The twilight of global trade?
Globalisation and free trade may be reversing towards regional supply chains for a mix of policy and economic reasons
If there’s one word that sums up much of the last 20 years in terms of the world’s automotive industry, it’s ‘globalisation’. Driven by rising sales in emerging markets, low-cost country sourcing, and the search for economies of scale, carmakers have invested heavily in building international supply chains of finished vehicles and automotive components, not to mention engineering, research and development and software capabilities.
Free trade agreements and a reduction in barriers, both tariff and non-tariff related, have also contributed to these changes. The last 20 years have witnessed China join the World Trade Organization, while the 10 member states of the Association of South-East Asian Nations have grown strongly and the European Union has expanded. There have been bumps along the way. Countries such as Russia and Brazil often seem to go two steps backwards after each effort to reduce barriers. But taken together, trade agreements have contributed to the complex integration of supply chains across a number of regions, from North America to Asia.
In 2016, for example, according to figures from the United States Department of Commerce, the US exported some $56.7 billion worth of cars and light trucks, making it the world’s third largest vehicle exporter behind Germany and Japan. About half of the value of those exports went to the United States’ partners in the North American Free Trade Agreement (Nafta), Mexico and Canada. Separately, the department also published a report in April 2016 that showed the export of automotive parts had almost doubled since 2009, with Canada and Mexico again the destination of almost 75% of those parts – many of which would in turn be re-exported to other countries or back to the United States in the form of finished vehicles.
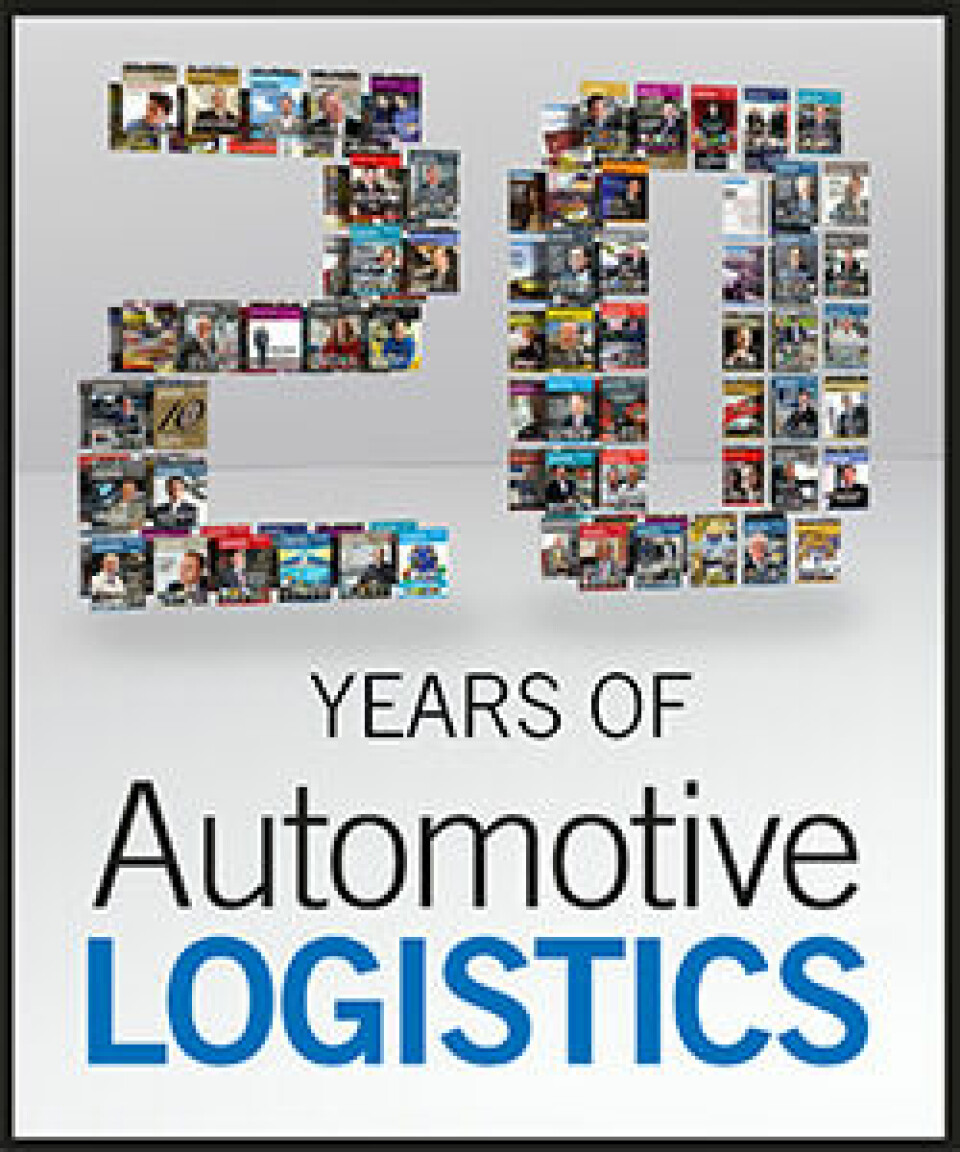
Click here to access more Automotive Logistics 20th anniversary features
Over in the UK, vehicle production has increased to around 1.7m per year, of which over 80% are exported. Yet again, most of these exports go to other EU states, while cross-border, regional supply chains are very much part of the story. According to the Automotive Council – a body set up in 2009 to strengthen cooperation between the British government and the automotive sector – more than half the components in a typical UK-built car are manufactured somewhere else, mostly elsewhere in the EU.
Back in 2013, for instance, Automotive Logistics examined the sophisticated logistics flows that fed Jaguar Land Rover’s UK assembly operations. Operated by DHL, the company’s longtime logistics partner, JLR’s continental European supply chain at the time involved some 40 carriers each week making around 1,100 collections from 480 suppliers in 17 countries, delivering them to the UK via seven consolidation crossdocks across Europe.
Vehicles such as the Land Rover Discovery included shock absorbers from Poland, front lighting from France, coolant hoses from the Czech Republic, an exhaust manifold from Hungary, a climate control panel from Ireland, and fuel injection and power steering from Germany. Transmissions were sourced from Germany and the US, according to type.
The beginning of the end?However, if the last 20 years have been about the integration and choreography of complex global and regional supply chains, might the next 20 years be about dismantling them, with 2016 globalisation’s high-water mark?
For many, the past year has seemed to suggest the tide was turning in favour of the anti-globalisation movement, notably following the UK’s Brexit referendum and the election of Donald Trump to the White House.
The outcome of the referendum in June 2016 continues to pose vexing challenges for the automotive industries of both the UK and continental Europe that many see as a long way from being resolved, despite the imminence of the UK’s March 2019 departure from the EU. Inside or outside the single market? Inside or outside the customs union? The answers weren’t clear a year ago and in large part, they seem no clearer now, worry executives. Despite the UK government’s seemingly reluctant acknowledgment that some kind of transition arrangements will be required, there is no indication of what these will actually be.
"Right across the developed world, there seems to be a growing perception among voters that globalisation isn’t delivering for them... that it’s depressing wages and threatening jobs – the very issues being highlighted in election campaigns." - Richard Gane, Vendigital
“It is reassuring to see the Government recognise the particular importance of customs arrangements to sectors such as automotive, which are subject to rules of origin requirements and operate ‘just-in-time’ processes,” noted Mike Hawes, chief executive of industry body the Society of Motor Manufacturers and Traders (SMMT) after interim transitional arrangements were at last being considered. “However, to maintain frictionless trade and ensure that business only has to adjust to one change, interim arrangements must retain membership of a customs union with the EU and full participation in the single market. Any other arrangement risks additional administration, delays and costs, undermining the competitiveness of UK exporters and increasing the costs of imports.”
Meanwhile, Donald Trump’s protectionist election campaign has again focused attention on globalisation. Immediately on taking office, as promised, he withdrew the United States from the proposed Trans-Pacific Partnership free trade area, a trade deal brokered by his predecessor that was designed to promote trade among 11 Pacific Rim economies collectively making up around one-seventh of the global economy – including Japan, the world’s second largest automotive exporter. He has since also threatened – though as yet without doing so – to dismantle a US-South Korea trade deal and the Iran nuclear agreement, the latter of which has encouraged more countries to resume doing business in Iran.
Openly contemptuous about Nafta, Trump also threatened in his election campaign to withdraw the United States from the treaty, in place since 1994, unless it could be renegotiated. Negotiations duly began in August, with US trade representative Robert Lighthizer charging that Nafta had “fundamentally failed many, many Americans, and needs major improvement. We cannot ignore the huge trade deficits, the lost manufacturing jobs, and the businesses that have closed or moved because of incentives – intended or not – in the current agreement.”
[mpu_ad]Even so, Brexit and Trump aren’t the whole story. For if 2016 was the year in which politicians’ and economists’ long-cherished beliefs were suddenly thrown overboard by many voters in the UK and US, it would be a mistake to imagine that protectionist inclinations weren’t also to be found elsewhere. Witness, for instance, the acrimonious debates seen among politicians in France, Germany, Italy, Hungary and Poland.
“Right across the developed world, there seems to be a growing perception among voters that globalisation isn’t delivering for them,” says Richard Gane, a 30-year consulting firm veteran, ex-automotive manufacturing engineer and director of procurement consultants Vendigital. “The view that’s emerging is that it’s depressing wages and threatening jobs – the very issues being highlighted in election campaigns.”
Politicians on both sides of the Atlantic are pointing to instances of both re-shoring and deferred offshoring as evidence of back-pedalling by automotive companies. Nissan’s chairman Carlos Ghosn, who had raised fears of plant closures if a ‘hard’ Brexit outside the single market and customs union went ahead, appears for the time being to have put such plans on the back-burner, having received unspecified assurances from the UK government that Nissan’s Sunderland car plant, the UK’s biggest single vehicle assembly site, would not be left worse off by Brexit. That said, as a series of position statements from the SMMT makes clear, the rest of the UK’s automotive industry does not feel so sanguine.
Meanwhile, a tweet from Donald Trump on August 4th hailed as a victory for American manufacturing a decision by Toyota and Mazda to build a $1.6 billion joint-venture assembly plant in the United States. With a capacity of 300,000 vehicles, it will employ around 4,000 workers and begin operation around 2021. As with Ford’s January cancellation of its plans to build another plant in San Luis Potosi, Mexico, and instead expanding its plant in Flat Rock, Michigan, the move has been portrayed in anti-globalisation quarters as a vote for re-shoring, and against globalisation in general and Mexico in particular.

Nafta’s supporters are rising to its defence, pointing out that it is the world’s largest free trade area, connecting 450m people, and that its impact on the three nations has been transformative. IIdefonso Guajardo, Mexico’s economy minister, insists that Nafta renegotiations must be about finding ways to make the agreement work better, rather than “tearing apart what has worked”.
Meanwhile, Al Zapanta, president and chief executive of the United States-Mexico Chamber of Commerce, speaks eloquently – in Spanish as well as English, and on both sides of the border – about the fivefold rise in tri-national trade that Nafta has brought about, and points out that US exports to Mexico exceed the country’s combined exports to the UK, France, Germany and Italy. Rather than erect walls, he is instead urging the creation of technology-led ‘smart borders’, and moves to make supply chains flow more freely.
The world keeps turningBut for the automotive industry, if not for other industries, globalisation’s best defence may not be rhetoric and political debate, but realpolitik and cold, hard economics. Global supply chains that have been 20 years in the making, goes the argument, will not be dismantled so easily.
Automotive industry veteran, Stephan Freichel, professor of distribution logistics at Köln University of Applied Sciences, for instance, reckons that the thirst for the efficiencies that globalisation brings will prove to be difficult to quench.
“The search for best-cost country sourcing or production will not stop. As long as the total landed cost – including all transaction costs, customs clearances, and waiting times – points to savings, then the globalisation model will be successful. In the long run, globalisation cannot be stopped as long as customers demand the product that they think they deserve.”
Sven Dharmani, principal and global supply chain leader for automotive at business advisors EY, agrees, insisting that the industry will move away from globalisation only slowly, if at all. “The global model has become too embedded to be dismantled easily: the platforms are too global, and global sourcing has been used extensively to drive down costs. Companies won’t make changes until they have to, and until there is more clarity around tax regimes and tariff rates. And until there is that clarity, it doesn’t make sense to do much beyond some basic scenario planning.”
The recent Ford and Toyota announcements are in some ways a case in point. Since cancelling its Mexico plant, Ford has decided it would build the next Focus sedan for North America neither in Mexico nor the US, but in China. Toyota is going to build more Corollas in the US, but it has not cancelled its Mexican plant, which will build SUVs instead.
"The global model has become too embedded to be dismantled easily... Companies won’t make changes until they have to, and until there is more clarity around tax regimes and tariff rates. [Until then] it doesn’t make sense to do much beyond some basic scenario planning." - Richard Wilding, Cranfield University
Still, Alan Braithwaite, founder of LCP Consulting, a specialist supply chain consultancy now part of business advisers BearingPoint, warns that a rise in tariffs or barriers would make life difficult for many OEMs. “It’s hugely complicated: companies will need to get into an enormous amount of detail, looking at individual tariffs and supply chains flows, if they want to minimise the costs of reducing their exposure to cross-border flows. Even with duty reliefs in respect of imported parts that are then re-exported, tariffs are a significant source of friction, and one that wasn’t there before,” he says.
At its starkest, sums up Richard Wilding, professor of supply chain strategy at Cranfield University’s Cranfield School of Management, the question is one of politicians versus economists, and accountants versus pundits.
“It’s a question of head versus heart and naked protectionism versus supply chain pragmatism – and while it’s the job of supply chain professionals to evaluate all the options, protectionism is a political phenomenon coming up against hard-headed managers,” he says. “And those managers are going to be asking some very searching questions about what is important to them: their long-established investments in highly skilled workforces and advanced infrastructure, or a leap into the unknown. While there’s a lot of uncertainty at present, so far the pragmatic approach is holding out.”
A growing body of evidence, meanwhile, continues to highlight just what protectionism would cost. Leaving Nafta, calculates The Boston Consulting Group in a study commissioned by the Motor and Equipment Manufacturers Association in the US, would cost American carmakers and suppliers $22 billion a year and add an average $650 to car prices. Similarly, in the UK, the SMMT has warned that leaving the single market would result in at least a 10% rise in the cost of imported vehicles and an average 4.5% rise in component costs – before factoring in the costs of trade ‘friction’ such as delays and extra paperwork that leaving the customs union will also entail.
Voters may be unhappy with globalisation, but do they really want to pay the prices entailed in protectionism? At the moment, the jury is out. Carmakers may not be able to wait and find out without taking action – however, 20 years of integration cannot be undone so easily.