert Bong agrees that demand for rail services is growing and points to forecasts predicting that the number of finished vehicles being shifted around the continent could grow by 2-3m units over the next few years – the majority of which will be imports.
“By the nature of this business, those vehicles that arrive in Europe via deep sea – besides a probably limited volume via 'Silk Road' trains – will require ongoing transport in bulk via rail,” he says. “As ports are already congested, they rely on quick clearance of a significant number of units, which cannot be done by truck. However, I have serious doubts that rail capacity will be in line with demand.”
A spokesperson for DB Cargo admits there are a number of key challenges currently facing the European rail freight network. These include high levels of congestion in terminals and ports, leading to “longer lead times and therefore more resources demand – especially for wagons”. The spokesperson also stresses that very high volatility, for example as a result of the WLTP, is leading to “sub–optimal” use of equipment, which can lead to cancellations.
“[These] challenges, [combined with] increasing demand for rail, can lead to lack of resources [such as] wagons, locomotive drivers and locomotives,” says the spokesperson.
Guillaume Quentin, alliance general manager, outbound engineering at Renault-Nissan Alliance Supply Chain Europe, also flags up varying infrastructure across Europe, for example different rail gauges, as a concern, pointing out that this makes it difficult to use the same engine across different countries. He adds that delays and disruptions to services are another problem.
“There is also some capacity missing compared to what we would need, and investment needs to be stronger to avoid derailments and secure assets against flooding,” he adds. “That said, we have no specific difficulty in accessing terminals, except some spot congestion.”
A competitive solution?According to Jung, rail transport remains “highly competitive” for long-distance, high-volume transport requirements, in view of the fact that a train can typically transport 200–250 vehicles, versus seven or eight on a truck.
Despite his belief that rail has the advantage of “enormous economies of scale”, he admits that short-term flexibility is superior with trucks. “Our existing plants are integrated with approximately 60% rail movements. The limits to rail transport are mostly the availability of infrastructure, on and off site, track lines, and loading equipment,” he says.
Hans–Bert Bong agrees that rail is competitive in terms of cost, especially for long-distance movements, but points out that the sector is not so competitive when it comes to comparing average lead times.
In his view, this is due to a combination of variables, including the fact that trains get slowed down by handovers between the various national rail systems when crossing borders. Moreover, he argues, vehicle trains tend to be treated with lower priority than either passenger trains or materials movements, with the latter often forming part of what he describes as a “business-critical lean supply chain”.
“This leads to the fact that finished vehicle rail wagons are assets with reasonably low productivity. Statistics show that, on average, wagon fleets probably get loaded just two to three times a month – the remaining time is used up by the travel, as such, but also by waiting times at OEMs, national borders and empty repositioning,” he says.
Rieder of ÖBB Holding, meanwhile, argues that rail is “absolutely competitive” compared with other modes, “especially in terms of long-distance transport”, giving the example of transport between Europe and Asia, which highlights the speed of rail versus ocean shipping and its cheapness versus air freight.
But he notes that there are challenges ahead: “From the perspective of the rail freight industry, the whole market is changing. Classical industrial volumes are going down [as] new industries increase. Digital business models are entering our industry and more and more players are entering the market.”
Breakdowns and other disruptionsGenerally speaking, Quentin says, the competitiveness of rail for vehicle deliveries is not always a given, especially considering that trucks are more flexible and will deliver direct to the customer, whereas trains involve multiple touch-points and longer lead times.
“Trains are mostly well integrated [at ports] with vessels’ arrival and departure, but having one single train track might increase difficulty due to the fact that loading and unloading in such circumstances can be a very time-consuming process.”
“Truck capacities at destination can also be a challenge from time to time,” he states.
Train cancellations and breakdowns can require trucks to come in and save the day; the converse of the high capacity of trains allowing large deliveries is that 200 units can be stuck on the tracks in the event of problems.
“The fixed network also drives some challenges, particularly where a route change is required,” he adds. By contrast, trucks can use detour roads to reach the same destination.
DB Cargo's representative argues that rail is more likely to be competitive under certain conditions, including where distances are long, road traffic is disrupted or volumes are high. Rail also comes into its own in situations where there is limited infrastructure in the plant, because trucks are, the spokesperson says, “much more space-consuming".
“The integration between rail and other modes is common practice and is not normally a problem. In addition, environmentally-friendly transport is of great importance for many customers – and this is where rail can play on its advantages over other modes of transport,” the spokesperson adds.
A plethora of problems for OEMsAsk OEMs what problems they encounter in delivering vehicles by rail and what kind of backlog these create, and the answers are varied.
[mpu_ad]According to Jung, BMW Group has experienced difficulties with rail due to a range of factors, including its high dependence on the weather, construction works and time schedules for shunting and offloading. While congestion in the German port areas has caused some delays recently, Jung says that any backlogs can usually be caught up “within a week”. Such short–term backlogs can usually be covered by onsite space at plants, although medium–term backlogs may result in a need for external storage, or to deliver them by alternate means, such as trucks. This usually involves higher prices, says Jung.
“Cooperation between OEMs in this area has not taken place so far,” he comments.
As for the long–term challenges facing the European rail sector, Jung argues that the key priorities should include a “drastic” shortening of the long periods typically associated with infrastructure changes, and a marked improvement in the willingness to invest “in the very near future”.
“The reputation of train drivers and the pertaining benefits also need to improve,” he says. “Rail companies have various incentive programmes for career entrants. [But] government subsidies for rail training would be highly welcome and standardisation within Europe would be of great help.”
For the Renault-Nissan Alliance, strikes such as the recent SNCF action have been causing difficulties and delays, although the group only tends to use trains for the initial approach to a destination, with trucks for final delivery. Strikes on the trains put pressure on truck capacity, worsening delays. Quentin believes that communication is key to anticipating problems, “which is actually the norm to protect lead times and avoid delays”.
“Trains continue to be a major development opportunity to further reduce CO2 emissions,” states Quentin. “Although cost is the main driver, along with lead time achievement and quality, the flexibility of the rail sector to meet vehicle delivery needs is not up to expectations compared with trucks. The sector needs to improve its integration and use innovation and technologies to catch up with market trends, for example in relation to track-and-trace technology.”
"Although cost is the main driver, along with lead time achievement and quality, the flexibility of the rail sector to meet vehicle delivery needs is not up to expectations compared with trucks. The sector needs to improve its integration and use innovation and technologies to catch up with market trends, for example in relation to track-and-trace technology." - Guillaume Quentin, Renault-Nissan Alliance
While admitting that LSPs and OEMs occasionally suffer from the after-effects of congestion and resulting delays, the DB Cargo spokesperson argues that the situation with truck transport is the same or even worse, adding: “We work very cooperatively with our customers and we do everything that works to overcome difficult situations. Up to now, there have been no plant shutdowns as a result of plants spilling over with finished vehicles.
“We are investing heavily in personnel – including 1,200 operational people, such as locomotive drivers and wagon inspectors – and modern locomotive and wagon equipment,” adds the spokesperson.
ÖBB's Rieder points out that, in his experience, most congestion originates from the interfaces between terminals and ports. He reports that OEMs are “putting a lot of pressure on the transport industry to keep the factories running”.
Lack of competitionIn terms of the prevailing market structure, BMW's Jung says levels of competition among railway companies and rail transport providers “could be better”. That said, he concedes that the needs of the finished vehicle sector do create some limitations, compared with simple container transport or general cargo.
“The rail equipment-producing companies are very few and new products are only built with long lead times of approximately three years,” he states.
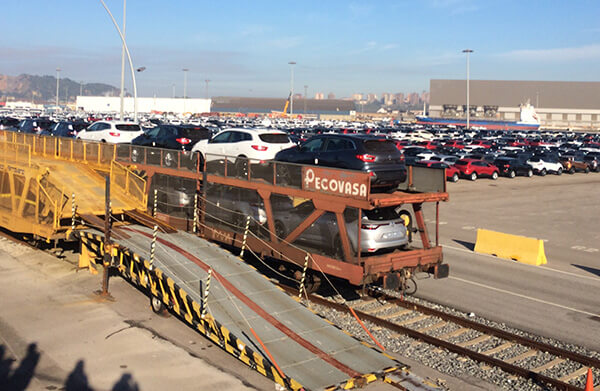
Quentin agrees that there is not currently enough competition in the sector, believing that service could be improved with greater diversity and innovation (see box below).
Bong stresses that rail wagons are “quite investment-intensive” and that rail requires a “much bigger critical mass” – particularly in terms of the number of wagons a rail–based logistics provider must own or operate before it can offer a reliable service.
“Taking all of these factors together – combined with the lower productivity [of the rail–based finished vehicle sector] and low margins – it is not a very attractive business for investors,” he says.
The DB Cargo spokesperson highlights that the extent of consolidation in the sector depends on individual markets, as well as on how authorities implement EU liberalisation efforts, adding: “In some markets, like Germany, we have a good competitive situation – in other countries, such as France, it is more difficult.”
Rieder believes that interoperability is “essential”, pointing out that this depends upon railways conforming on standards of gauge, couplings, brakes, signalling, communications, loading gauge, structure gauge and operating rules. Whereas North American freight railroads are highly interoperable, systems in Europe and Asia are much less so.
However, the EU is working on establishing transnational legal, technical and operational conditions with a view to harmonising the different systems. This will entail the standardisation of infrastructure facilities, train control and signalling systems, plus technical equipment related to traction units, power supply and rail operation. Steps towards this include the European Train Control System and the Global System for Mobile Communications – Railway.
“The aim is to shape the transnational rail traffic in the EU and in third countries so that it is interoperable in order to make rail freight significantly more efficient and faster,” he states.
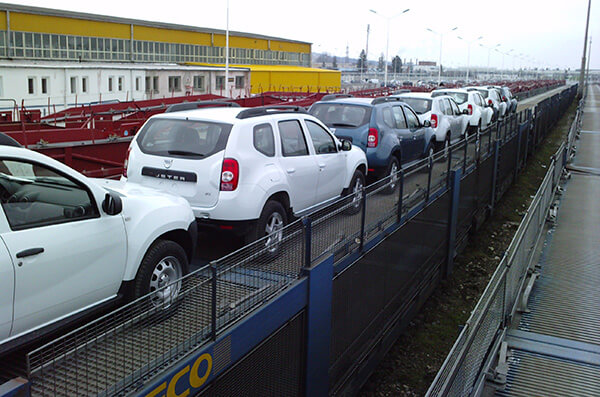
Over the next few years, industry observers suggest, several ongoing innovations and technological changes – including advances in digitalisation and self–driving trains – are likely to exert a growing influence on the rail sector and help make the most of existing capacity.
While a tough investment environment and the high cost of traditional rail wagons lead consultant Hans-Bert Bong to predict that capacity shortages will probably increase, he suggests that one positive factor is the growing trend towards containerisation of finished vehicles.
Although regarded as quite exotic ten years ago, he says, several providers now offer stillage systems for vehicles in containers.
“The advantage of containerisation is that existing transporters and infrastructure can be used and vehicle containers enjoy the same priority as any other container in the system, which offers speed,” he explains.
“Climate change will force politicians, OEMs and LSPs to push for an increase in environmentally-friendly modes, such as trains powered by green, electric energy. This shift from road to rail and water will make demand even bigger,” he adds.
“Automation could also be interesting,” says Guillaume Quentin of Renault-Nissan Alliance Supply Chain Europe, “but there are technical and legal challenges to be tackled.”
A spokesperson for DB Cargo points to ongoing innovations in safety, steering and control systems across rail infrastructure as factors that could also help, effectively increasing capacity by making for faster trains and shorter safety distances between them.
“The equipping of locomotives and wagons with GPS systems and sensors improves steering, utilisation and maintenance. We also assume that the environmental aspect of transport will become even more important for customers in the future. This is where the rail sector can play on its advantages,” says the spokesperson.
Jung notes that digitalisation in finished vehicle rail transport is progressing at a similar pace to that of general cargo traffic. In particular, GPS tracking of rail carriers is being implemented by some companies already and will help streamline rail distribution in the future, he believes.
“Current distribution systems definitely need to be enabled to employ GPS big data. The cargo rail network has high potential for self-driving solutions, due to predictable routes and influencing factors,” he says. “Nevertheless, willingness to invest in self-driving concepts is rather low. Long-term contracts between rail service providers and OEMs could foster greater investment readiness.”
"Current distribution systems definitely need to be enabled to employ GPS big data. The cargo rail network has high potential for self-driving solutions, due to predictable routes and influencing factors. Nevertheless, willingness to invest in self-driving concepts is rather low. Long-term contracts between rail service providers and OEMs could foster greater investment readiness." - Siegfried Jung, BMW Group
Though not yet the subject of much public discussion, Bong says, self–driving trains are an exciting option and one that should be “much easier to achieve than self–driving cars and trucks”. This is mainly because locomotive drivers only control the speed of a train, while the track is controlled and set centrally, avoiding any need for sophisticated navigation.
“We all know examples of driverless airport or city 'sky trains'. It can help to overcome locomotive driver shortages which, next to the assets themselves, are a limiting factor to growth. In addition, regularly occurring industrial action could be avoided.”
Introducing driverless trains could be a tricky business, however, as Bong admits: “Of course, this is quite a political issue and needs to be addressed carefully.”