The boundary between outsourced supply chain and in-house manufacturing is moving all the time. Where should carmakers draw the line?
For example, many plants use on-site or nearby preparation or sequencing centres, staffed not by manufacturing personnel but by employees of logistics providers and tier suppliers. These facilities conduct quality checks, sort items into the right order to match production schedules and even carry out subassembly activities before delivering parts and modules just in time to assembly lines. Prominent examples would include Toyota’s use of ‘separation centres’ at its factory campuses in the US, which are outsourced to logistics providers, or the sequencing activities managed by a provider at adjacent warehouses to Nissan plants, including at Sunderland, England.
As well as moving activities that were traditionally in the realm of manufacturing out into the supply chain, carmakers are also inviting their logistics providers inside the factory walls, with some, like Jaguar Land Rover in the UK, using logistics staff to bring parts right to the production line, delaying the handover to manufacturing personnel as late as physically possible. The Volkswagen Group is another carmaker that outsources in-plant activities and line feeding to providers. It has had an historical relationship with the Schnellecke Group for in-plant activities, as well as with the Anji-Ceva joint venture in China for Shanghai VW plants. The carmaker has also outsourced in-plant services to providers at plants including Wolfsburg, Hanover and Osnabrück in Germany, as well as in Hungary. [sam_ad id=6 codes='true']
Is this intimate outsourcing an inevitable step in the evolution of an industry that has been vertically disintegrating since the days of Henry Ford? By handing every other activity to functional specialists, vehicle assembly plants can focus their energy on the core function of assembling vehicles. To some in the industry, this is a compelling argument, but to others, it is not a done deal.
In the UK, DHL made the wrong kind of headlines last year when a labour dispute with union employees and contract staff responsible for parts handling activities at JLR plants and logistics centres threatened to spiral into strike action. The dispute was eventually resolved after a largely symbolic half hour walkout, but for a while it looked as if production at Tata’s highly successful UK carmaking business might be disrupted by strike over which its management had no control (neither JLR nor DHL were willing to comment for this story).

Last year, an official at Opel/Vauxhall also told this magazine that “material handling activities are traditionally considered as core for the supply chain and kept in-house,” although the carmaker does outsource some of this activity, including at its powertrain plant in Hungary.
The case for inside outsourcing
The companies with the most to gain from the expansion of logistics outsourcing see feeding the line as a logical extension of their activities. Dick Jennings is vice-president of automotive at Ryder. “As a lead logistics provider,” he says, “everything we do should begin at the point of use on the assembly line, as it is that person who actually adds the value to the vehicle.”
The goal of inbound logistics, whoever is responsible for it, says Jennings, is to present material to the individual on the line at the right time and in the proper amount. For carmakers, giving that responsibility to a logistics provider ensures that “the entire logistics process is seamless all the way from the supplier to the line, with no hand offs or transitions.”
Penske Logistics is another company vying for lead logistics provider work from automotive firms. Terry Miller, the company’s executive vice-president says that his company now does “quite a bit” of in-plant logistics activities for its US automotive clients, including in-plant inventory management and parts follow up, just-in-time line feed and ‘hot shot’ emergency line feeds.
Miller agrees that Penske’s automotive customers differ both in the degree to which they outsource in-plant logistics activities and to which they are willing to give this work to a single service provider. “There are some manufacturers that want to run in-plant work themselves, some who like to have more than one LSP, and other manufacturers who want just one neck to choke.”

- Terry Miller, Penske Logistics
Logistics providers and plant design
Outsourcing of line feeding activities can even extend beyond execution to the design of line-side facilities. According to Jennings, Ryder is increasingly involved in a number of important technical decisions around the configuration of its customers’ production lines, including “ensuring the pick face is safe and ergonomically sound,” which, he says, has implications for the way you configure the work cell.
“You also need to think about what the packaging looks like: you want it to be perfect for the operator, but you also need to keep in mind that packaging may originate some distance away from the line, so you also need to think about part protection and truck cube utilisation.”
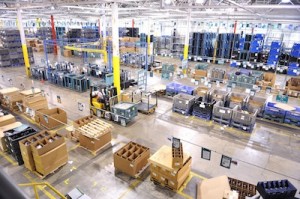
A challenge for service providers in extending contracts to encompass the full range of their capabilities, notes Jennings, is that carmakers often decide on their logistics concepts for new facilities or new programmes before putting those concepts out to tender. “Obviously, the earlier in the process that we can become involved, the more opportunity we have to suggest improvements to car companies. With some of our customers, we are now beginning to have those early conversations.”
This process of ‘engineering before tendering’ seems to have been the experience for Nissan Europe. Engineers at the company admit that they made more efforts during the development phase of the next generation Qashqai to consider packaging configurations and material handling processes, such as sequencing or kitting (assembly of the model began in Sunderland earlier this year). But working directly with logistics providers at this stage still appears much less common.
The case for keeping control
So what of those carmakers that choose not to outsource more activities? One company that has taken a deliberate step back from in-plant outsourcing is Chrysler Group. The company made this change of direction with the implementation of the ‘World Class Manufacturing’ process in 2009 as part of its alliance with Fiat. Marcel Breault, head of World Class Manufacturing, explains that the decision was tied closely to that change in the company’s production philosophy.
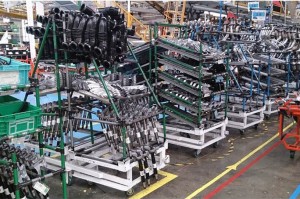
To simplify its line-side areas, Chrysler Group has installed off-line kitting zones where dedicated operators select, check and group parts prior to delivery to the line. Staffing these areas with Chrysler personnel, rather than third-party providers, is a fundamental part of the philosophy. “The people in the kitting areas play a vital role in our overall manufacturing efforts,” says Breault. “As well as moving parts, they are also conducting quality checks, and responding quickly to resolve issues that arise. This approach has been very beneficial for us and been an important part of the significant improvement in our quality numbers.”
Bill Leto, senior manager heading up logistics activities for Chrysler Group’s World Class Manufacturing effort, emphasises the importance of operator expertise. “A key part of our philosophy is the knowledge we are building within the organisation. We want the whole organisation to be able to see waste and improvement opportunities with the same set of eyes. We are creating an environment where the operator becomes a doctor of the product, and understands how every part works. Our logistics operators have the same level of knowledge.”
Insourcing has other benefits in manufacturing productivity improvement programmes. It allows operators to be reassigned to logistics tasks as improvements reduce the need for manpower on the line. Breault also emphasises cost and flexibility advantages inherent in assigning tasks to in-house personnel: “There is always a piece cost associated with doing things outside your plant, so if we ask suppliers to add an additional check or preparation activity, we have to pay for it.”
Chrysler Group’s move to a kitting approach has also delivered safety and ergonomic benefits, as the company moves from the use of forklift trucks to deliver bulk material to line side to the delivery of small lots using trolleys and automated guided vehicles. In turn, the space freed up by the reduction of in-plant inventories is helping the company to boost the capacity and utilisation of its lines, and to insource more activities as productivity rises.
While, for Chrysler Group, the case for insourcing is compelling, its implementation is not universal. “These days, we take a total cost of logistics approach. We ask ourselves what we pay for each part, and how much of the handling we are going to pay for,” says Breault. “In some cases, we have suppliers who are the experts at handling their components and it just makes sense for them to do those activities. Increasingly, too, we are working with our suppliers to help them improve their own performance.”

- Marcel Breault, Chrysler Group
The move towards in-house operations of plant logistics has occurred in other parts of the Fiat world as well. In Brazil, for example, Fiat took over its in-plant logistics activities during 2012 at its huge Betim plant. It will also keep the activities in-house at the new plant it is building in Pernambuco, set to open next year.
And while every carmaker takes a different approach, including for different markets and regions, other manufacturers have expressed similar ambitions to simplify inbound logistics handling. Volvo Car Group, for example, has been taking a number of sequence suppliers back in-house, while Nissan Europe has said that it would reduce its reliance on sequencing in favour of more in-house kitting.
Managing the risks
So how can those carmakers that do choose to go further with outsourcing in the plant mitigate the risks that might come with the loss of direct control of what Ford calls 'production-sensitive logistics'? Ryder’s Jennings suggests that the contractual and reputational pressure on suppliers is enough to ensure they deliver what carmakers need in these valuable but sensitive contracts. “In manufacturing, working perfectly is the ticket to admission. Your performance as a service provider just has to be perfect, there is not room for mistakes.”
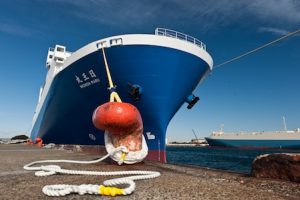
Likewise, there is always some carrot to go with the stick in these agreements, he adds, usually in the form of gain-share agreements for high performance.
Even if they would like to outsource more logistics activity, some carmakers are also prevented from doing so by labour agreements that restrict the jobs that can be handed over to suppliers. Miller notes that the evolution of these agreements can be an important driver in the growth of outsourcing agreements with some customers. “We have seen a steady evolution over the past 30 years: as their labour agreements transition, carmakers often get more flexibility.”
While acknowledging that there is always a small risk of industrial action, Miller adds that labour relations risks can be overestimated. “A major portion of our labour is non-organised and, where it is organised, we have very good relationships with the unions,” he says. “In most cases our associates really take ownership of this kind of work and they are proud to be part of the manufacture of our customer’ products.”
Some in-plant logistics outsourcing also involves a high use of temporary workers or those employed via agencies, for whom the pay is lower and terms and conditions less restrictive than for union or permanent employees. That was at the heart of the union threats against DHL serving JLR plants, for example. In Germany, the use of such flexible contracts is also common. According to a spokesperson for IG Metall, the main union for automotive workers in Germany, there are about 100,000 temporary workers in the country’s automotive plants, while some plants have as much as 50% of their labour force on agency contracts, including for a growing amount of logistics-related tasks.
Industry changes
What part can in-plant logistics service providers play in the industry’s quest for on-going continuous improvement? Pressure for perfect execution in demanding conditions has, says Ryder’s Jennings, been one of the key changes in the industry since the 2008 financial crisis. “Compared with pre-2008 levels, we are now seeing automotive plants working at much higher levels of utilisation. People have reached the stretch goals, and the transformation in the industry has been really impressive. As companies aim for 100% capacity utilisation, the pressure to get material flow right increases.”

– Dick Jennings, Ryder
Penske’s Terry Miller agrees that manufacturers can maximise a plant’s production capacity by using logistics providers for more in-plant services. “More and more manufacturers want to free up space inside their plants to make products, so moving inventory and preparation activities out of the plant makes sense for them,” he notes. “There are often financial drivers too, since they don’t have to carry that inventory, which is good for cash flow.”
Looking at the wider picture, Miller believes that the majority of future efficiency improvements will come from incremental steps rather than revolution. “We have to operate in a lean environment, and to do that we need the right people, the right technologies and the right visibility.”
Suppliers also need to be in the right locations, and here Miller notes that industries recent shift from offshoring to ‘near-shoring’ has had a significant effect, encouraging it to ramp up its capacity in Mexico, for example, to support automotive customers.
Where the automotive OEMs lead, their suppliers often follow and Miller notes that an increasing number of tier one suppliers are now adopting the same in-plant logistics outsourcing approaches. The automotive sector’s influence even extends to other industries entirely. “We now offer the same kind of services to some leading appliance manufacturers, which are enthusiastically embracing automotive industry approaches, in many cases hiring people with an automotive industry background to help them," he says.
Could further outsourcing be the key to the next step change in efficiency? “There are opportunities to change manufacturing systems or supply chains to eliminate several millions of dollars in transportation costs at a stroke,” says Ryder’s Dick Jennings. “But opportunities like that don’t come along every day. In practice, the vast majority of improvements will be delivered inch by inch and bit by bit, with a focus on day-to-day execution.”
Against this background, he concludes, outsourcing as much as possible to their logistics providers allows carmakers to “concentrate completely on the production of the vehicle, and on achieving flexibility against heavy production schedules”.
Additional reporting by Christopher Ludwig.