Aiming to double its engine and transmission capacity by 2018 and with ground to be broken on a $1.6 billion assembly plant, Ford Mexico is counting on a localised supply chain, closer logistics and reduced currency exposure to smooth its explosive growth plan
By the second half of this year, Ford will be constructing three large, brand new plants for engines, transmissions and vehicle assembly in Mexico, all set to open by 2018. Gabriel López, president and chief executive officer at Ford Mexico, marvels at the scale and speed of this expansion across the network and supply chain. The Argentine native has not seen anything like it in his near-30-year career with Ford, which has included roles in sales, service and executive leadership across Latin America and South Africa.
“I don’t think any Ford subsidiary in the history of the company, besides our much larger China joint ventures, has gone through such dramatic paces as we are now in Mexico,” he says.
This investment represents the second major production overhaul in Mexico in less than a decade. When López took over as the local boss here in 2010, Ford Mexico had recently completed another transformation following the global economic crisis. That year, Ford reopened its Cuautitlán plant, outside Mexico City, after converting it from building F-series trucks to the Fiesta compact car for the Americas. At its engine plant in Chihuahua, in northern Mexico, it had also added production of diesel engines to supply large trucks built in the US, as well as a joint-venture transmission plant with powertrain supplier Getrag (which was acquired this year by Magna) in Irapuato, Guanajuato state, in the central Bajío region (Ford now owns the transmission plant 100%).
But that earlier $3 billion investment will be dwarfed by the current plans. By 2018, Ford will have doubled its production capacity for engines and transmissions in Mexico, spending $2.5 billion on a new plant within its existing engine factory at Chihuahua and opening its first, fully owned transmission plant in the country, which will be combined with the former Getrag joint venture into one, large facility .
Later on this year, the company will break ground on a $1.6 billion assembly plant in San Luis Potosi, in the central state of the same name, to build compact vehicles.
Together with his logistics team, led in Mexico by Rafael López (no relation), director of material planning and logistics (MP&L), Gabriel López has put supply chain and logistics at the forefront of the carmaker’s production decisions, sourcing strategy and supplier development. Logistics, he says, was “the primary driving force” in Ford’s selection of San Luis Potosi as the location for the plant.
“San Luis Potosi provided two essential elements,” he says. “It is close to the centre of gravity of the Mexican supply base [and] it has railway access already established close to the plant so that we can ship out directly to ports or into the US.” (See Ford Mexico part 2 for more on the company’s outbound logistics arrangements.)
The site benefits from a dense cluster of suppliers in the wider region, as well as good road and rail infrastructure. In fact, since 2007, Ford has used an important consolidation centre and crossdock close to the site of the future plant.
“This centre is a very strategic site and the only such crossdock that we use [in Mexico],” says Rafael López. “We use it to consolidate parts from North American suppliers to distribute to Mexican plants, as well as for Mexican suppliers for plants in the US and Canada.
“Everything that comes from overseas to Mexican plants and [everything that is] exported globally is also consolidated into this crossdock,” he adds. “It shows how important San Luis Potosi already is for our supply chain.”
Logistics was also critical to the decision to centralise engine and transmission output at the existing sites in Chihuahua and Irapuato. “The scale of production in one place will bring us great benefits,” says Gabriel López.
Along with new production, Ford wants to deepen its supply chain localisation in Mexico. Both San Luis Potosi and the powertrain plants will use “substantially” more parts from suppliers in Mexico compared to existing operations. There will also be greater localisation in Mexico as new models and investments are targeted at Ford’s assembly plants in Cuautitlán, which currently builds the Fiesta, and in Hermosillo, in the north-western state of Sonora, which builds the Fusion and Lincoln MKZ sedans. Such localisation is important especially given the weakening of the Mexican peso, which has fallen 30% relative to the dollar over the past two years.
“We are aiming to maximise the benefits of being in Mexico, and that means increasing local content and being as close to suppliers as we can be,” says López.
A huge task at handFord has yet to determine which models will be produced across its plants over the coming model cycles (see box at end of article), so Gabriel López does not yet have precise volume projections for vehicles or powertrain; but the growth looks set to be explosive.

Adding the new powertrain capacity to Ford’s existing engine output in Mexico would bring Chihuahua, which built 590,000 engines in 2015, closer to the levels produced in the US (which, at around 1.33m engines per year, ranks second globally for Ford behind the UK). However, López warns that the volume can’t necessarily be predicted this way since Ford’s existing lines in Mexico will have different plans and products to those they build today.
“Some engines and transmissions will be replaced by others, and so we cannot yet say what level we will reach, but the growth in capacity is substantial,” he says.
Ford has yet to announce the precise capacity at San Luis Potosi, although López says that a large, integrated plant such as the one planned here, which will include full stamping, press and paint operations, requires at least 250,000-300,000 units per year.
Regardless of the exact figures, the carmaker’s supply chain experts, tier suppliers and logistics partners have a big job before them. Already, Ford’s tier suppliers are building around 30 greenfield plants and 25 brownfield facilities for the new engine and transmission plants, says López. The assembly plants will drive an even more significant migration and expansion among suppliers.

With so much of Ford’s powertrain and vehicle output in Mexico destined for export to the US and Canada, as well as to other markets in Latin America, Europe and Asia, the smooth flow of materials and vehicles to and from ports and the border will only become more critical. After all, while the huge growth anticipated for Mexican automotive production and exports will bring many opportunities, it could also expose gaps and bottlenecks across Mexico’s supply chain, and worsen the country’s chronic traffic and pollution issues.
Traffic snarls in the Bajío Though it would be wrong to say Ford has been late to invest here – it was technically the first carmaker to enter the market more than 90 years ago – its production levels have remained fairly constant over the past five years following its last big changes at the start of the decade. In the interim, other OEMs have rushed into the country. This year, Audi is launching a new factory in San José Chiapa, in the state of Puebla, while its parent Volkswagen Group has launched a new engine plant in Guanajuato and new models from its plant in Puebla. This spring, Kia started serial production close to Monterrey in Nueva Leon. Toyota, Mercedes-Benz and Nissan are also building new plants in the Bajío, while Fiat Chrysler is expanding Mexican production with Jeep output in Toluca, close to Mexico City.
Others are building alongside Ford in San Luis Potosi. General Motors will expand its plant there, which is 5km from where Ford will be, while BMW’s new plant, slated to open in 2019 to build 3-series models, will be next door to Ford in a neighbouring industrial park.
While all three carmakers will benefit from a higher level of suppliers in the region, they will also be sharing, and competing for, the same labour pool, rail and highway access.
Gabriel López and his team see risks to logistics capacity and infrastructure, especially in and around Mexico City, and the wider Bajío, which includes the states of Querétaro, Guanajuato and Aguascalientes, with San Luis Potosi sitting on the northern edge. He also has concerns over key import and export routes by rail and at ports.
“I don’t think any Ford subsidiary in the history of the company, besides our much larger China joint ventures, has gone through such dramatic paces as we are now in Mexico.” - Gabriel López, Ford Mexico
“When you think that Mexican vehicle production capacity is forecast to go from 3.5m units today to more than 5m units by 2020, we worry about how those extra units are going to move around,” he says. “Already today we observe congestion at the ports and the main highways, particularly when you go through the Bajío.”
Such problems have been well documented, from rail and road constraints to shortages at ports, including at the Gulf port of Veracruz, the country’s largest. Mexico’s Secretariat for Communication and Transport has established a national plan for logistics with a significant number of projects planned or underway, including new rail lines and autopistas (motorways), logistics platforms and expanded ports. However, the government is struggling with weak finances following the fall in the price per barrel of oil – an important commodity for Mexico. Some projects have run out of money or been cancelled. For example, a major rail bypass project at Celaya, in Guanajuato, close to Honda’s new plant, has run years over schedule and is now stalled because of a lack of funds.
Worsening urban traffic in Mexico also has impacts on the wider logistics sector, including for Ford. Car use and ownership have been growing faster in major areas, especially Mexico City, than the federal and local government can expand roads or public transport. The resulting congestion and pollution is so bad that this spring the Mexico City government declared a ‘pollution emergency’. Car and truck restrictions were in place at least one day per week between March and June – and in late April and May this went as far as restricting 40% of vehicles on certain days. Other cities, including Puebla, have imposed similar limits.
For Ford and other brands, the subsequent restrictions and congestion impact customers and deliveries of vehicles and spare parts to sales centres. Meanwhile, traffic queues on motorways and secondary roads are both symptoms and causes of delays and disruptions in the supply chain.
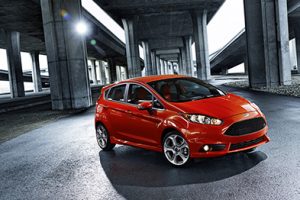
Gabriel López highlights traffic on roads and rail links across a key industrial corridor of suppliers and plants that moves between Puebla, north through to the Mexico City region and onward through the Bajío. “Particularly around San Juan del Rio [in Querétaro] and north, we see levels of traffic which there are no major plans by the government or logistics industry to address,” he says. “We have problems day in, day out receiving material at our plant in Cuautitlán because of congestion from these areas.
“The traffic gets stopped every day, which causes a major problem for trucks delivering just-in-time, leaving us no option but to increase inventories to ensure that the pipeline is never dry,” he adds.
Traffic in this area could also be an issue for the outbound flow of powertrains and vehicles. “We need improvements in the internal nodes of the transport network,” says Rafael López. “For example, we move most of the large engines we build in Chihuahua to truck plants in Kansas City or Kentucky by rail. However, engines that move to Hermosillo and Cuautitlán all go by truck, as they will to San Luis Potosi.”
When trains are stopped in Mexico they become common targets for vandalism or theft, which is causing further headaches over the congestion in the Bajío and elsewhere.
Invest and get smarter Gabriel López calls on the Mexican government to implement its national logistics plan, as well as for port authorities, railways and private firms to invest in the capacity the country requires. He also says that manufacturers have to get smarter about distribution; for example, efforts need to be made to increase night and weekend deliveries of vehicles and spare parts in areas like Mexico City.
Ford also hopes innovations in technology might ease the problem, at least for drivers and consumers. From May to August this year, the Ford Research and Innovation Center, based in Palo Alto, California, is accepting submissions for the ‘Ford Mexico Smart Journey’ challenge, which invites companies and developers to submit apps that integrate multimodal transport options specifically for Mexico City, with cash prizes for the winners. Gabriel López is one of a panel of judges that includes representatives from local government, mobile taxi firm Uber, pedestrian groups and the media.
Despite the long list of hazards, so far the automotive industry has generally avoided disastrous disruptions. However, that may be the result of a temporary reprieve, as Mexican production and global exports have declined this year following slow demand in the US for the small cars built here, the restrictions on Volkswagen diesel cars (many of which are built in Puebla) and recessions in export markets.
Nevertheless, manufacturers continue to build and commit to capacity expansion in the country. Plus, Mexico’s local vehicle market has been red hot for the past two years, growing at a rate of 15% or more per year, including a significant rise in imports. Ford has faced shortages of car carrier trucks for domestic distribution as a result, especially during seasonal peaks.
“At the end of the day, you need to make a call and invest in what is required to meet demand,” says Gabriel López.
The right place at the right time Despite logistics constraints, Ford’s management is confident in its Mexican investments, in large part because of the careful consideration of San Luis Potosi’s location for logistics and suppliers. Joe Hinrichs, Ford’s president of the Americas, says both played a big role in choosing the site. “The supply base, including the logistics network, is extremely important to us when we consider manufacturing locations,” he says.
San Luis Potosi sits at an important supply and logistics intersection. According to Ford data, the north-east region, which stretches roughly from the city to the surrounding area of Monterrey up to the border, is home to the highest concentration of suppliers, at around 32%, while the neighbouring Bajío has 24%.
That is why Ford has already been using its consolidation centre here, which is about 1.5km from the future plant. This combines parts from suppliers into full truckloads for Ford’s Mexican plants, as well as handling intermodal flows and sea containers for export and import material. The crossdock receives 250 loads per week, along with five overseas containers, and dispatches a similar amount. While inbound loads come in the majority by truck, at around 70%, consolidation at the centre means Ford ships 70% by rail (trailers on flatcars).
“Where it makes sense we distribute material directly to plants by full truckloads, but all small or partial loads are consolidated in San Luis Potosi.” - Rafael López, Ford Mexico
“Where it makes sense we distribute material directly to plants by full truckloads, but all small or partial loads are consolidated in San Luis Potosi,” says Rafael López. He adds that Ford is planning to grow the consolidation centre to make sure the area can cope with the expansion in flows to the region when the plant opens.
As the plant will be in an industrial park, some roads and infrastructure are already in place. The local government has committed to building several new secondary roads (though no additional autopistas) and a railway extension to the plant. According to Gabriel López, the government is also carrying out a traffic study to determine potential bottlenecks, given that Ford, BMW and GM will all be in the same area.
The region already benefits from good logistics links however, including both of Mexico’s class one railways. “Kansas City Southern connects 250 metres away from our new plant, while we can also connect nearby to Ferromex,” says Rafael López.
Although one of the two class one railways (yet to be determined) will have a dedicated rail link to the plant’s vehicle yard, the potential of a secondary option could be important for the site’s future outbound transport, adds Gabriel López.
“When we chose the site, we wanted to make sure we had railway options from the start, which is an issue some competitors are facing right now, especially in the Bajío, as well as for Kia in Nueva Leon,” he says, referring to a delayed rail connection at the Korean carmaker’s new plant.

Ford’s selection of San Luis Potosi is also a symbol of the Mexican automotive supply chain’s evolution since the OEM last set up a greenfield plant in Mexico in the early 1990s, when it chose Hermosillo, and Chihuahua a decade earlier – both close to the US border.
Those locations were chosen because almost everything produced at the assembly and engines plants would be for northbound export, and because most suppliers were also in the US. Today, however, the vehicle and engine products are more global – including Lincoln exports to China from Hermosillo. The supply base has evolved from being mainly the maquiladoras that process parts for re-export at the border towards value-added manufacturing across the centre and north-east.
“If we had to decide today whether Hermosillo would be the right place to locate the plant, we would probably make a different call, as we did with San Luis Potosi,” says Gabriel López. “When we established Hermosillo we didn’t know that Mexico would change the way that it has changed, and that so much production capacity would come to the Bajío. That happened later.”
In Hermosillo, Ford needed to establish a supplier park adjacent to the plant to allow suppliers to localise key components. Such an area won’t be needed for San Luis Potosi; nearby suppliers will be able to deliver just-in-sequence, while López estimates that 60-70% will be based within 300km – a higher proportion than Ford’s other Mexican plants.

A bright futureJoe Hinrichs, who ran Ford’s global MP&L department in the early 2000s, thinks Mexico can cope with the expected growth over the coming years. “We are confident the [Mexican] government and the industry, especially the supply base, will continue to make the necessary investments in the future. The Mexican supply base is strong and growing,” he states.
Being on the ground in Mexico might give Gabriel and Rafael López a few more headaches, but they, too, are ultimately optimistic, not least as Ford finds further logistics solutions. Ford will soon start using the port of Mazatlan on the west coast to export to the US. It has also recently started using the port for direct shipments to China.
The rate of supplier investment in Mexico also means that Ford’s production will benefit from closer logistics and reduced currency exposure. Gabriel López is particularly encouraged by what he believes will be more tier two and tier three suppliers growing in Mexico over the coming years.
“Nowadays most suppliers are in Mexico and are in a position to deliver parts here in the right quality, quantity and complexity,” he says.
Such developments are a good sign that the supply chain will help to safeguard Ford’s huge investment in Mexico, rather than put it at risk.
See Ford Mexico part 2 for more on the company’s outbound logistics arrangements.

Mexico is already in the top rungs of Ford’s manufacturing; in 2015 it built 434,000 vehicles and 590,000 engines – fourth highest globally for the company in each category. However, those figures don’t capture the country’s full significance in Ford’s North American and global supply chain. Last year, Ford Mexico exported 412,700 vehicles, including 384,000 to the US and Canada. It also exported 415,000 engines.
Meanwhile, the corporation’s purchasing bill for production parts in Mexico was around $11.5 billion (spare parts would add considerably more to the total), second highest globally for the corporation after the US and ahead of major production bases like China and Germany. Of that total, the majority of purchasing is for plants in the US and Canada, including powertrain supply.
Gabriel López expects Mexico to retain its number two ranking for parts sourcing, even after the company has opened a string of new plants in China. “As we launch the new plants, and increase our local sourcing, that purchasing number will grow substantially,” he says.
With its current investments, Mexico will become a global hub for Ford’s smaller vehicles and low-fuel-consumption models and technology, exporting powertrain units to regions including South America and Asia. More broadly, Mexico will continue to play a major role in the restructuring of Ford’s North American production, particularly in orientating higher cost US and Canadian plants towards more profitable SUVs and trucks, with smaller vehicles focused in Mexico.
This shift began in some ways when Ford moved F-series truck production from Cuautitlán to the US in exchange for Fiesta production in 2010. Last year, Ford also shifted output of F-650 and F-750 medium-duty pickup trucks from a joint venture plant with truckmaker Navistar in Escobedo, close to Monterrey, to Avon Lake, Ohio.
But the biggest changes may still be to come. Ford has already said that it would move production of the Focus and C-Max sedans from its plant near Detroit, Michigan by 2018. Though it has not yet confirmed where they are moving, this would be around the time that the new plant in San Luis Potosi opens. Production of the Fusion in Flat Rock, Michigan is also expected to move by the end of its model cycle in 2018, which could mean increases at Hermosillo, where the model is also built.
Finally, there has been media speculation that an electric vehicle or plug-in hybrid – dubbed the ‘Model E’ in early discussions by Ford and considered a competitor to Tesla’s much-anticipated Model 3 – could also eventually be built in Mexico. Ford already builds hybrid variants of the Fusion and MKZ in Hermosillo.
Gabriel López has not confirmed any of these rumours, although he does acknowledge that stricter fuel economy rules in the US and Canada over the next decade are going to push up demand for hybrids and electric vehicles substantially. Already, suppliers are starting to localise electric and hybrid components in Mexico, including components for the Fusion and MKZ.
“The growth in North America for hybrid and electric cars will require a substantial increase in capacity, including suppliers for batteries, motors and controllers,” he says.